Waterproofing breaches that lead to major structural restoration
- Blistering is a type of breach that occurs when liquid-applied polyurethane membrane layers are applied too thick causing the coating to become spongy and soft. Exceeding the manufacturer’s design thickness requirements, using the wrong tools, as well as having a very rough concrete surface profile can cause this to happen.
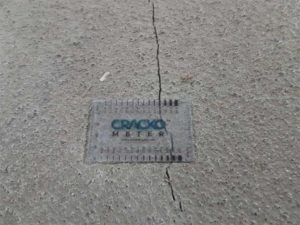
During membrane installation, it is important to perform quality control measures such as measuring the wet film thickness. Any depressed or rough areas should be filled prior to membrane application. Larger blisters can also form from moisture migration which originates from the concrete having a high moisture content.
- Splitting develops when the waterproofing system cracks due to excessive movement beyond its elongation capability. Inadequate detailing of cracks or construction joints, excessive slab movement due to thermal effects or slab deflection, as well as a thicker-applied coating (polyurethane systems) are the leading causes of this type of failure. The type of crack treatment will depend on crack widths encountered following surface preparation of the concrete substrate.
Cracks with widths less than 1.6 mm (0.0625 in.) will require a detail coat of waterproofing membrane above the crack prior to the entire base coat application. When cracks exceed 1.6 mm then it is industry standard practice to rout and seal the crack with sealant followed by a detail coat. For rubberized asphalt waterproofing, different reinforcements are used in conjunction with detail coats based on the crack width criteria.
For larger movement joints such as those that are classified as expansion joints, this requires even more careful attention to detail to ensure splitting does not occur. Waterproofing is engineered and tested to an optimal thickness to produce the desired elongation capability. Excessive thicknesses during waterproofing membrane application can create a more rigid system which reduces the waterproofing’s capability to bridge cracks effectively.
- Delamination is an indication the waterproofing membrane is poorly bonded to the concrete substrate and has peeled off or is at high risk to occur. Areas of exposed concrete and peeled-off waterproofing coatings can be easily identified visually. However, other areas may appear sound visually but may be completely debonded.
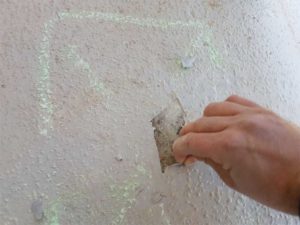
On exposed traffic waterproofing coatings, this can be detected by chain dragging the top surface which is a non-destructive method by acoustic sounding. Another method of assessing the bond of the waterproofing membrane is by performing a test cut and verifying the adhesion qualitatively.
For elastomeric traffic waterproofing coatings, adhesion tests can also be completed with a portable device that can measure quantitatively the pull of strength (bond strength). This breach can originate due to inadequate surface preparation, moisture, contaminated slab, insufficient membrane thickness, damage from vehicle impact, and chemical exposure. To avoid delamination and achieve a good mechanical bond, surface preparation by abrasive blast cleaning (shot blasting) is recommended to obtain a concrete surface profile of three to four.