Waterproofing breaches that lead to major structural restoration
Maintenance
The minimum maintenance standards involve annual reviews by building staff ensuring the slabs’ drains are free of debris and vehicle traffic waterproofing systems are cleaned on a regular basis. Part of this review should include accessing the hydro vault to ensure there is no evidence of water penetration which could cause a potential fire or explosion.
Localized repairs and replacement of worn and debonded membranes should be addressed as part of a maintenance plan to avoid leaving the concrete unprotected and exposed to water and de-icing salts which can lead to corrosion of the embedded reinforcing steel. The Canadian Standards Association (CSA) 413, Parking Structures, under Annex E.1, routine maintenance clearly states, “the cost of repairs to protection systems is a small fraction of the cost of repairing consequential damage to the structure.” Based on practical experience, the average cost difference to repair the structure is a minimum of 10 times the cost to repair the waterproofing system.
Repairs
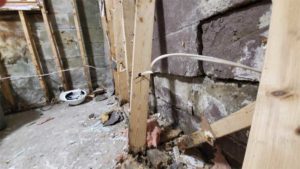
Full replacement of waterproofing membranes at the end of their service life is inevitable and requires diligent financial planning since these types of projects can be quite costly when major structural restoration is involved. Depending on the first four factors, this can have a tremendous impact to the service life of the waterproofing and the repair strategy. For the waterproofing system to perform to its maximum potential, action needs to be taken promptly when problems initially occur.
References
American Concrete Institute (ACI) 515.1R “A Guide for the Use of Waterproofing, Dampproofing, Protective, and Decorative Barrier Systems for Concrete”
• Canadian Standards Association (CSA) S413-07, Parking Structures
• International Concrete Repair Institute (ICRI) Guideline No. 310.2R-2013, “Selecting and Specifying Concrete Surface Preparation for Sealers, Coating, Polymer Overlays, and Concrete Repair”
• ICRI Guideline 710.2-2014, “Guide for Horizontal Waterproofing of Traffic Surfaces”
Daniel Aleksov, P.Eng., BSS is a principal and co-founder of Leading Edge Building Engineers and a senior structural engineer specialized in the restoration and renewal of existing buildings. He has spent more than a decade assisting building owners and property managers solve water penetration and building component failures with durable and cost-effective solutions. At Leading Edge, he is responsible for all technical aspects of building envelope and structural restoration projects from the initial assessment phase to the design and construction completion. He has successfully completed more than 300 engineering projects related to underground parking garages, site works, landscaping, windows, walls, sealants, roofs, balconies, plumbing and HVAC. Over the last five years, Aleksov has been cultivating his creativity which has helped him develop his own quality control tool and use new technology such as drones and wireless concrete sensors for building applications. He has also contributed valuable insights on social media as well as shared perceptive and thoughtful presentations with all stakeholders in the industry. He is an active member with many professional organizations and serves as a board of director for the Ontario Building Envelope Council (OBEC) and chairs the communication committee. He is also involved with the International Concrete Repair Institute (ICRI) and volunteers for the concrete repair and waterproofing committees. He is committed to lifelong learning and creating a positive impact to the engineering and construction industries.