Weatherproofing ICF Walls: Lessons in resiliency from B.C. field testing
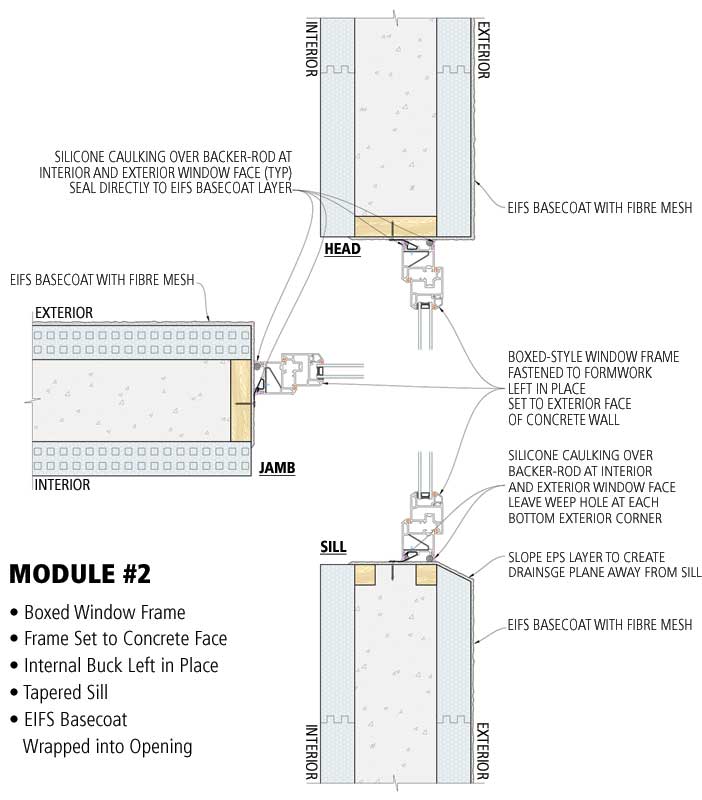
Testing ICF walls for water intrusion
In 2013, a number of North American ICF manufacturers teamed up to provide code-compliant, tested construction details for window and door penetrations in ICF walls. HPO agreed to partner in this targeted research project, recognizing the value of the research to support its goals of energy reduction and resiliency in B.C. housing stock.
Phases 1 and 2 of the testing began in 2014. Several 2 x 2-m (6 x 6-ft) wall samples were constructed using 152-mm (6-in.) core ICFs, and each employed a different buckout method common at the time. These included various wooden bucks—some spanning the full width of the ICF wall, others recessed into the ICF cavity—as well as vinyl block-outs designed specifically for the ICF industry. The assemblies were laboratory-tested at the Vancouver headquarters of a B.C. window manufacturer, using its air/water intrusion testing equipment. Simulated wind-driven rain was pitted against a typical fixed-pane vinyl window sample in compliance with ASTM E331, Standard Test Method for Water Penetration of Exterior Windows, Skylights, Doors, and Curtain Walls by Uniform Static Air Pressure Difference, in conditions representing a range of building types.
The results were more instructional than encouraging. Most examples allowed water and air penetration past the assembly at relatively low levels of pressure and water flow. Some held to mid-range pressures, but all failed at
the high-pressure criteria levels. With those results, the ICF technical representatives and building science experts at RDH Building Science set about designing six additional test samples implementing modified features or untested techniques for a second round of tests. These all yielded much-improved results, with one displaying quite unexpected and extraordinary performance.
The 2011 North American Fenestration Standard (NAFS) has 18 levels of pressure criteria, increased from three under the original CAN/CSA A440, Specification for Windows, Doors, and Skylights. The levels tested here fall within the pressures given in NAFS, but conform generally to the older standard.
Tested levels were:
- 150 Pa (3.13 psf);
- 300 Pa (6.26 psf); and
- 700 Pa (15 psf).
These levels generally correlate to low-rise, mid-rise, and high-rise building types. Lab testing was successful up to 5000 Pa (104 psf), in one module’s case—seven times the average pressure criteria for high-rise building enclosures under NAFS. Even more surprising was the fact the most successful ICF buckout method was also one of the simplest and least expensive to install.
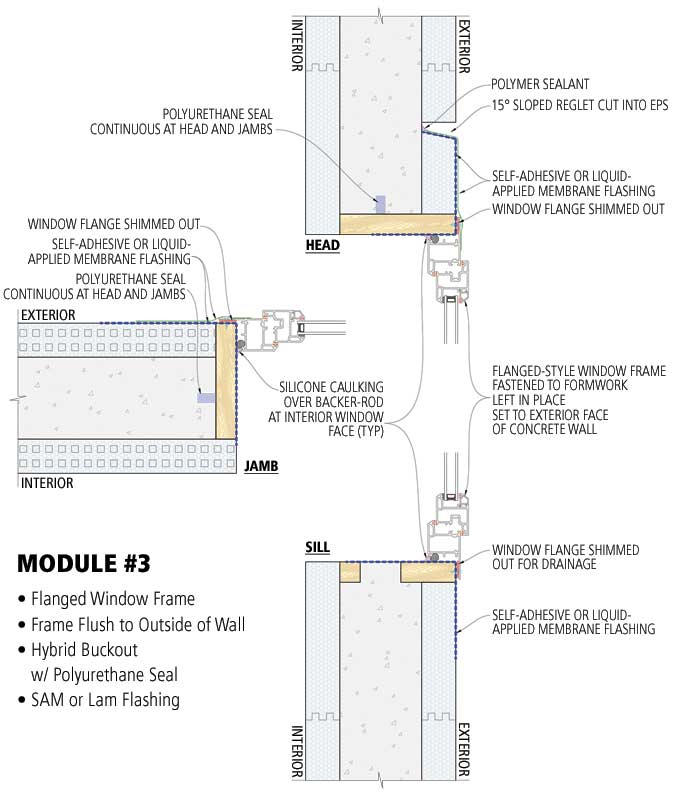
Field testing
Data extracted from laboratory testing was used to ‘shortlist’ four additional test assemblies for a more realistic and accurate field test under ASTM E1105, Standard Test Method for Field Determination of Water Penetration of Installed Exterior Windows, Skylights, Doors, and Curtain Walls, by Uniform or Cyclic Static Air Pressure Difference. While the most successful results came from ICF wall samples featuring non-flanged (i.e. boxed or equal-leg) window frames, the ICF industry made it clear a flanged window option, mounted to the exterior face of the wall, was a necessity. Widespread use of this option made it critical to provide it, rather than attempting to force a change.
A technical subcommittee was formed to design a cost-effective buckout option able to both accommodate a flanged window installation and demonstrate adequate moisture and air resistance. Brian Hubbs, the lead engineer for the project at RDH, provided input.
Hubbs suggested a reglet be cut in the EPS just above the flanged window opening, allowing the head-flashing from the window to be sealed directly to the concrete core. Thus, the core’s watertight plane could be preserved and extended to the exterior of the flush-mounted window, and the opportunity for water to pass around the extended window buckout minimized. This method proved to be successful at the first two pressure levels tested, with minor leaks detected at the highest levels. Even though it was not fully successful in testing, this method’s effective performance at tested levels exceeds requirements for nearly all residential building types in all regions.
Phase 3 involved field-testing. A site in Surrey, B.C., was selected and the four assemblies were constructed onsite according to designs developed, critiqued, and accepted by technical professionals from the ICF industry, along with building envelope engineers who oversaw the entire project. Again, ASTM E1105 was implemented at varying wind-pressure and water-flow levels meant to reflect conditions expected on a range of building types.