Waterproofing considerations for green roofs
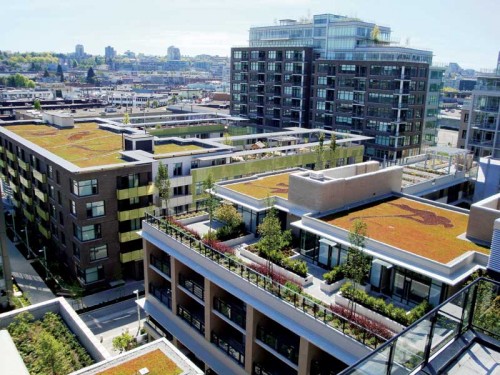
By Karen Liu, PhD
Green roofs are continuing to gain recognition as a sustainable building design feature throughout North America. These vegetated assemblies contribute to many credits under the Canada Green Building Council’s (CaGBC’s) Leadership in Energy and Environmental Design (LEED) program.
To ensure performance of these systems, the Single-ply Roofing Industry (SPRI) association has passed two design standards and a test procedure specific for vegetative roofs in the last couple of years. Further, Factory Mutual (FM) Global issued Approval Standard for Vegetative Roof Systems (Class Number 4477) in 2010.
Despite the rising popularity of green roofs, many designers are still inexperienced in properly specifying them. Roofing professionals are often nervous in installing a system for green roofs, where the roof membrane is exposed to constant moisture and leaks are hard to find and repair. A green roof can also expose the roof membrane to chemical inputs (e.g. fertilizer), aggressive roots, and increased foot traffic.
A robust and durable roofing system is necessary to provide a solid foundation for green roofs. Architects and specifiers are often faced with the (over-simplified) question, ‘What is the best roofing/waterproofing system for green roofs?’ This article helps answer this query.
Roofing assemblies
There are two common configurations of roofing systems depending on the relative placement of the roof membrane and the thermal insulation—the compact conventional and the protected membrane roofing assembly (PMRA). A green roof can be installed on either, each with its own pros and cons.
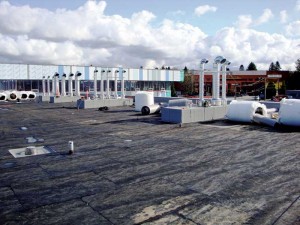
In a conventional system, the green roof is installed atop the membrane, which sits on the thermal insulation. Since the membrane is located directly under the green roof, it is easier to locate and repair should a leak occur. However, the high foot traffic during green roof installation increases the probability of mechanical damage on the membrane. Therefore, some roofing manufacturers require an asphaltic core board or a protective fleece to be placed atop the membrane as part of their specification for green roof applications.
Additionally, it is important the insulation has good compressive strength and creep resistance to support the green roof system’s additional weight for long-term success. A cover board can also be placed on the insulation to help distribute the load more evenly and minimize damage to the insulation facer.
In a protected membrane roof assembly, the green roof system sits on the thermal insulation, which is placed above the membrane. The advantage of this configuration is the thermal insulation protects the roof membrane from mechanical damage during installation. However, it is important the green roof does not prevent topside venting of any residual moisture in the PMRA—one must ensure a ‘diffusion-open’ assembly. This can be achieved by having a ventilating space (i.e. air- and vapour-permeable) above the insulation. If vapour cannot escape, it could be driven back into the insulation, reducing its thermal resistivity. Therefore, one should not place vapour retarders such as root barrier, saturated drainage felt, or a water-retention mat directly atop the insulation when installing a green roof system on PMRA. Instead, it is critical to use the stone ballast or a preformed plastic drainage sheet to provide drainage and the necessary ventilation.
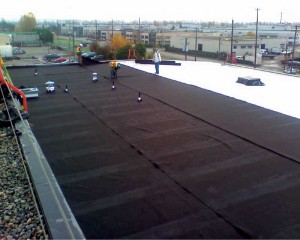
Roof membranes
A green roof often means more foot traffic to the rooftop during installation, normal use, and regular maintenance—this increases the probability of mechanical damages of the roof membrane. The membrane is also constantly exposed to moisture, chemicals, and roots. Additionally, it is difficult to locate leaks and it is labour-intensive to repair them. Therefore, it is important to install the most robust and durable roof membrane with good workmanship on green roofs for long-term performance.
Green roofs should only be installed on waterproofing (but not water-shedding [e.g. shingles]) systems to prevent water ingress. In addition to the general requirements such as strength, elongation, and low-temperature flexibility, the ideal roof membrane for green roofs should have sufficient thickness. For example, the Roofing Contractors Association of British Columbia (RCABC) requires single-ply and modified bituminous (mod-bit) membranes to have a minimum thickness of 1.5 mm (60 mil) and 3.7 mm (145 mil), respectively, for its RGC guarantee program. It should be resistant to:
- hydrolysis;
- chemicals (e.g. organic and synthetic fertilizers);
- micro-organisms;
- root penetration; and
- foot traffic.
Redundancy in the system should also be considered.
Liquid-applied roofing
Liquid-applied roofing (e.g. rubberized asphalt) is commonly used in waterproofing for intensive green roof systems. One of their advantages is they can be installed on a very low slope (less than two per cent). Since the waterproofing layer is quite thin, good workmanship is important to ensure uniform coating thickness. A protection layer is often required to protect the waterproofing from foot traffic during installation.
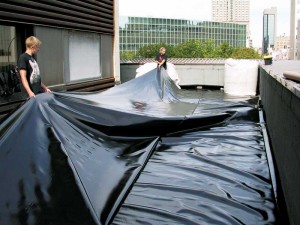
Single-ply
Single-ply roofs—such as ethylene propylene diene monomer (EPDM), thermoplastic polyolefin (TPO), and polyvinyl chloride (PVC)—are gaining more popularity in Canada because of their easy installation. This type of roofing consists of a reinforcement fabric sandwiched between two polymer sheets. Single-ply membranes are thin, usually ranging from 0.7 to 2 mm (30 to 90 mil).
A protective fleece at a minimum weight of 500 g/m2 (0.1 psf) is recommended, especially on the thinner membranes, to protect them from foot traffic during installation.
Two-ply mod-bit
Two-ply modified bituminous products are the most commonly used membranes for green roof applications. They consist of a reinforcement fabric sandwiched between two layers of modified bitumen. Each ply is quite thick at 3 to 4 mm (0.12 to 0.16 in.) and the second ply further adds redundancy. A protective layer is optional for mod-bit membranes.
Root resistance
Aggressive roots and rhizomes can damage the waterproofing layer. The fine root tips can go into small crevices on the membrane’s surface or at the seams; they can then grow and eventually breach the waterproofing. Some roofing membranes and joining methods are more resistant to root penetration than others.
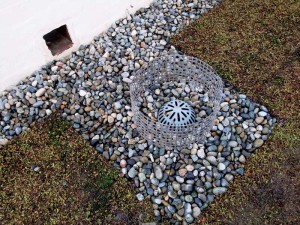
There is a test method for root resistance—American National Standards Institute/Green Roofs for Healthy Cities/SPRI (ANSI/GRHC/SPRI) VR 1-2011, Procedure for Investigating Resistance to Root Penetration on Vegetative Roofs, based on Germany’s Landscape Research, Development, and Construction Society (FLL) Guideline for the Planning, Execution, and Upkeep of Green Roof Sites. This involves exposing a membrane sample (with side and end seams) to aggressive roots and rhizomes in a trial container in controlled greenhouse conditions for two years. Membranes passing the test receive certificate. However, some plants with very aggressive roots and rhizomes, such as bamboo and Chinese reeds, are perhaps best to avoid on the roof altogether.
The best option is to select a roof membrane with built-in root resistance. Some single plies available in Canada, such as PVC and TPO, have been certified as root-resistant. Some mod-bit membranes have a protective sheet/coating that prevents root penetration. In Europe, copper foil is sometimes embedded in mod-bit membranes formulated with root repellent to provide physical and chemical protection against root ingress.
For those membranes not certified as such, the designer should specify a root penetration barrier to protect them from this damage. There are generally two types of root barriers—physical and chemical. The former are simply flexible sheets that block root ingress. They are usually made of polyethylene, PVC, or TPO. The designer should check with the manufacturers for chemical compatibility with the roof membrane. It is important the root barriers be installed with proper laps and seams per the manufacturer’s instructions.
Chemicals (usually copper-based compounds) that inhibit growth can be used with geotextile materials to protect the roof membrane. Since they may leach into water runoff over time, their use should first be reviewed for compliance with local environmental laws.