Waterproofing construction joints
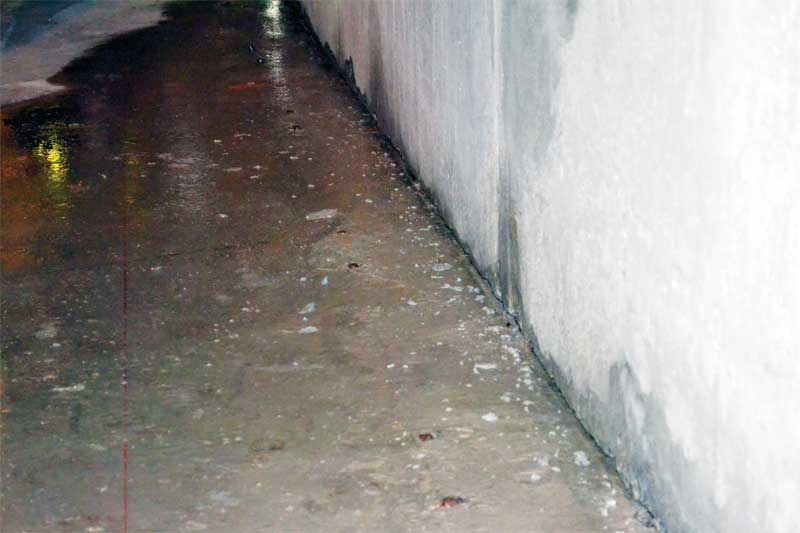
PVC waterstop
PVC waterstops are also known as ‘dumbbells’ due to their shape. These plastic sheets are placed across the joint before concrete is poured, creating a physical barrier blocking water penetration. This particular type of waterstop relies on the ribs in the concrete design to prevent water from passing through the joint.
The PVC waterstop is great for blocking water and relatively inexpensive, but has limitations. Improper compaction around the waterstop can result in a high probability of honeycombing, while concrete shrinkage can lead to the formation of small gaps between the PVC and concrete. This material does not bond well to concrete and can be tedious to install. Further, it can bend while concrete is poured, forming a tunnel where water can infiltrate.
These issues create instances where water leakage can exist. This is not to say PVC is not an effective waterstop product, but rather it does support the 99 per cent principle, given its installation is difficult and often done incorrectly. Leakage does not necessarily occur due to the fact the waterstop is not working, but instead because of an error in installation. To make matters worse, once a problem has been created, it is virtually impossible to recognize until the joint begins to leak.
Over the past 25 years, more advanced and economical waterstops and materials for joints have been developed, many of which are easier and more efficient to use than older models.
Bentonite strip
Bentonite strips have increased in popularity in the waterstop market, and traditionally work well in various situations. Bentonite is a hydrophilic clay material applied at the construction joint to stop the flow of water through concrete in vulnerable areas. Unlike the PVC waterstop, bentonite has the ability to expand several times its volume when it comes in contact with water, filling voids in concrete and forming a watertight seal.
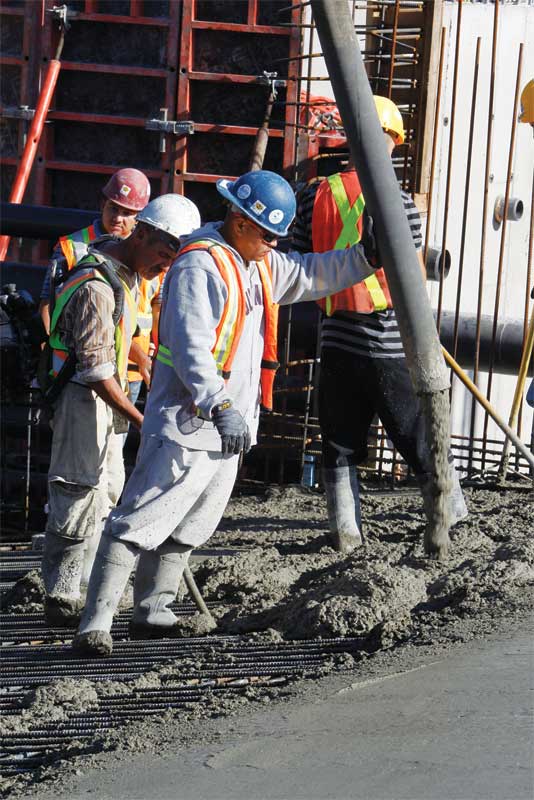
Further, these strips are flexible, allowing for ease of application. They require no special pieces or procedure to connect, as the ends join naturally together to form a continuous waterstop. These strips have also proven effective under continuous or intermittent hydrostatic pressure. Additionally, bentonite waterstops’ swelling capabilities allow them to block the intrusion of water to a greater capacity than a PVC product, which only acts as a physical barrier. This capacity also allows bentonite to fill voids and cracks to compensate for poorly consolidated concrete.
However, there are also a few drawbacks to using bentonite strip. It can:
- swell before concrete is poured if it comes into contact with moisture, and not return to its original shape;
- break apart and deteriorate over time (a process limiting its long-term ability under hydrostatic pressure); and
- not swell enough when encountering either saltwater or contaminated water.
Synthetic rubber swelling strip
Synthetic rubber strips are also hydrophilic waterstops. They are extremely effective at keeping water out of construction joints, creating a more durable concrete structure. This product’s material and innovative design allows it to stop water not only under normal conditions, but also when high hydrostatic water pressure is involved. Such conditions can occur with structures built in or near a harsh marine environment, and in below-grade applications where water pressure is a concern.
Synthetic rubber swelling strips have a great swelling capability within the joint. Unlike bentonite or other clay-based hydrophilic strips, they have a controlled swell within the joint, only swelling to fill the voids in concrete. Like bentonite, however, if the concrete is poorly compacted, the rubber strip will fill voids and cracks, blocking water and chemical infiltration.