Wood in civic buildings
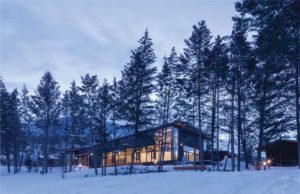
By Jim Taggart, FRAIC
In April 2019, John Horgan, then Premier of British Columbia, announced a new program to incentivize the use of wood in public buildings in an attempt to mitigate the impact on the forest industry of climate change-related phenomena as the rising population of mountain pine beetles and the increased frequency and severity of forest fires.
For public projects, as for other types of buildings, new engineered mass timber products, supported by new legislation, make wood an economic and functional choice in both rural and urban areas. Two recent projects illustrate this point.
This article, based on a newly released case study by Wood WORKS! BC and the Canadian Wood Council (CWC), examines two recently completed civic buildings in British Columbia using wood. In Vancouver, Fire Hall No. 5 is an innovative response to rising land costs and the shortage of affordable social housing. In the Village of Radium Hot Springs, a wealth of local wood products, manufacturing capabilities, and craft skills combine in a community hall and library that can truly be called a ‘100-mile building’.
Fire Hall No. 5
Vancouver has the highest land costs of any city in Canada and, as a consequence, faces the challenge of maintaining an adequate supply of affordable housing. One strategy employed to address this situation is to reconsider permissible density and co-location of uses on city-owned property. Fire Hall No. 5, which combines a new station with 31 units of supportive housing, is one such example. The mixed-use project replaces an aging facility rendered obsolete by new seismic codes and the introduction of larger ladder trucks.
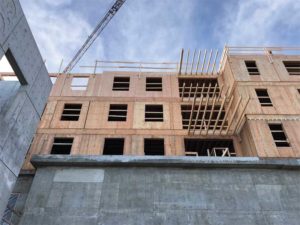
Photo © Johnston Davidson Architecture
The new fire hall includes three apparatus bays, crew dormitories, washrooms, fitness areas, a community training room, and a self-contained breathing apparatus (SCBA) maintenance room serving the entire Vancouver Fire Rescue Service (VFRS). Through a partnership with the Metro Vancouver YWCA, 31 units of safe, affordable housing for low-income, woman-led families and their children became the second component of the project.
Johnston Davidson Architects (JDa) faced the challenge of maximizing the program area within the 18-m (59-ft) height limitation on a tight site, while facilitating fire truck access and separating the fire hall and residential uses. Moreover, the entire building had to be designed to meet current post-disaster standards.
With the corner site facing two streets, it was possible to create two distinct entrances to the building—one for the fire hall off 54th Avenue, and another for the YWCA housing off Kerr Street. This ensures the two organizations are understood by those accessing the building to be separate and distinct. VFRS occupies the first two floors and YWCA occupies floors three to six.
Most of the main floor is taken up by VFRS operational spaces and the apparatus bays where the emergency vehicles are stored. These vehicles leave and return through overhead doors located off 54th Avenue.
The glazed fire hall entry is denoted by its coloured interior and proximity to the traditional concrete hose tower. The entry gives access to a community/training room and washroom, separated from the remainder of the hall by a secure point, making it accessible for community groups. The Kerr Street entry to YWCA residences is also at this level. The second floor is entirely occupied by VFRS and houses the crew dorms, washrooms, and fitness facilities.
Above the fire hall are four floors of housing for YWCA’s tenants, the suite layouts are almost identical on all floors with the exception of the third floor, which also incorporates a common room and laundry. Certified Leadership in Energy and Environmental Design (LEED) Gold, the building provides YWCA, the City of Vancouver, and the occupants with an energy-efficient solution for affordable housing.
The colour and texture of the materials used throughout the building play a role in the well-being of all occupants, and together with large-scale graphics, contribute to easier wayfinding. On the main and second floors where the fire hall is located, access to natural light, exterior views, and operable windows was a key component of the design. This increases the comfort for fire crews and reduces the requirement for artificial light and related energy demand.