Waterproofing through the ages: From ancient Pyramids to modern day techniques
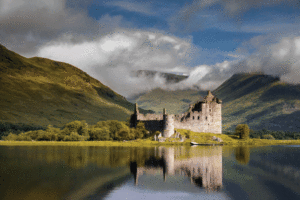
By Rockford Boyer, B. Arch. Sc., MBSc, BSS
Water is the source shaping the environment, connecting all living things, and is critical for all forms of life. However, despite its fundamental importance, water poses a significant threat to the long-term strength and durability of buildings. Its infiltration, whether in the form of bulk water or vapour, can have detrimental effects.
Traditionally, drying mechanisms were essential to address moisture within the enclosure system. When controlling moisture below ground, the only solution is to completely prevent its entry into the foundation system. Moisture ingress can cause various damaging functions that degrade the foundation system, including corrosion of reinforcement, freeze-thaw damage, and chemical attack. To ensure the longevity, operation, occupant comfort, maintenance, and sustainability of a building, it is necessary to use high-quality and high-performing waterproofing materials. This article explores the history of waterproofing materials and strategies over time. It also explores a highly advanced and one of the most durable waterproofing materials on the market today—polyurea.
A brief history
The origins of waterproofing and moisture management can be traced back more than 13,000 years ago. In the ancient world, the demand for skilled waterproofing was remarkably high, given its crucial role in various domains such as agriculture, construction, and transportation. This led to the emergence of the “waterproofing trade” as one of the most essential and sought-after professions, ranking behind masonry and carpentry.
Understanding the origins and history of waterproofing provides designers, architects, builders, and owners with real historical information and data on how previous groups developed and applied waterproofing solutions for their specific geological region and period. Historical records, buildings, and relics can provide valuable performance data, including nonperformance data, which can potentially increase the success rate of future waterproofing applications and materials. Previous examples of waterproofing performance, education and material used will ultimately elevate the designer’s knowledge about which solutions have the best potential for success. Manufacturers deal with scenarios like this every day when a new product is brought to market, designers often ask “how does this compare to competitive product which has been on the market for 10 years?” Those in the Paleolithic Period did not have the opportunity as today’s industry professionals do to have 1000s of years of waterproofing experience.
During the Paleolithic Age, mankind was transitioning into a “permanent resident” phase, rather than a nomadic hunter gatherer, and a moisture protection solution was needed for their agriculture surplus. Straw and clay were used as the typical solutions for grain surpluses; however, ceramics and bitumen vessels were developed to assist in the transportation of water and liquids. Bitumen emulsion on the underside of boats allowed for fishing, transportation, and longer land and sea explorations. These developments and advancements in waterproofing technology assisted in the progressions of the early day man and their transition to becoming a permanent resident.
In ancient Egypt, bitumen emulsion and dry reed fibres were used to waterproof the deep foundations of the great temples and pyramids. Archeological excavations have proven the effectiveness of ancient waterproofing, as the interior spaces of the pyramids remained dry, even during the annual floodings of the Nile River. During the Roman era, waterproofing techniques relied on sturdy masonry and concrete foundations and structures. Roman engineers incorporated volcanic ash, seawater, and lime in their concrete mix, to create a “pozzolanic” reaction that enhanced the concrete’s durability and resistance to water.