Why drainage and ventilation are critical for adhered masonry walls
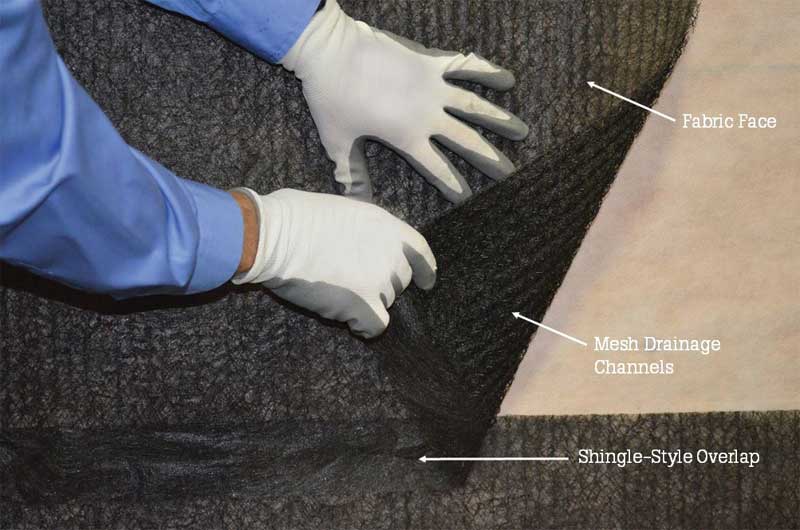
Why old veneer installation methods
do not work with modern walls
Traditional adhered veneer materials include stucco, manufactured and cast stone, and thin stone and brick. Manufactured and cast stone and thin brick were introduced during the 20th century as alternatives to dimensional stone and full-sized brick. Traditional installation methods employ either wire mesh or expanded metal lath firmly attached to the substrate as the support for the veneer. Cementitious mortar fully encapsulating the wire or lath is then applied as an undercoat, or scratch coat, which provides a strong foundation for the veneer. Veneer materials—except stucco—are adhered to the scratch coat by applying a solid layer of mortar to the back of each veneer unit and pressing it tightly against the scratch coat for a few seconds. Stucco is applied continuously as one or two coats over the scratch coat.
When they first became popular, adhered masonry veneer walls did not have the sophisticated flashings, insulation, and WRBs used today, so they leaked a lot of air and would dry quickly if they got wet. With continuous insulation (CI) and WRBs being the best way to meet ASHRAE 90.1 and NECB standards, along with the use of more effective flashings and sealants around wall openings, modern adhered masonry walls leak very little air. This relative airtightness is a key difference between older adhered masonry walls and those of today, and is one reason drainage planes behind the veneer are so important in modern structures. Water that penetrates the wall stays trapped in the wall unless drainage and ventilation are added to get it out.
Weather-resistive barriers
Changes to WRBs make another difference between older and new building construction. WRBs are membranes applied continuously to a building envelope. They are rated in ‘perms,’ or permeability to water vapour. A WRB’s appropriate perm rating, and whether it is placed on the inside or outside of the insulation, is determined by the average heat and humidity of the climate in which the building is constructed. Ideally, a WRB allows enough water vapour to pass through it that the substrate dries without allowing liquid water through. Using two layers of building papers such as Grade D asphalt-impregnated building paper or Number 15 felt as a WRB is common when CI is not included.
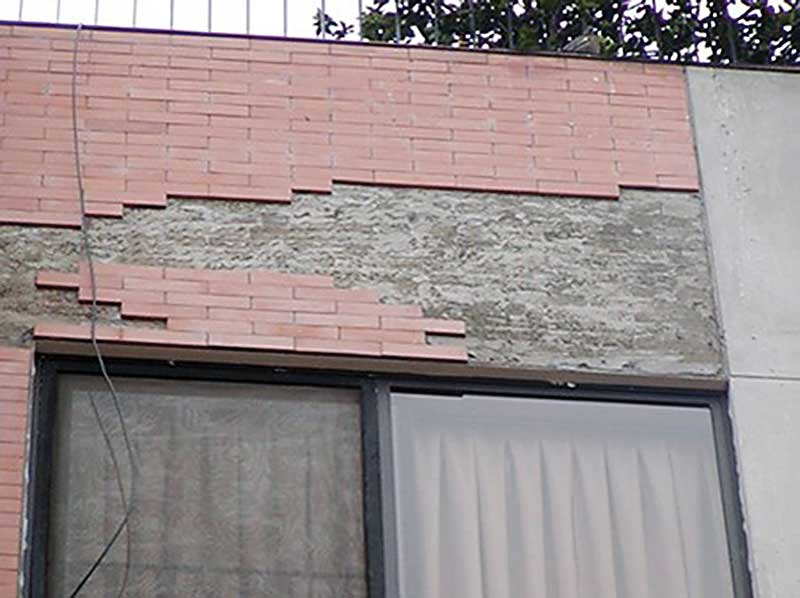
The thinking behind using two layers of building papers is the assumption the outer layer will get wet when the scratch coat is applied. When the papers dry, they wrinkle, eliminating any mortar bonding by pulling away from the scratch coat and creating a sufficiently rough surface that water drains between the papers and the scratch coat. However, since the wrinkles are shaped randomly, they do not create continuous drainage channels running the height of the wall. This means they can obstruct water flow and create pockets where water can collect. Any buildup of water can lead to its lateral migration at the laps and allow a wider area of the substrate and scratch coat to get wet.
The absence of a mortar bond allows some drainage, but very little—if any—ventilation. Since older buildings with paper or felt as a WRB leaked a lot of air, they did not need to provide ventilation. Using plastic house wraps instead of building papers is now common, and some brands can bond strongly to mortar, which minimizes potential drainage. (For more information, see Lstiburek’s “BSI-029: Stucco Woes–The Perfect Storm.”) Since today’s buildings do not leak much air, and modern papers and plastic house wraps allow minimal ventilation, there is very little drying behind the scratch coat with paper, felt, or house wraps.
Additionally, without a drainage and ventilation plane, building papers can absorb enough water to degrade and develop holes, which allows water to get to the substrate. They can also become saturated with water, creating an intensive vapour source inside the wall. If water stays in contact with the substrate, even if there is a WRB over it, it can migrate through fastener holes and other penetrations and be absorbed by interior materials. If even small amounts of moisture stay in contact with the substrate long enough, it can cause fastener corrosion, nail pullout, mould, and sheathing degradation.
Since CI is now commonly used in order to meet energy standards, manufacturers have developed rigid insulation with sealed seams, which serves as both CI and a WRB. These systems can be more efficient to install and more resistant to damage during installation than the WRBs mentioned above, but they still need drainage and ventilation. Also, when wire or lath is attached on top of CI, the fastening system must be designed to handle the eccentric loading placed on the fasteners, because if they bend or pull out, cracks in the veneer will develop very quickly. (The Foam Sheathing Coalition offers a “Guide to Attaching Exterior Wall Coverings Through Foam Sheathing to Wood or Steel Framing” with tables for determining the right fastener sizes based on stud type, insulation thickness, and veneer weight.)
Since modern buildings do not self-ventilate by leaking air, and since all masonry building exterior walls leak moisture, using traditional installation methods with modern materials but without a drainage plane means most of the water penetrating the veneer must migrate into the substrate or out through the face of the veneer.