Wireless sensors in construction
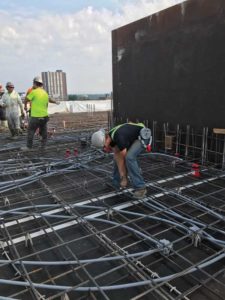
A new generation of sensors
Canada and the majority of North America is approaching a time where much of its concrete infrastructure will reach the end of its life cycle and will need to be reconstructed. New, non-destructive testing technologies have been developed to assess the state of corrosion in concrete, a necessity to ensure safety of aging infrastructure. As concrete infrastructure is renewed, it is worthwhile to consider the use of technology to not only monitor the condition and properties of concrete during the building process, but further along its life cycle. These new testing methods have also to provide more consistent results and improved ease of use when compared with other non-destructive testing methods.
The labour and work demand associated with the assessment and testing of aging concrete is pushing researchers and engineers toward a new generation of sensors with the ability to monitor the integrity of concrete throughout its lifespan. This becomes especially important as the industry considers the growing number of engineering professionals needed to assess infrastructure as it ages.
Fully embedded concrete sensors are being developed to address issues such as:
- corrosion in steel reinforcement;
- deterioration due to freeze-thaw cycles;
- delamination, softening, and erosion of cement due to sulfate-containing waters entering hardened concrete; and
- cracks caused by alkali-silica reactions within the aggregates.
By including condition-monitoring equipment directly into new concrete infrastructure, it is possible to predict failure without having to rely on the high amounts of labour traditionally necessary for adequate testing. This equipment is also giving engineers a more comprehensive understanding of concrete quality and life-cycle activity.
This technology could also provide building professionals with the ability to monitor and ensure structural integrity of concrete while providing data necessary for optimizing manufacturing and fabrication of failure-proof concrete. Future monitoring systems utilizing smart sensors could provide data on concrete temperature, moisture, and humidity levels, as well as chemicals and pH levels. Not only can these sensors be used to ensure structural durability, but they can also provide a basis for monitoring the integrity of structures designed to withstand natural disasters such as earthquakes. Being able to monitor components or entire structures for deformation, stresses, creep, and strains could result in significant savings in time, cost, and resources.
Conclusion
The adoption of sensors to monitor the properties of concrete during the building cycle provides many advantages to stakeholders, just as the adoption of other sensors and technology used on the jobsite can greatly improve safety and sustainability while reducing project costs and the margin for error. The development and adoption of new concrete sensors for the life-long monitoring of concrete properties is becoming essential as we face the end of the life cycle of much of the country’s infrastructure. Including these new systems in infrastructure renewal projects will, ultimately, improve durability and sustainability of concrete as well as reduce the chances of failure of these new structures as they age.
Roxanne Pepin is a digital marketing specialist with Giatec Scientific, an Ottawa-based company developing smart technology for the construction industry. She oversees the planning, production, and distribution of communication materials while co-ordinating online marketing efforts relating to digital advertising as well as website and content development. She can be reached at roxanne@giatec.ca.