Waterproofing through the ages: From ancient Pyramids to modern day techniques
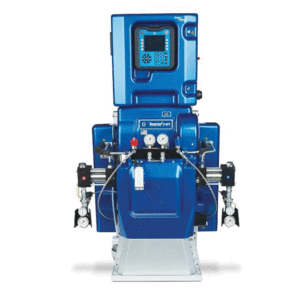
Many polyurea’s in Canada have been tested to traditional “asphaltic” standards; however, it does not typically represent the true characteristics of the polyurea. To ensure the polyurea sold in Canada meets and exceeds the traditional waterproofing standards, testing protocols have been set up to ensure it outperforms its intended roll. It has been demonstrated polyurea can be unsupported when testing the resistance to hydrostatic pressure at various depths (other sheet goods, asphalt should be tested supported). Out of scope testing by leading building science/engineering firms have determined protection boards can be eliminated in front of the polyurea membranes due to their superior structural characteristics. Military branches around the world have also used polyurea for blast mitigation based on the products resistance to movement, abrasion, and impact.
Polyurea was developed more than 30 years ago by chemical engineers who formulated these resins to possess low VOCs, superior fire performance, a wide range of modulus options, and exceptional versatility and strength, surpassing the current leading waterproofing materials.
These waterproofing materials are applied by trained installers that utilize computerized plural component equipment to achieve a more uniform and effective system application. The computerized plural equipment (Figure 1) combines the isocyanates (A side) and resin blends (B side) at the tip of the nozzle to create an inert and durable urea-linkage waterproofing membrane. The initial curing of the waterproofing material happens within 20 seconds and the full cure occurs within the following few hours, resulting in a high tensile, high abrasion-resistant, and totally monolithic waterproofing membrane.
The application of polyurea
Due to its ease of application, polyurea offers numerous possibilities on the jobsite. However, the most common applications of polyurea are for waterproofing and protecting vertical and horizontal concrete surfaces below-grade.
Blindside and positive side waterproofing using spray-applied polyurea has witnessed a surge in demand due to factors such as cost-effectiveness, speed, application quality, and effective resistance to damage during construction. However, the primary contributing factor is the application of polyurea to fresh concrete. The chemistry of the polyurea waterproofing allows application onto a damp substrate, whereas a polyurea/polyurethane blend could not.
Like any other waterproofing material, proper substrate preparation is imperative to the success of polyurea. As the saying goes, “the application is only as good as its substrate.” The surface of the substrate must be sound, clean, and free of oil, grease, wax, dirt, sealing compounds, or any contaminant which may act as a bond breaker.
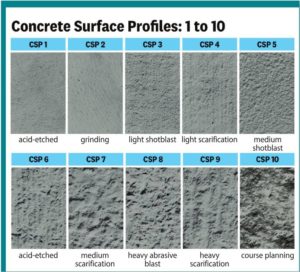
A concrete surface profile (CSP) reference guide on the quality and condition of the concrete substrates was created to assist building professionals, contractors, and applicators determine if the substrates require remediation prior to the application of the waterproofing (Figure 2). The CSP reference guide identifies a concrete condition ranging from CSP1 (smooth) to CSP10 (pitted), and should be reviewed prior to any application of a waterproofing membrane.
Application of a polyurea waterproofing membrane should be applied to concrete surfaces with a CSP between one to four, or the potential for blisters can occur (due to expanding gas). Primers should always be used on a concrete substrate to minimize the potential for waterproofing delamination and blistering. If it is not a CSP 1-4 concrete, it must be remediated to bring the concrete surface profile up to a CSP 1-4 prior to the application of a polyurea.