Why drainage and ventilation are critical for adhered masonry walls
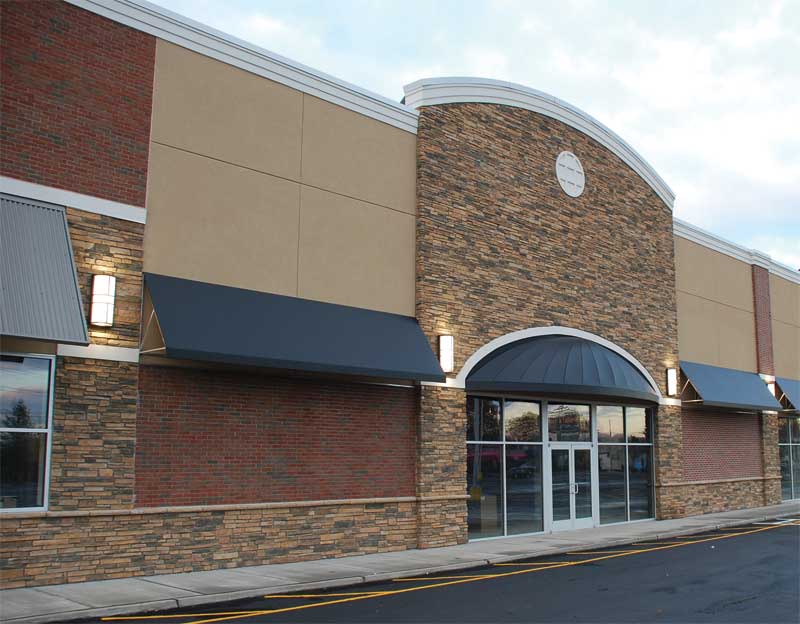
By Art Fox
In masonry cavity walls—a design that has been in use for more than a century—the cavity provides a path for drainage and ventilation and acts as a capillary break. (The author would like to give special thanks to Steven
Fechino [engineering and construction manager for Mortar Net Solutions], Jim Lucas of Lucas and Associates, and Scott Wylie of Wytech Building Envelope Solutions for their invaluable advice and expertise.) However, adhered masonry veneers like stucco have been installed for hundreds of years without drainage or ventilation. So why do we need to add drainage and ventilation planes to adhered masonry walls now? The short answer is American Society of Heating, Refrigerating, and Air-conditioning Engineers (ASHRAE) 90.1, Energy Standard for Buildings Except Low-rise Residential Buildings, and the Canadian equivalent, the National Energy Code for Buildings (NECB) 2011. (For more, read “The Sleeping Giant Awakes: NFPA 285.”)
ASHRAE is an international organization that sets energy-use standards for commercial buildings. Its standards are frequently used as the basis for building codes for jurisdictions in Canada and the United States. Recent changes in building materials, as well as increasingly strict energy codes derived from ASHRAE 90.1, have made drainage and ventilation for adhered masonry walls just as important as they are for masonry cavity walls. This article looks at how modern adhered masonry veneer walls are different from those built before the 1950s, and why these differences are making drainage and ventilation essential for excellent, sustainable performance.
The physics of water
Water molecules are attracted to each other, which results in surface tension—the skin-like film on the water’s surface that makes water drops possible. However, there is a limit to how many molecules can stick together before their weight or air movement overcomes the force of surface tension and pulls them apart. Molecular attraction also causes capillary action, which, combined with the tendency of water to move from wetter to drier, explains why a molecule of water entering a small hole will draw other molecules with it.
Large clumps of water molecules form liquid drops, which quickly run off smooth surfaces like stone and stucco, but will not penetrate an unbroken wall. If water gets behind the veneer, it also will not penetrate small holes in the weather-resistive barrier (WRB), such as those caused by the WRB and lath fasteners, because the attractive force of the water molecules toward each other keeps the drops larger than the holes. The weight of water alone is not enough to force it through.
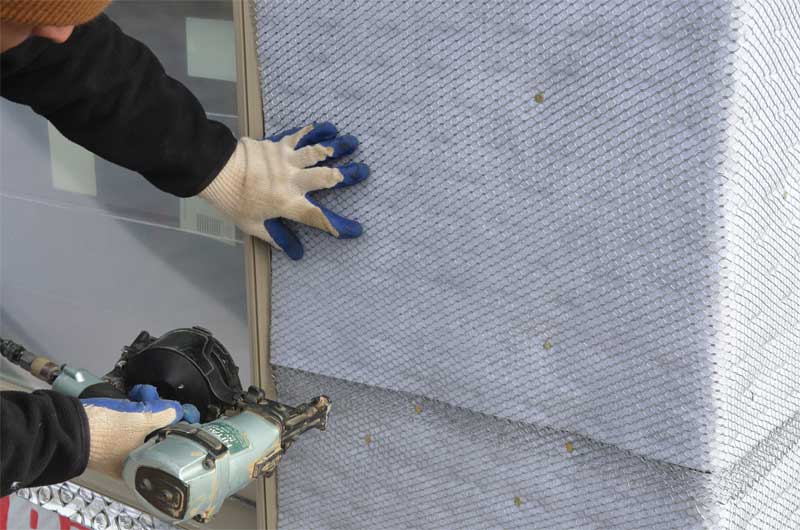
That being said, when pressure differentials caused by wind-humidity differences or heat become strong enough, they can push the water through even very small holes. In building science, this is called hydrostatic pressure. It is similar to pushing a partially filled water balloon through a garden hose—it will not go through the hose by gravity alone, but put enough pressure behind it and it will. Additionally, if there is no bond break between the scratch coat and WRB, high moisture content in masonry will move to lower concentrations in the substrate.
So-called ‘perched’ water can also wreak havoc on adhered masonry walls with trim elements such as lintels. (More information is available in “BSI-057: Hockey Pucks and Hydrostatic Pressure,” by Joseph Lstiburek.) When water becomes trapped behind such walls in the narrow space between the trim and the veneer, it cannot drain due to the clumping effect of water-molecule attraction. The water then soaks into the masonry, substrate, or both. When the sun’s heat causes the humidity in the space between the veneer and WRB to become higher than outside or inside the building, the solar energy drives the moisture both outward through the masonry and inward through the WRB, as well as through any holes in the WRB and sheathing.
How water gets into the wall
Every mason and masonry wall designer knows water gets into masonry walls either as liquid (such as rain or snow) or as vapour (the gaseous form of water). Water vapour does not cause any trouble until it condenses and becomes liquid water. Therefore, providing a drainage mechanism for liquid water is vital, but it is just as important to get vapour out of the wall system before it becomes liquid.
Water penetrates the wall in three different ways. It can:
- enter as liquid or vapour through tiny mortar cracks or through gaps around wall penetrations and at places where different materials meet;
- be drawn as liquid by capillary action through porous masonry; or
- move as vapour from a warm, humid side of the wall to a cooler, drier side of the wall, where it can condense into liquid if dewpoint conditions are met.
In cool weather, water vapour can move from the warmer, more-humid conditioned air inside the building to the exterior, and in warm weather, it can move from the more-humid exterior toward the cooler, drier interior. In either case, the vapour can condense at the back of the veneer.