Waterproofing breaches that lead to major structural restoration
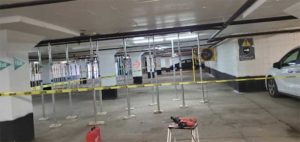
by Daniel Aleksov, P.Eng., BSS
When performing a walkthrough of a building and observing symptoms of degradation of the concrete structure one will certainly ask themselves “Why is this happening?” The short answer is the concrete was inadequately protected. Concrete is a durable material that has stood the test of time, but in the modern age, it has a fundamental weakness that depends on how it is reinforced. Ironically, the steel used to increase concrete’s tensile strength is also its weakness when it is subject to attack from foreign contaminants such as water, oxygen, carbon dioxide, chlorides, and aggressive chemicals.
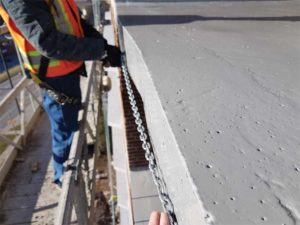
These foreign contaminants induce steel corrosion which is the leading cause of concrete deterioration. Although concrete naturally protects the embedded steel, it has its vulnerabilities due to its porous nature and is susceptible to cracking when it undergoes volume changes. Cracks, joints, and penetrations coupled with unprotected concrete are a path of least resistance for moisture along with the other contaminants to reach the embedded steel. As the steel corrodes over time, it increases in volume and exerts pressure on the surrounding concrete which leads to delamination (separation of concrete layers) and spalling (detaching from the structure itself).
All these symptoms are indications the concrete is in distress and requires immediate attention. The corrosion and section loss of the steel jeopardizes the load-carrying capacity of the concrete and has the potential to lead to catastrophic failure if measures are not taken to temporarily support and rehabilitate the structure. This is why it has been understood for well over 50 years that concrete requires protection and the concept of a waterproofing barrier system was developed.
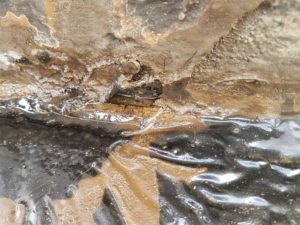
Protecting structural components from water penetration
A waterproofing barrier is a combination of systems and materials designed to resist hydrostatic pressure exerted by moisture in a liquid state. Its sole purpose is to protect the structural components from water penetration and, by extension, into a usable space. To have a successful barrier, it must be continuous from slab to walls and other surfaces subject to liquid moisture. Waterproofing barriers traditionally consisted of multiple layers of bituminous saturated felt bonded together with hot applied coal tar pitch or asphalt. Currently, hot applied rubberized asphalt membranes are still commonly installed, but there is a vast array of other waterproofing barrier types used such as cold applied rubberized asphalt, elastomeric thin system membranes, cementitious coatings, modified bituminous asphalt, polyvinyl chloride (PVC), bentonite clay, etc. The focus of this article will be on fluid applied waterproofing membranes primarily on horizontal portions of traffic surfaces.
The five most common types of waterproofing breaches for liquid applied membranes are as follows:
- Pinholing is a phenomenon that occurs when trapped air outgasses from the waterproofing coating creating bubbles that burst and leave behind small craters. Some of the causes of this condition include but are not limited to a porous or uneven concrete surface, dampness, direct sunlight, insufficient primer application, and a high ambient or substrate temperature. Following the waterproofing membrane manufacturer’s application instructions is essential to avoid this type of issue with respect to surface preparation, primer coverage rates, temperature, and humidity ranges as well as environmental conditions conducive to proper curing.
- Wrinkling occurs in the form of bubbling when water penetrates and migrates below the membrane or is absorbed from the concrete. That is why it is imperative for the concrete substrate to be within acceptable limits with respect to moisture content.
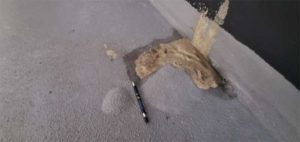
Verification of moisture content can be performed by various methods including the plastic sheet method or a handheld moisture meter. However, in colder weather, when there is limited vapour drive, an in-situ probe should be used to obtain a more accurate reading.
It is also important to understand if the substrate consists of a hollow core slab or composite metal deck which will require venting to allow the moisture to dissipate. Wrinkling can also develop during the installation of elastomeric reinforcing sheets during hot-applied rubberized asphalt which will create a tunnel-like opening at the seams for water to penetrate. This condition is also common for sheet-applied waterproofing membranes that rely on fusing two adjoining rolls of the membrane at side and end laps.