Waterproofing shotcrete at VanDusen Botanical Gardens
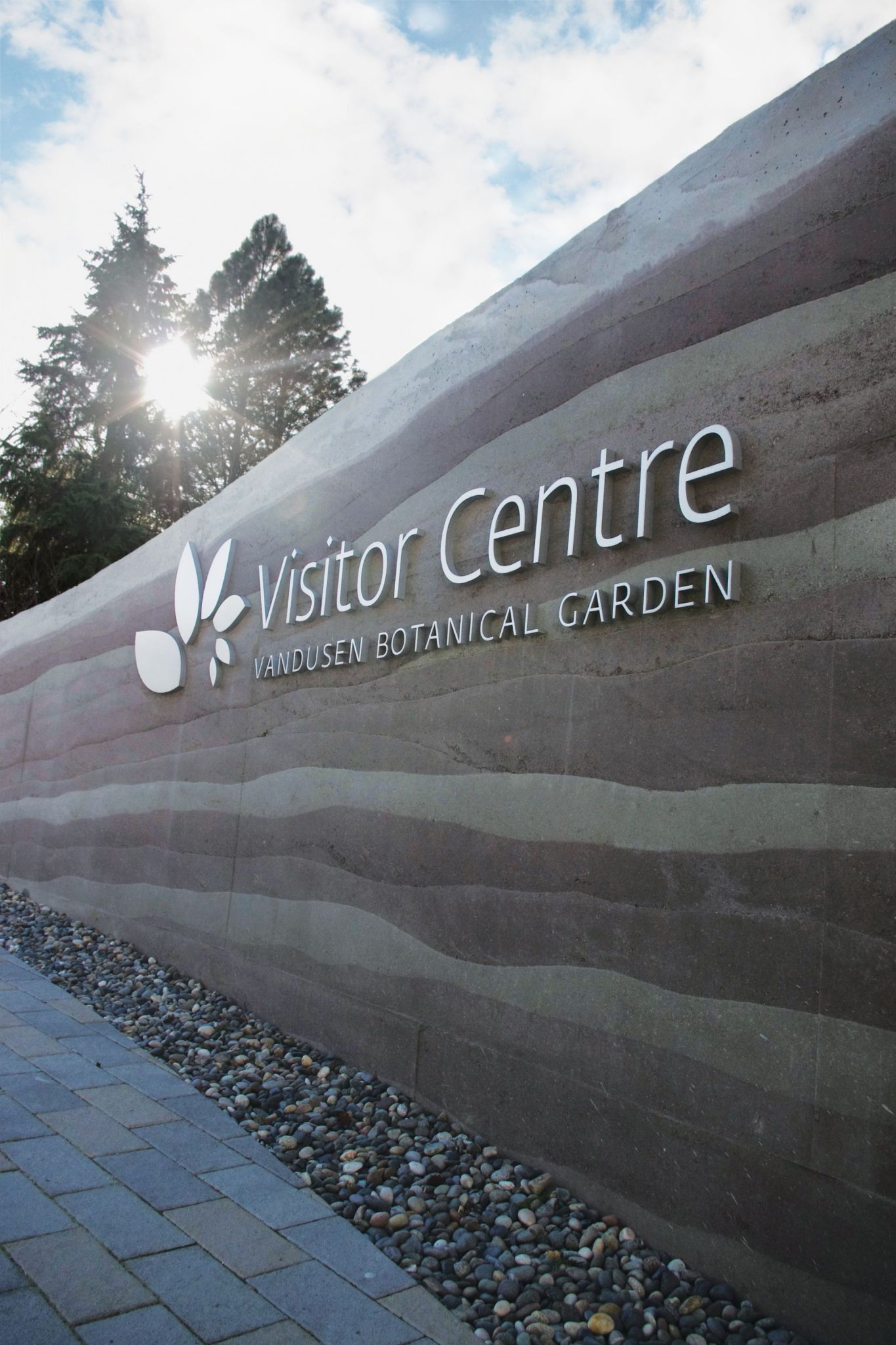
By Jeff Bowman, BSc
Unlike the traditional method of pouring concrete into a moulded form, shotcrete involves spraying concrete from a high-pressure hose, allowing the structure to be builtup in layers. This method is being specified for foundations, building tanks, and parking garages because it saves time and money, requiring half the forming and equipment of regular cast-in-place methods, while also allowing for considerable design flexibility.
Vancouver’s VanDusen Botanical Gardens was redesigned in 2011, making a strong impact regarding environmentally conscious building practices. The centre not only maintains a scenic 22-ha (55-acre) botanical garden, but also has a strong focus on botanical and horticultural education. For the new visitor centre, designers wanted to showcase the commitment to reducing the facility’s carbon footprint by creating a ‘living’ building designed to Leadership in Energy and Environmental Design (LEED) Platinum certification standards.
Further, the VanDusen Botanical Gardens design team wanted the project to fit the parameters of the Living Building Challenge—a certification program defining the most advanced measure of sustainability within the building industry.
Design plans
The building’s design is in the shape of an orchid, with organic lines blending in with the landscape. The original plans called for rammed earth for the building’s structural and architectural walls. However, it was determined rammed earth alone would provide neither adequate load-bearing strength, nor enough heat retention to meet the project’s LEED objectives.
Instead, a reinforced concrete wall had to be used, with the rammed-earth wall being only the decorative, visible piece at the entrance. After researching different concrete placement options, the project team decided structural shotcrete would be the best overall solution for the unique design.
The VanDusen project team enlisted Torrent Shotcrete Structures to create a wall to reinforce the decorative rammed earth, which curved and oscillated in accordance to the unique organic, orchid design. As the building needed to align with strict LEED Platinum requirements, the waterproofing system had to conform to strict environmental specifications, as well as work as a long-term solution. Also, the project interior and exterior were intended to be finished concrete. However, the green building specifications placed restrictions on volatile organic compounds (VOCs) in sealers or finishes, typically following the emissions limits published by the U.S.South Coast Air Quality Management District (SCAQMD).
Waterproofing shotcrete can be challenging to those familiar with the process of cast-in-place concrete, even without strict green building requirements. Shotcrete has the potential to be more permeable and have larger, more frequent voids when an inexperienced contractor is used.
These voids are generally created when rebar is displaced during the period the shotcrete is still plastic. Additionally, any shotcrete placed by a less experienced nozzleman can contain insufficient consolidation or cold joints within the structure. Proper consolidation must be achieved to prevent imperfections such as cracks, voids, and joints that could later cause waterproofing problems. An experienced contractor is able to place shotcrete with enough impact velocity to allow it to be consolidated, while also flowing around and encapsulating the reinforcement. This has the effect of producing a high-density, less-permeable structure. The results are similar to vibrating cast-in-place concrete, but there is less risk of segregation.
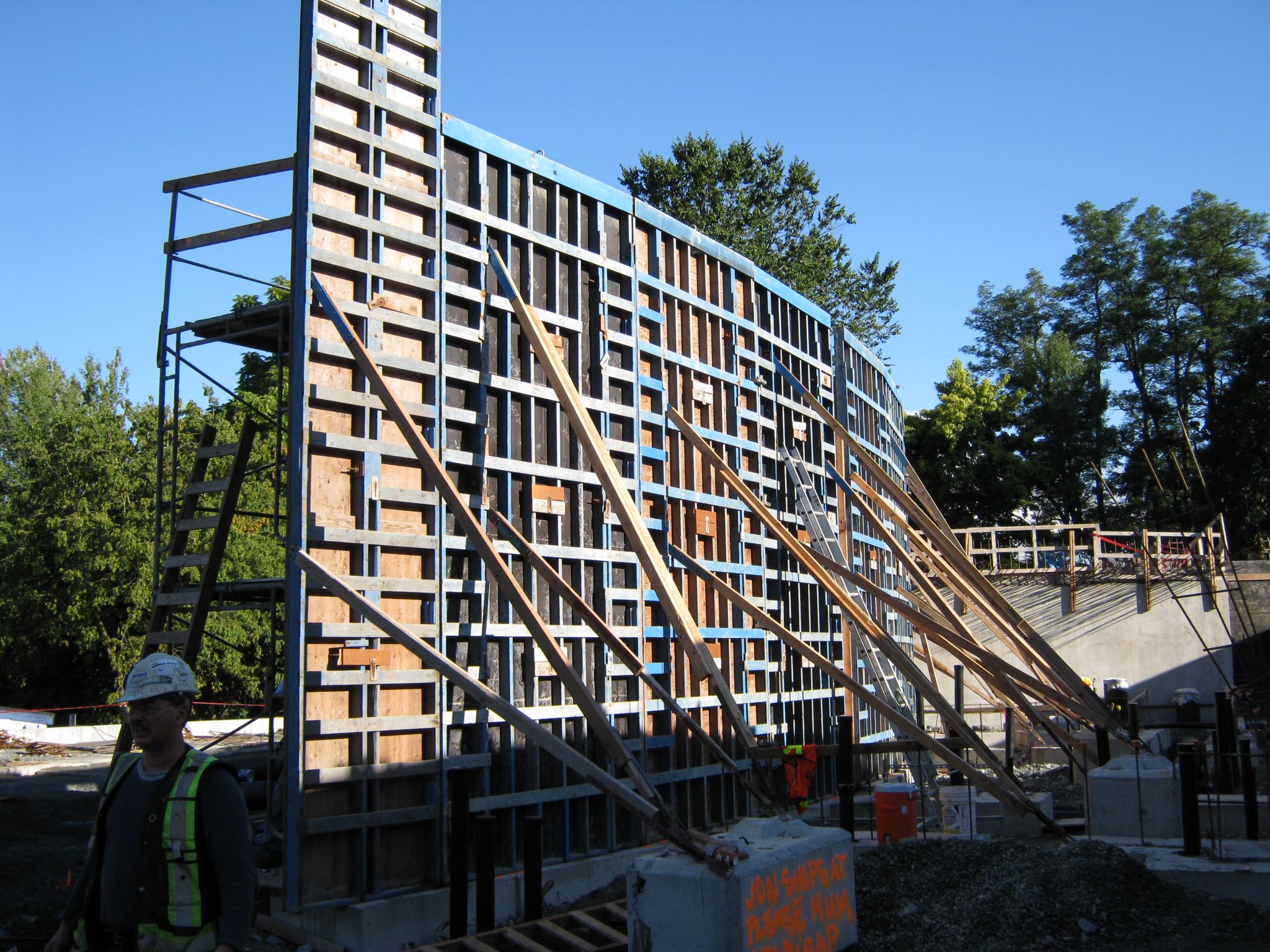
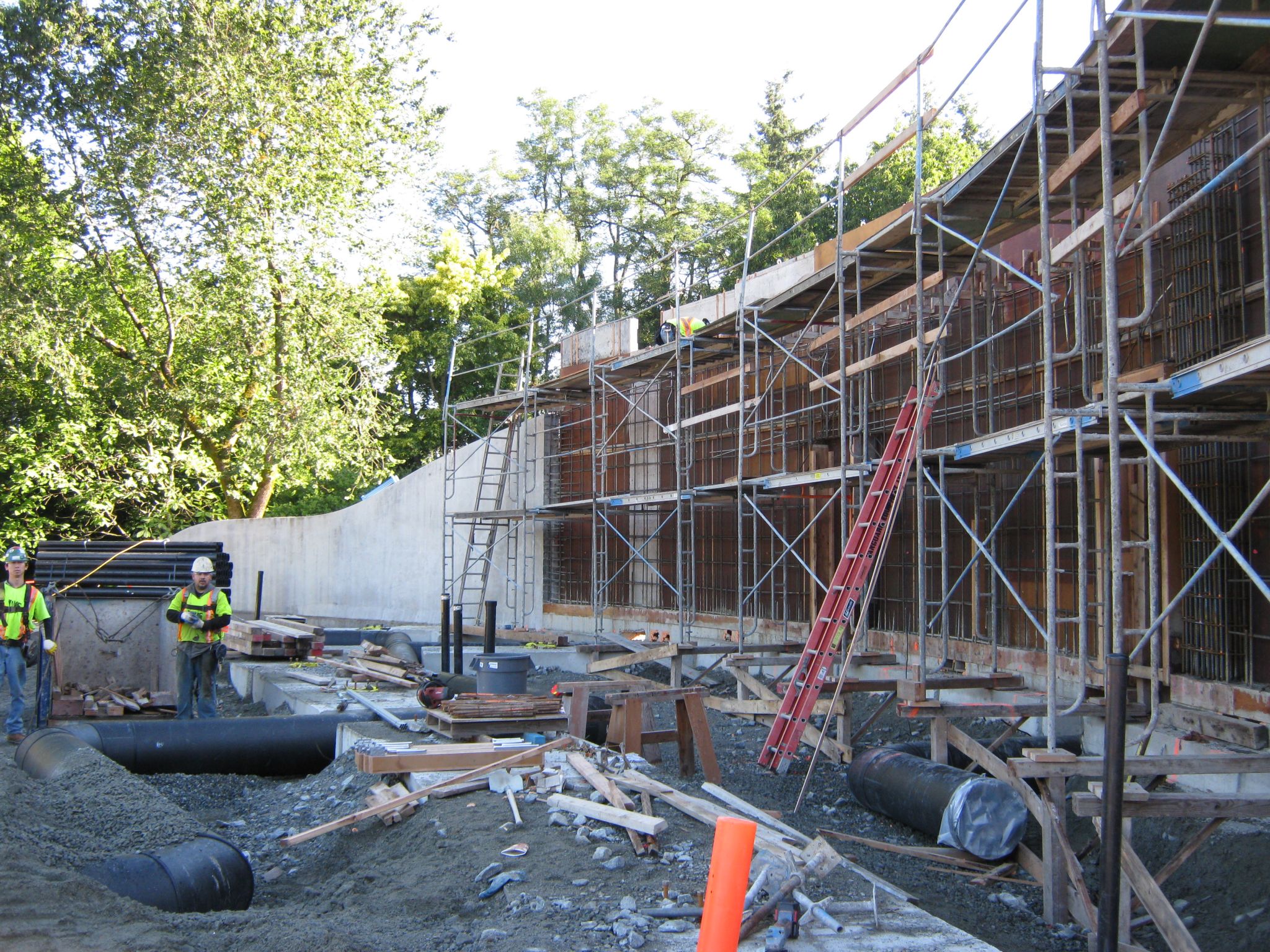
Surface-applied waterproofing systems
Surface systems include coatings and sheet membranes and can be either polymer- or bitumen-based. They can be applied with a brush, spray, roller, trowel, or squeegee, and usually contain urethane or polymeric asphalt (hot- or cold-applied) in a solvent base.
Successful waterproofing with these coatings depends on proper thickness and uniform application. They call for skilled, experienced labour to apply them, as well as a clean and dry substrate—which can be difficult to achieve in a construction environment. The coatings are vulnerable to damage, and require a protective layer before backfilling. Properly cured concrete is also required to avoid problems with adhesion and blistering.
Although surface coatings work well on projects with multiple plane transitions, intricate geometric shapes, and protrusions, the polymer (i.e. liquid) coatings can deteriorate when exposed to ultraviolet (UV) radiation and cannot withstand foot traffic. The liquids themselves also contain toxic and hazardous VOCs. Disadvantages common to all surface coatings include limited crack resistance, time-consuming surface preparation requirements, and the amount of access space required to install them.
Sheet membranes
Sheet membranes are flexible sheets adhered to the wall and sealed at the seams. This method has crack-bridging ability, but similar limitations to coatings.
Installation can be challenging, as membranes require sealing, lapping, and finishing of seams at the corners, edges, and between sheets. Additionally, sheet membranes must be applied to a smooth finish without voids, honeycombs, or protrusions. Also, because the membrane can puncture and tear during backfilling, protection boards need to be installed.
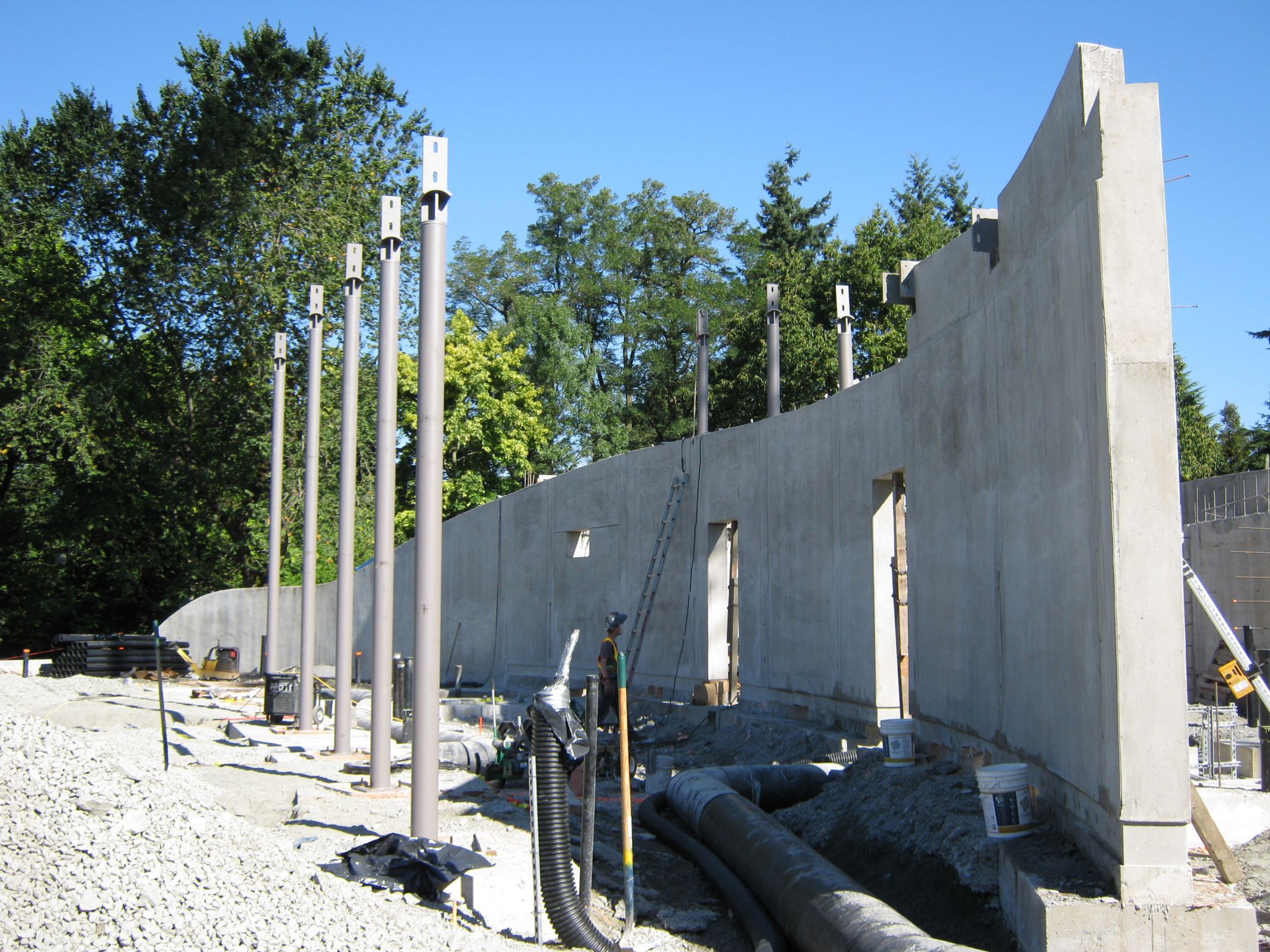
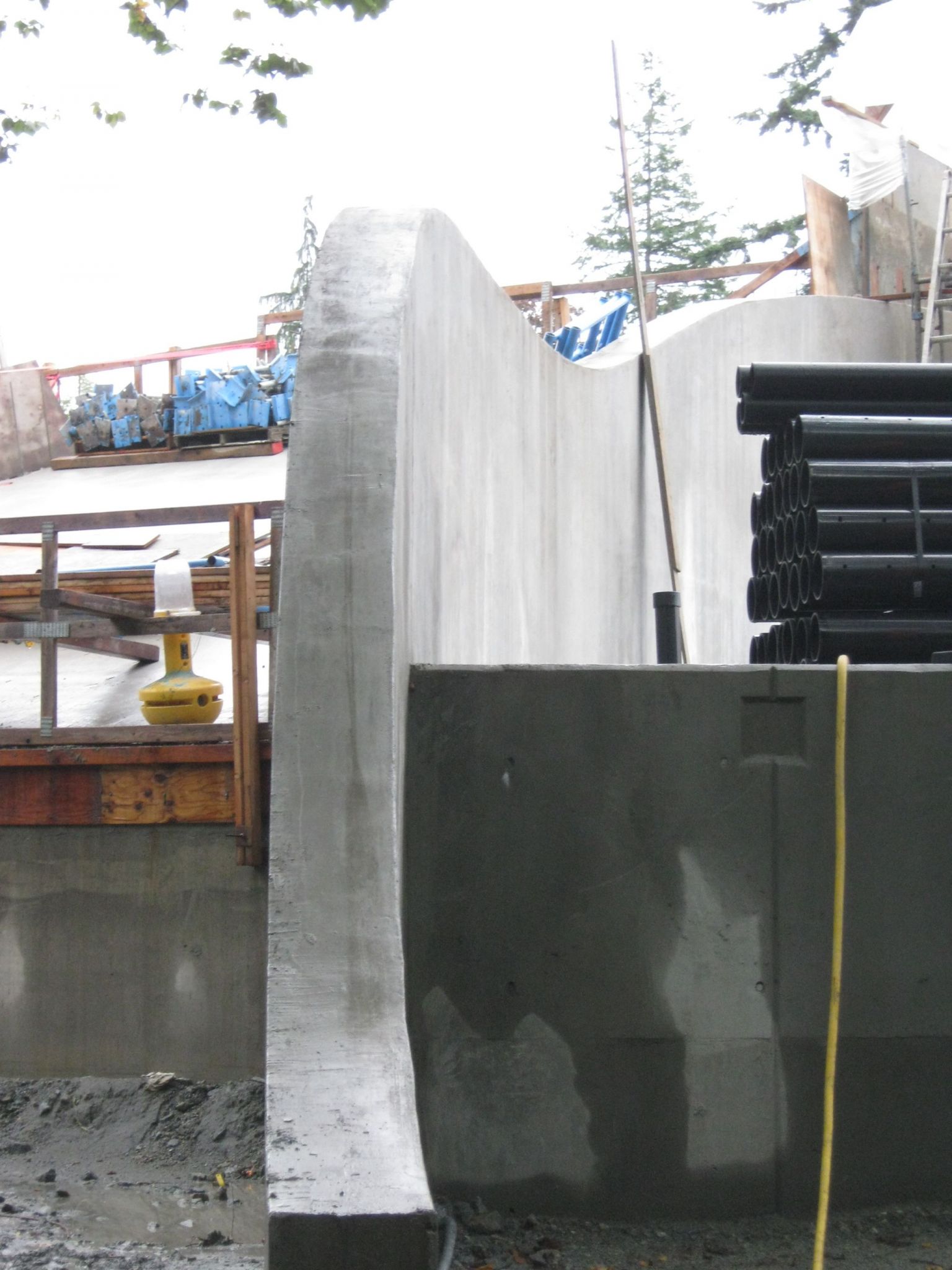
Integral systems
Neither method of surface-applied waterproofing was deemed appropriate for the VanDusen centre’s unique design. Surface preparation and installation of a coating or membrane would have taken up valuable time. More importantly, the surface barrier would likely have been damaged during the installation of the rammed-earth portion of the wall, which would have rendered the waterproofing useless. The use of VOCs in liquid-applied membranes, as well as the primers and joint adhesives for sheet membranes, also made these systems incompatible with the project’s environmental requirements.
Many structural shotcrete projects have turned to integral waterproofing systems, which include densifiers, water repellants, and crystalline/reactive systems. Integral systems are admixtures added at the batching plant and delivered pre-mixed into the concrete. Instead of forming a barrier on the concrete’s surface, they turn the full depth of the concrete itself into a water barrier. They do not require additional surface preparation or labour to install and, once installed, cannot be damaged by scratches and punctures.
Integral systems do have some special requirements. For example, they demand a high level of consolidation to be fully effective, and also require a waterstop to be installed at the joints.
Densifiers
Densifiers can include pozzolans such as silica fume, fly ash, and slag, which react with calcium hydroxide resulting from the hydration of regular portland cement to provide a stronger, denser concrete. Water-reducing admixtures (WRAs) can be considered to serve a similar purpose, as using less water results in concrete with reduced porosity and therefore lower permeability.
However, this approach has limitations. Although they produce high-density concrete, none of these additives do anything to address the true weak points in concrete—the cracks and joints. As a result, they do not provide a complete waterproofing solution.
Water repellants
Water repellantsare typically stearates, fatty acids, oils, and silicones. These materials function through the use of water tension, and reduce water absorption by promoting a beading effect. However, this repellent effect cannot stand up to water under pressure, so these materials are generally considered to be ‘dampproofers’ rather than full waterproofers. They are also unable to prevent water from entering through cracks and joints.
Reactive/crystalline systems
These systems are added to fresh concrete to reduce the material’s permeability and provide permanent waterproof protection. When added to the concrete mix, crystalline system’s chemicals grow millions of needle-like crystals throughout the concrete matrix, blocking the movement of water in all directions. These crystals then remain dormant until cracks form, at which time they react with any incoming water to ‘self-seal’ the crack and maintain a watertight barrier.
A crystalline system does not require additional labour, time, or access during installation. Once installed, it cannot be cut, punctured, or damaged. However, the disadvantage is cracks and joints may take time to self-seal.
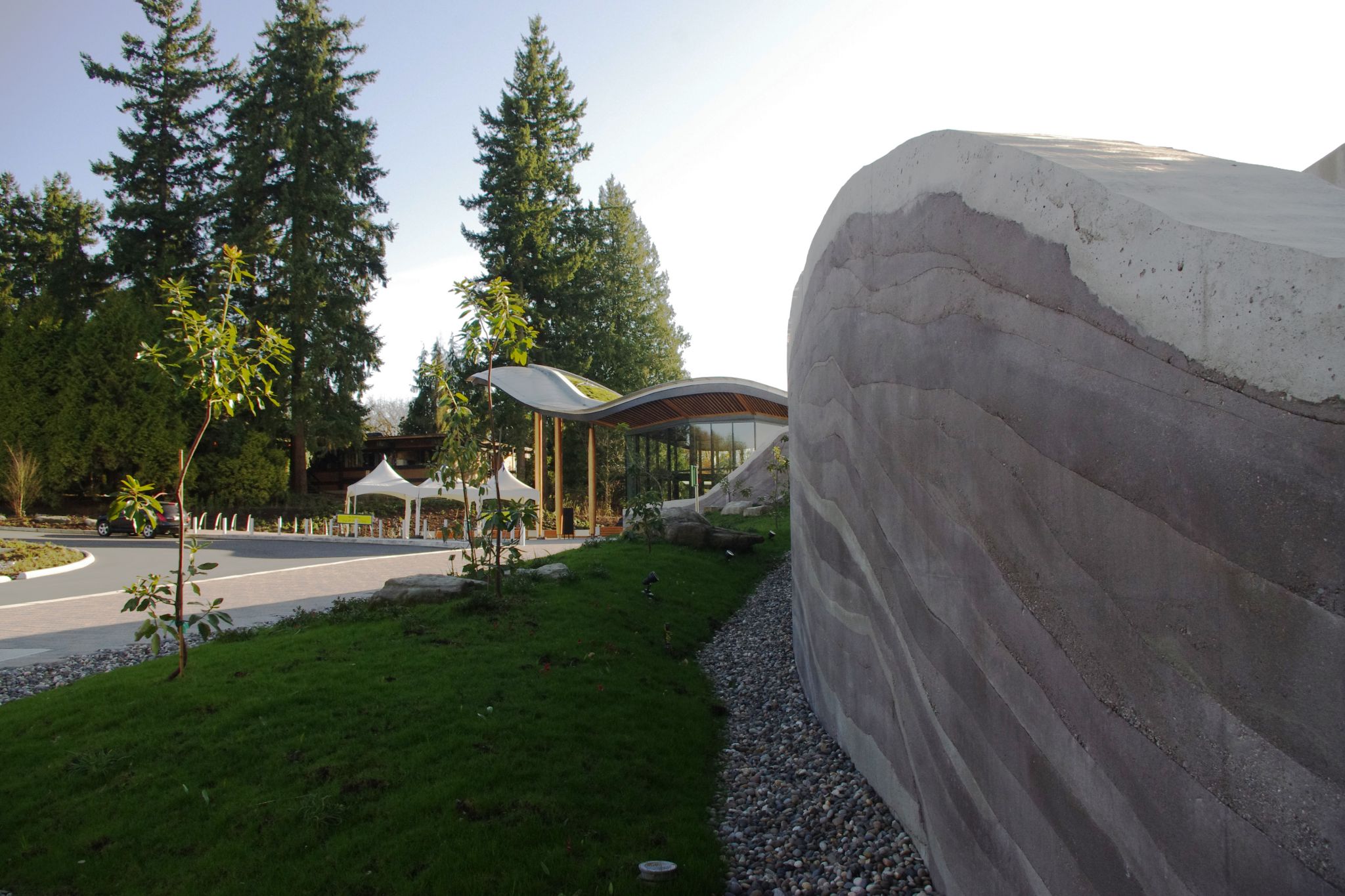
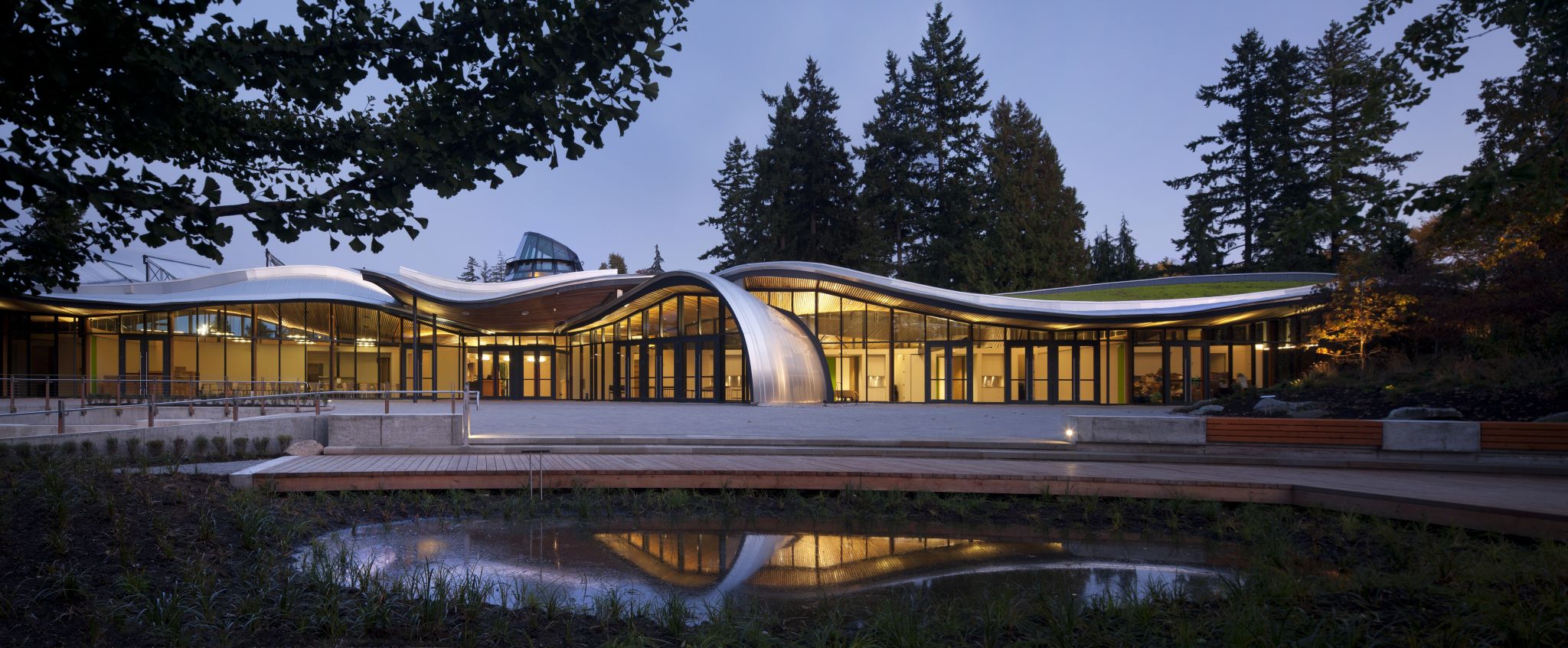
Waterproofing solution
After being presented with various waterproofing options, a crystalline system was specified for the VanDusen project. Crystalline waterproofing is best suited to shotcrete because as an integral system it is not prone to damage or poor workmanship. The specified system can withstand extreme hydrostatic pressure and has a compatible crystalline waterstop that can withstand the rigorous shotcrete process. Additionally, it has an integrated repair system, and provides low cost and low risk.
The VanDusen Botanical Gardens Visitor Centre is recognized throughout North America as one of the leading, pioneering green structures. Concerns regarding the concrete waterproofing selection went further than just the prevention of water penetration—it also had to fit strict criteria to fit in to the LEED Platinum parameters.
Using the crystalline system to waterproof the shotcrete also added sustainable benefits to the building including:
- making the shotcrete mixture more plastic and creating a higher-end architectural finish to the concrete walls without requiring sealers or finishers;
- the integral admixture reduces site disturbance as no excavation is needed for application;
- no VOCs;
- positive contribution to the structure’s overall durability and life expectancy by stopping corrosion, increasing freeze/thaw durability, and protecting against chemical attack; and
- permitting the concrete to be recycled at the end of the structure’s life.
Conclusion
The VanDusen Visitor Centre project has won numerous awards for its design and implementation, including:
- Lieutenant Governor’s Award for Engineering Excellence by the Association of Consulting Engineering Companies, British Columbia (ACEC-BC);
- five Vancouver Regional Construction Association (VRCA) awards for contractors and trades;
- Lieutenant Governor of British Columbia Award in Architecture, merit level, by the Architectural Institute of British Columbia (AIBC); and
- first place in the inaugural World Architecture News (WAN) Engineering Awards, based out of London, England.
The building successfully achieved its goal of being self-sufficient and carbon neutral, along with LEED Platinum and is on its way to becoming the first fully certified Living Building Challenge structure in Canada.
Jeff Bowman earned his bachelor’s degree in chemistry from the University of British Columbia in 2002 before joining Kryton International, the same year. He has extensive experience in the development and use of various construction products for the repair and waterproofing of concrete, specializing in crystalline admixtures and repair materials. Bowman has written numerous articles on waterproofing technologies and has contributed to international publications on this topic. He is primarily active within North America, but has consulted on various projects worldwide. Bowman can be reached via e-mail at jeff@kryton.com.