What lurks beneath?
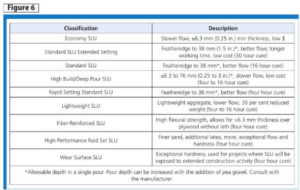
SLU selection
Setting material manufactures provide several self-levelling underlayment formulations optimized for specific floor levelling situations. Whether by specification or a contractor’s choice, a project’s site conditions and flooring requirements can be better addressed with the right product, potentially saving time and labour, as well as achieving a more suitable substrate for tile installation. Figure 6 (page 32) illustrates the range of products available to manage the project’s budget, construction schedule, degree of flattening (or levelling), and product working time.
Cementitious self-levelling underlayments should only be applied to clean and structurally sound concrete substrates. It is recommended to remove bond-breakers, such as grease and oils or curing compounds and damaged and loose concrete. Surface should be roughened or profiled to promote a better mechanical bond of the primer and SLU to the concrete.Surface preparation
SLUs can also be applied over gypsum-based underlayments, oriented strand board (OSB) underlayments, cutback adhesive residues, epoxy and cement terrazzo, metal, ceramic and stone tile, and well-adhered resilient flooring. Careful evaluation of these conditions must be made before installing a self-levelling product. Manufacturers will have specific preparation requirements for these conditions and could, in some instances, require a complete tear out before attempting to install a SLU.
Additional items to evaluate
Moisture vapour
A moisture vapour emission rate (MVER) in excess of 1.4 to 2.5 kg/93 m2 (3 to 5 lb/1000 sf)/24 hours or 75 to 80 per cent relative humidity (RH) could exceed the flooring manufacturer’s guidelines or restrictions for their product. Ceramic and stone tiles as well as cement-based SLUs are more compatible with excess moisture vapour. However, the effects of the vapour, such as production of alkaline deposits on the substrate, efflorescence formation on the flooring surface, staining, mould growth, and warping, may plague the finished floor, particularly luxury vinyl tile (LVT), carpet, and wood. MVER or RH readings that are not compatible with the flooring product must be remediated with 100 per cent solids, two-part epoxy, moisture mitigation membrane.
Construction joints and cracks
Movement joints and cracks that may have developed after the concrete’s installation require specific methods when installing underlayments and ceramic tile and stone. The TTMAC Tile Specification Guide provides several useful details such as:
301MJ, Movement Joint Guidelines for Ceramic, Glass, and Stone – Expansion joints in the concrete must be brought up through the tile assembly, in the same plane;
311F Detail A (on-ground concrete) and 311F Detail A(above-ground concrete) – Both flooring details include a cementitious self-levelling underlayment, and are recommended for concrete slab construction where no bending stresses occur, and FF is critical, but the latter requires a bonding mortar that is approved by the manufacturer for above-ground use; and
311F Detail C – Full – Allows for the relocation of a static joint or crack through the tile assembly by incorporating a partial crack isolation membrane in the assembly.
Additionally, full slab depth joints and cracks require filling to prevent the self-levelling underlayment from flowing through the slab into the room below or soil subgrade. If SLU seeps through the concrete slab after the products’ heal time, ≥ 10 minutes in accordance with ANSI A118.16, a permanent depression can form in the SLU’s surface directly over the crack. This depression can reflect through resilient flooring.
Substrate priming
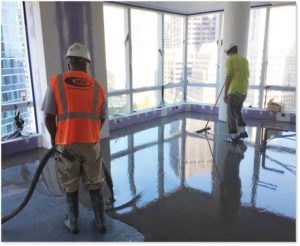
Concrete is a porous material. If not correctly primed to not absorb SLU’s mix water, the SLU’s workability, flow and heal rates, adhesion, strength, and surface flatness are compromised. A properly applied primer penetrates the surface, forming a uniform film, free of voids and pinholes. Non-porous substrates, such as hard-trowelled concrete may also be a problem and could require mechanical preparation before a primer is applied.
ASTM F3191, Standard Practice for Field Determination of Substrate Water Absorption, is a simple test for assessing the substrate’s porosity. Drops of water should be applied onto the concrete, particularly on suspected problem areas. If the water is readily absorbed, creating a darkened spot, the concrete is porous. If the water drops bead up on the surface, and no dark damp spot is visible, the concrete is non-absorbent. Extremes in porosity are equally problematic and require special attention. The primer will need multiple applications on porous concrete, whereas repellent surfaces may require mechanical preparation or a special primer. Also, primer applications over gypsum-based or OSB underlayments, cutback adhesive residues, epoxy and cement terrazzo, metal, ceramic and stone tile, and well-adhered resilient flooring may require special consideration before priming.
Going with the flow
Self-levelling cement underlayments can be mixed and applied using automated mixing and pumping equipment or manually mixed onsite with drill-powered ‘eggbeater’ paddle and poured from the mixing barrels. Both methods are suitable for commercial and residential installations.
A wet edge must be maintained between successive pours of SLU. Fresh material poured adjacent to product that has already started to harden can form a ridge or bump along the unintended cold joint, which could create a visible ridge in resilient flooring. The window of time for mixing to final finishing is approximately 20 minutes for standard set SLUs. Temperature, humidity, and air movement must be factored into the installation so the SLU’s working time and flow and heal rates are not compromised. Cold temperatures are also a potential problem. The ideal ambient, substrate, and product temperature is 10 to 32 C (50 to 90 F). Manufactures provide rapid and delayed setting formulations when installing at temperature extremes. Strategic material and equipment staging, and adequate labour must be managed for a successful installation.
As material placement proceeds, another contractor will be pushing and pulling the flowable product to the required thickness with a gauge rake. The gauge rake has adjustable feet so that the blade is set and maintained at the correct elevation above the substrate. Gauge raking is followed by lightly pulling a smoother across the SLU (Figure 7).