Will this concrete help build a better bridge?
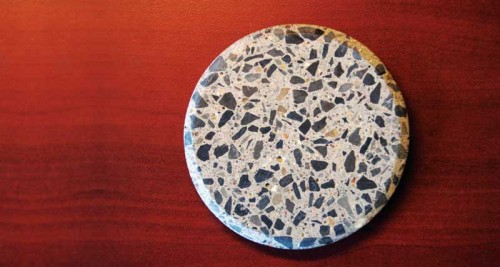
By Daniel Cusson, PhD, P.Eng.
When a reinforced concrete bridge deck is subjected to freeze-thaw cycles and de-icing salts over a number of years, the ensuing deterioration drastically reduces the structure’s service life and results in costly maintenance or early replacement. In such severe environments, high-performance concrete (HPC) is often required because of its superior strength and low permeability.
Unfortunately, HPC also has a tendency to crack prematurely if not properly cured. A more durable low-shrinkage HPC has now been developed at the National Research Council’s Institute for Research in Construction (NRC-IRC). This product can considerably increase the lifespan of bridge decks exposed to harsh environments.
Typically, concrete shrinks when it dries because of a decrease in its internal relative humidity (RH). In normal-strength concrete, typically with high water-cement (w/c) ratio and high permeability, drying shrinkage occurs when moisture is lost to a drier external environment. In high-performance concrete, which typically has low w/c and permeability, this drying shrinkage is not as significant as it is in normal-strength concrete. Nevertheless, significant autogenous shrinkage may occur if there is not enough moisture in the concrete to hydrate the cement particles. This autogenous shrinkage is uniform within the concrete element and can cause cracking if the element is not free to shrink—this is the case for most structures where a new concrete element is cast over an existing one, thus restraining its movement.
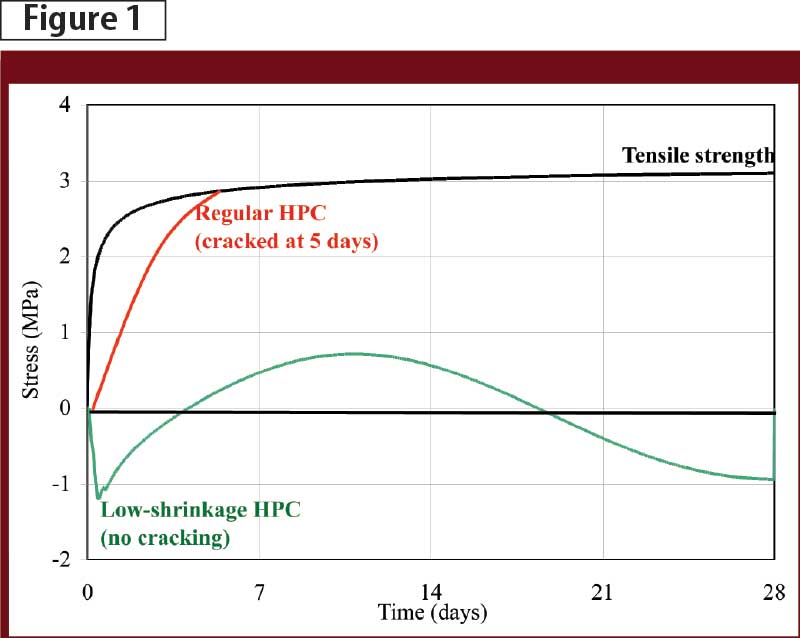
Images courtesy NRC-IRC
The new HPC discussed in this article has been specially formulated to reduce early shrinkage cracking through a technique known as ‘internal curing.’ The strategy consists of using pre-saturated porous, fine, lightweight aggregate as a partial replacement for normal sand to uniformly carry and distribute additional curing water within the concrete. This results in improved cement hydration, leading to a moderate increase in strength and the reduction of self-desiccation and related shrinkage cracking—common problems with regular HPC, since there is typically not enough mix water to hydrate all the cement particles.
Additionally, the new HPC mix formulation combines internal curing with a shrinkage-reducing admixture—also carried by the porous lightweight aggregate—to reduce long-term drying shrinkage. Supplementary cementing materials (SCMs) such as slag and silica fume are employed as partial replacement for cement to reduce the concrete’s permeability, heat of hydration, and carbon footprint. Further, a superplasticizer and an air-entraining admixture are used to ensure ease of placement and high resistance to freeze-thaw cycles.
Gauging performance
NRC-IRC researchers conducted extensive testing to assess the performance of this low-shrinkage concrete formulation to ensure it could surpass expected performance requirements for bridge decks and similar applications. Under controlled environments and severe exposure conditions in the laboratory, the NRC-IRC tests assessed:
- fresh concrete properties;
- hydration and chemistry;
- shrinkage and mechanical properties; and
- long-term durability.
To assess performance under realistic environments, large-size steel-reinforced high-performance concrete slabs—exposed to large temperature fluctuations, wind, rain, ice, and de-icing salts—were cast outdoors. These were evaluated for their resistance to restrained shrinkage cracking and corrosion of the embedded reinforcement.
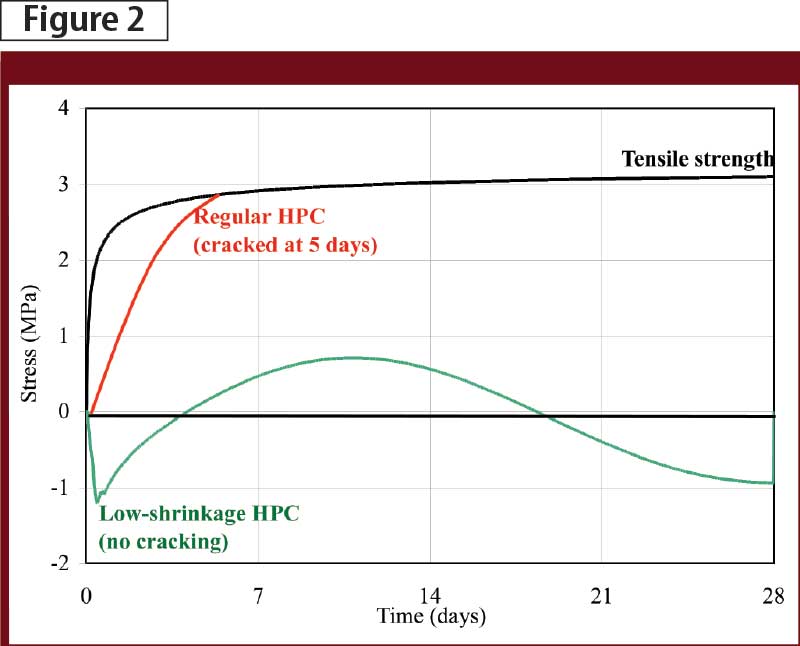
The new HPC mix is expected to deliver a low risk of shrinkage cracking when used in bridge decks. For example, Figure 1 compares free autogenous shrinkage deformations of sealed concrete specimens made of either low-shrinkage HPC or regular HPC. As opposed to regular HPC, which rapidly developed large shrinkage deformations (even under a sealed condition), the low-shrinkage HPC initially developed some expansion in the first 24 hours, followed by negligible shrinkage during the next seven days. In bridges, concrete decks are restrained by the supporting girders; this restriction of movement usually results in tensile stresses that lead to cracking if shrinkage deformations are too large.
Figure 2 compares the development of stresses in large-size slabs made of either low-shrinkage HPC or regular HPC. It shows regular HPC cracked after only five days, while the low-shrinkage HPC developed very low stresses compared to its tensile strength. Additionally, other tests have demonstrated chloride diffusion can be reduced by a factor of two compared to regular HPC, and by a factor of four compared to typical 30-MPa (4.4-ksi) normal-strength concrete. Preventing cracking and reducing permeability is important because this minimizes penetration of de-icing salts and delays the initiation of steel corrosion and related concrete damage, thus achieving long-term durability.
Cost comparisons in Cornwall
NRC-IRC’s low-shrinkage high-performance concrete formulation has been accepted for the deck construction of the Canal Bridge in Cornwall, Ont., with construction slated for the fall of 2012.
The bridge, owned by Federal Bridge Corp. Ltd., is part of the $75-million replacement of the Three Nations Crossing (formerly called the Seaway International Bridge)—a major transportation link between Canada and the United States (Figure 3).
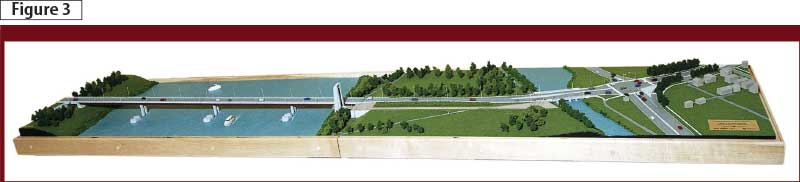
Image courtesy Federal Bridge Corp. Ltd.
The deck of the new bridge will consist of a continuous reinforced concrete hunched slab, carrying three lanes of traffic over four continuous spans. The slab width will be 21.75 m (71.4 ft), and the total length will be 30 m (98.4 ft).
The HPC to be used in the slab of the new bridge will have a minimum thickness of 350 mm (14 in.)—the same thickness employed for a conventional deck design using normal-strength concrete. The reason for using this standard thickness with the new HPC is the bridge design was approved before the NRC-IRC research results became available. NRC-IRC calculations made after the bridge design was approved show the deck design could be further optimized by taking into account the new HPC’s superior strength. For example, the minimum slab thickness could be reduced from 350 to 250 mm (14 to 10 in.), according to the bridge design code, and the concrete cover over the steel reinforcement could be slightly reduced from 75 to 60 mm (3 to 2.4 in.) to optimize the effective slab depth, providing higher bending strength. Figure 4 shows the estimated quantities of concrete and reinforcement required for two compared bridge deck designs. The table illustrates the slab could be built with a reduced volume of concrete and a slightly larger quantity of steel reinforcement, while still meeting the code requirements for strength, serviceability, and fatigue.
Although the unit price of a cubic metre of HPC is typically higher than that of normal concrete (due to the need for more cement, special admixtures, and a higher level of quality control), the slab’s overall cost could be considerably reduced owing to the smaller concrete volume required. For concrete and steel combined, the cost comparison shows a 10 per cent difference between the initial construction costs for the two deck designs.
Since the HPC being used for the Canal Bridge deck will have standard slab thickness and cover, the cost of the HPC and steel combined would be 20 per cent higher than for the normal concrete base case. This cost increase for deck construction materials is still small when one considers the significant savings offered by low-shrinkage HPC bridge decks over their lifecycle.
For example, lifecycle cost analysis showed the slightly higher construction cost of the HPC deck would be recovered quickly (within five years) and recouped several times over the life of the structure (approximately three times cheaper). This is due to the lower incidence of maintenance activities (i.e. detailed inspection, protection, and repair) and the much longer service life achieved. In short, fewer bridge deck replacements are required over a given period.
The analysis does not take into account other savings resulting from aspects such as:
- less traffic disruption;
- improved public safety; and
- lower environmental impact due to less construction material used over a longer service life.
In addition to bridge decks, this low-shrinkage HPC is suitable for applications in which concrete elements with large surface-to-volume ratios (e.g. slabs and walls) are built in environments where severe loading, movement restraints, or harsh environmental conditions prevail, such as freeze-thaw cycles and/or exposure to chlorides and other chemicals.
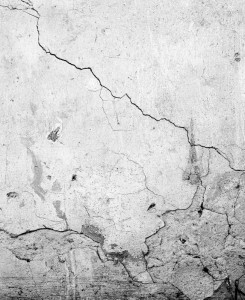
Photo © BigStockPhoto/Zsolt Ercsei
Federal Bridge Corp. Ltd. is planning to conduct further tests using the new concrete at the Cornwall site before beginning construction of the new bridge. In the meantime, NRC-IRC will complete the development of guidelines for the use of the material in bridge decks; these resources will be made available soon on NRC’s website, including the detailed mix formulations and specifications. Their availability will be announced in the NRC-IRC newsletter, Construction Innovation.
Conclusion
Based on the experimental results obtained in both the laboratory and field, and the prediction models calibrated with the test results, one can draw the following general conclusions:
- Internal curing with pre-saturated fine lightweight aggregate combined with a shrinkage-reducing admixture is a cost-effective measure to reduce the risk of shrinkage cracking in concrete bridge decks.
- Low-shrinkage, high-performance concrete can provide excellent mechanical properties and very low permeability to both water
and chlorides. - The construction cost of bridge decks using low-shrinkage HPC may be only slightly higher compared to normal-strength concrete owing to the smaller volume of concrete required despite a typically higher unit cost.
- The service life of bridge decks can be extended by up to a factor of three with low-shrinkage, low-permeability HPC compared to normal concrete.
- The lifecycle cost of bridge decks made with low-shrinkage HPC can be reduced by up to a factor of three compared to normal concrete over a 100-year period.
Daniel Cusson, PhD, P.Eng., is a senior research officer in the Urban Infrastructure Program of the National Research Council’s Institute for Research in Construction (NRC-IRC). He is an expert in experimental research and numerical modelling of the behaviour of high-performance concrete (HPC) structures and their non-destructive condition assessment using advanced structural health monitoring technologies. An adjunct professor with Université de Sherbrooke’s civil engineering department, Cusson is a member of various American Concrete Institute (ACI) and International Union of Laboratories and Experts in Construction Materials, Systems, and Structures (RILEM) committees. He can be contacted via e-mail at daniel.cusson@nrc-cnrc.gc.ca.