Virtual Air Barriers: The DBZ solution for humidity resolution in an apartment building
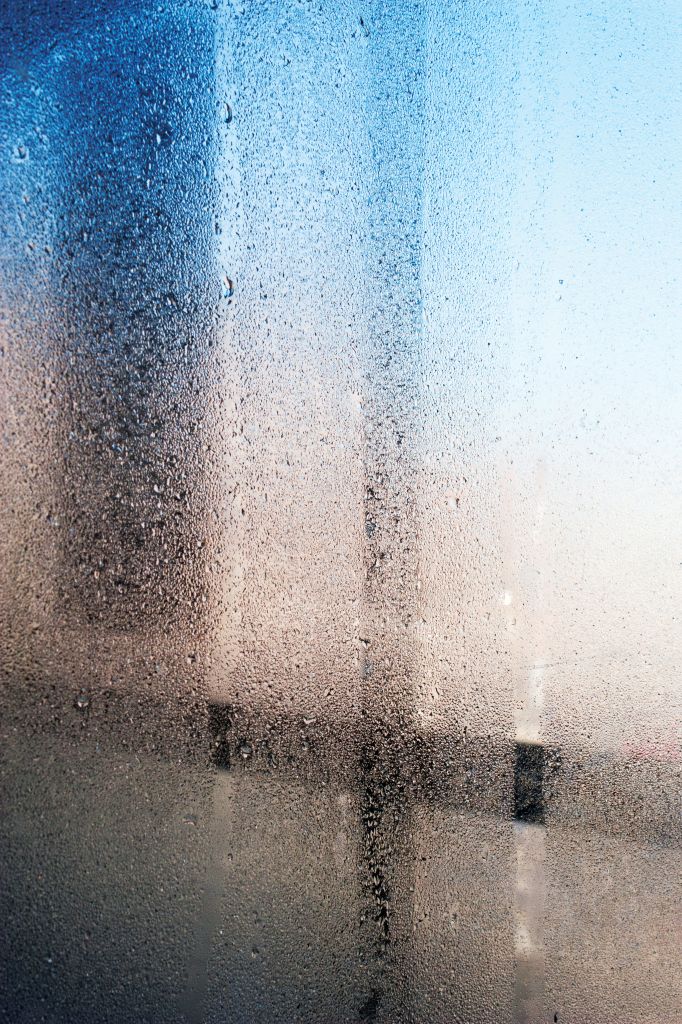
By Rick Quirouette, B. Arch.
In the July 2013 issue of Construction Canada, this author’s introduction to the virtual air barrier and dynamic buffer zone (VAB/DBZ), “Designing the Virtual Air Barrier,” was published.1 This article explained a research project on the basic science and technology of the VAB/DBZ to control condensation within the exterior walls of a large heritage building in Ottawa. The heritage building was humidified in excess of 60 per cent relative humidity (RH) to demonstrate and measure the concept’s performance characteristics. The article provided a substantial description of the experimental setup, instrumentation, testing protocol, observations, and the first set of criteria suitable for designing, constructing, and operating a VAB/DBZ.
In this article, the VAB/DBZ concept is applied to an apartment building with severe, high indoor humidity conditions and condensation problems. Specifically, the windows and exterior doors of all eight apartment units within the building exhibited severe window condensation during the fall, winter, and spring—this included wetness on floors, mould production, and sustained indoor high humidity in the structures every winter for more than a decade. This condition occurred in the apartments regardless of the number of occupants and their lifestyles. In the summer, indoor conditions were stifling with higher than normal indoor relative humidity (RH).
The problem
It is a common assumption high indoor humidity conditions result from the lifestyle of occupants. People may have too many plants, activate humidifiers for long periods, or dry clothes in bathrooms. Conventional wisdom has concluded most condensation problems, along with mould production and even water damage from condensation, are caused by these living habits. However, is this assumption correct?
Research undertaken by this author in the 1980s, and experience with many such problems throughout Canada, has revealed living habits are an uncommon cause of high humidity and condensation problems in apartments and other residential buildings.2 There are many other reasons for these conditions, none of which are caused by the occupants or living habits. (See “Sources of Moisture Other than Occupants.”)
The high humidity conditions and condensation problems of the building examined in this article are a particular example of these incorrect assumptions. Sustained high humidity conditions in the apartments led to various occurrences of moisture damage, including:
- sustained window frosting in winter and wetting of sills and walls;
- operable windows and balcony doors that would not open or close properly in winter due to frost and ice formation;
- water leaking on kitchen and laundry floors from back wall in the spring; and
- paint peeling, gypsum board stains, and other moisture damage (Figure 1).
The condensation on the windows created a further complication. The swelling of the wood frames made it hard to close the window, thereby promoting frost buildup at its edges. Additionally, it was noted small amounts of mould had formed on various surface areas of the outside walls, particularly corners and on windows sills. The RH levels varied slightly between apartments, but the high RH conditions of 30 to 50 per cent in winter were essentially the same in all apartments.
The building owners tried to correct the problem using conventional methods of ventilation, tenant advisories on how to minimize moisture production, window repairs, and mould cleanup. Maintenance repairs were undertaken annually, but the high RH conditions occurred year after year for nearly all of its occupancy period—over a decade. The high humidity conditions continued, and even appeared to worsen over the years. All conventional methods of RH control failed.
The building
This project involved an apartment building constructed in the early 1990s. It included eight two-storey apartments stacked one above the other (Figure 2). The building was constructed with cast-in-place concrete floors, walls, and ceilings. Its back wall, separating two different occupancies, also separates the apartment units from a large, outdoor, unheated storage area.
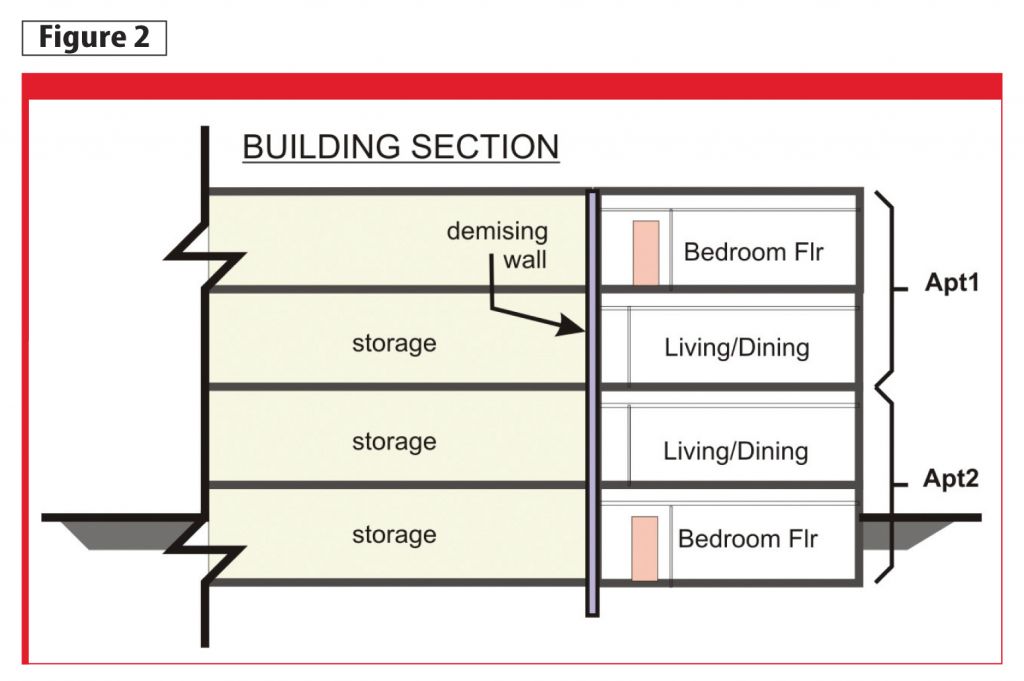
The rear wall of the apartments—a back, fire-rated wall—was constructed with:
- 300-mm (12-in.) concrete wall;
- 50-mm (2-in.) cavity;
- 150-mm (6-in.) steel stud with cavity insulation; and
- foil-backed gypsum wall board finish (Figure 3) that provided the required vapour retarder and an air barrier as per 1995 National Building Code of Canada (NBC).
The apartment units are electrically heated and equipped with a bathroom and kitchen on one floor, and a full bath and storage room with laundry facilities on the other. The kitchen and bathroom exhaust ducts are routed in the back wall cavity, then up and into a suspended ceiling above the laundry, bathroom, and kitchen. It is also enclosed in a bulkhead routed across the ceiling of the corridor and living room on one floor, and a bedroom on the other, before discharging the humid air to the outside near the balconies. The laundry rooms are equipped with washers and dryers, and there are no fireplaces in the unit.
The investigation
An investigation was undertaken on the buildings in 2002 and 2003. In early February 2003, two apartments were instrumented to measure and record two months of indoor temperature, RH, and air pressure difference with the outdoors. The temperature and RH sensors were located on each floor, as well as in the storage area and the outdoor side of the balconies.
In late March 2003, all the apartments were examined to view indoor conditions. This included the retrieval of monitoring data of the history of temperature, RH, and air pressure measurements. It was also reported that upon a warm-up cycle, water would often leak from the back wall onto the laundry and kitchen floor for two or three days in the spring in many, but not all, apartments.
The occupancies of all apartments were surveyed to assess the indoor conditions and living habits. Some units housed large families, most were occupied by only two people, and a few were vacant all winter. Nevertheless, all apartments had about the same high humidity conditions.
From the analysis of the monitored data, it was generally noted the indoor RH varied between 40 and 60 per cent in two of the apartments with an indoor temperature range of 19 to 22 C (66 to 71.6 F) and outdoor temperatures range of –20 to –5 C (–4 to 23 F).
In August 2003, a test opening in the back wall of one apartment was examined and photo-documented. It was noted there was corrosion on the steel stud track on the floor (Figure 4), the gypsum board was not sealed to the underside of the ceiling, and there were numerous unsealed duct joints leaking into the back wall’s cavity.
Causes of building humidity
From the observation and analysis of the building design and construction, and knowledge of the problem’s history, it was concluded the indoor high humidity conditions resulted from the storage and release of moisture in and on the concrete back wall.
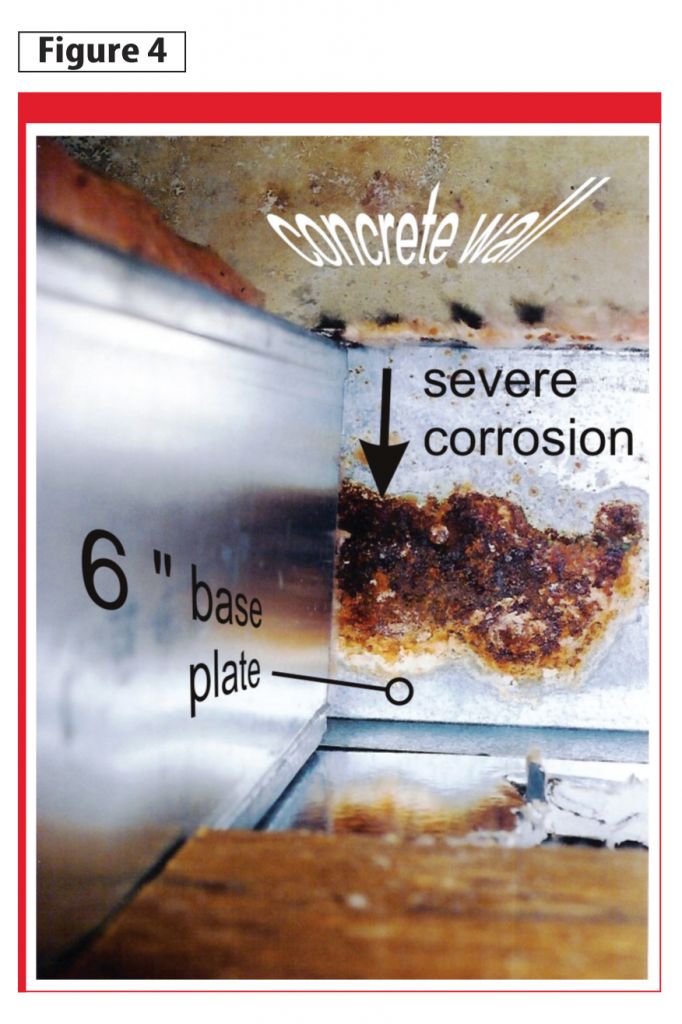
Concrete is known to store large amounts of moisture with no visible signs of wetness. It was estimated the concrete wall area between the outdoor storage and any apartment could store and release upward of 1890 to 2225 L (500 to 600 gal) of water over one year. This is assuming a modest moisture content increase in the concrete from eight to 12 per cent. This also means the concrete released most of this moisture through the year as the concrete wall temperature rose above the departments’ indoor dewpoint temperature.
In the spring, summer, and fall, moisture from the concrete back wall is released into the back wall cavity and then into apartment spaces. In winter, when the back wall is cold and possibly frozen, moisture also accumulates as frost on the apartment side of the concrete surface. It is this moisture that appears on the floor of the kitchen and laundry rooms in late spring during a warm-up cycle (Figure 5).
Further analysis revealed the stored moisture of the concrete originated from air leaks in the joints of the exhaust ducts of the dryer, stove vents, and bathroom vents on both floors. The ducts were routed within the back wall cavity. This equipment would be used daily to contribute significant humid air into the cavity. The moisture in the air then condensed on the cold concrete wall surface to be absorbed and later released.
The same duct pressure then forces the wall cavity’s humid air to leak back into the apartments in the spring, summer, and fall. The humid air from the back wall cavity flowed into the apartments through numerous discontinuities in the gypsum board finish, including a discontinuous foil-backed gypsum board at the concrete ceiling, unsealed duct penetrations, and various cracks at gypsum terminations. This caused sustained high humidity conditions throughout the spring, summer, and fall.
It became clear the occupant living conditions had little to do with the high humidity conditions of these apartments. The sources of moisture were then the kitchen stove vent, bathroom vents, and laundry dryer. All these sources were supposed to be exhausted to the building’s exterior. However, because of the long duct run to the outdoor, the duct air resistance backed up the duct pressure, resulting in leaks at unsealed joints. Humid air from the exhaust ducts was injected into a cold cavity to deposit condensation while exhausting only a small amount of humid air through the outdoor vent.
VAB/DBZ for the apartments
It became obvious a remedial repair strategy would involve the redesign and construction of the back walls for each apartment. The equipment in the bathroom and kitchen would require removal, as well as disconnection of various electrical and plumbing services and the back wall gypsum board and insulation. This repair method would be expensive and disruptive to tenancy. In 2003, the estimated cost was approximately $20,000 per apartment, plus the cost of moving tenants for up to three months.
Though unproven by industry standards, it was decided to apply the VAB/DBZ concept to the individual apartments. This repair strategy would be applied initially to two apartments. If the performance proved successful, the method would be extended to all apartments. The estimated cost of providing each apartment with a VAB/DBZ application was approximately $5000.
A VAB/DBZ application combines architectural modifications coupled with a simple mechanical pressurization system. The architectural modifications consist of defining a pressure zone within the building enclosure and sealing the holes and openings of the surface areas defining the pressure zone—this could be a wall or roof cavity, a partition wall, and even a suspended ceiling.
To seal the pressure zone, all joint cracks, holes, and openings must be closed with rigid materials. Specifically, perimeter gypsum board joints at the floor, partition walls between apartments, and concrete ceiling were taped with gypsum mud and tape. The duct openings between the equipment, the back wall cavity, and a few cavity openings (i.e. a door header), were capped. The workmanship was of standard quality, solely inspected for continuity.
Additionally, the bulkhead cavities across the living room and the bedroom leading to the exterior wall were isolated from the exterior wall cavities. Sealing consisted primarily of using a butyl caulking, plywood collars for large holes at duct penetrations, and gypsum plaster for all other cracks and joints. Lastly, the exhaust duct joints were resealed where possible.
For the living/dining room floor, the pressure zone (Figure 6) consisted of the back wall cavity, the kitchen’s suspended ceiling cavity, and the bathroom. Further, the pressure zone included a duct chase bulkhead from the hallway through the living/dining room connected to the exterior wall. The bulkhead included the original exhaust ductwork from the indoor appliances of the kitchen and bathroom.
On the bedroom floor, the pressure zone consisted of the back wall cavity, the laundry and bathroom suspended ceiling, and a duct chase extending from the suspended ceiling through a bulkhead on the ceiling between two bedrooms that extended through the exterior wall to the outdoor vent.
The mechanical pressurization system consists of a simple in-line ventilation fan, speed controller, and a heater to warm the supply air. The fan size is calculated by determining the back wall area and multiplying by 19 L/sec/9 m2 (40 cfm/100 sf) of wall.3
For this building, each floor of each apartment was treated as a separate volume to receive the features of a VAB/DBZ system. The mechanical pressurization system consisted of a 70 L/sec (150-cfm) in-line fan, of a quality that could continuously operate for several months. The fan pressure head was limited to 125 Pa (0.5 in. H20). This pressure is insufficient to detach a gypsum panel from a wall or to pop various joint seals.
The in-line fan was installed in the bulkhead near the outside wall and suspended on springs to minimize fan noise (Figure 6). On the outdoor side of the exterior wall, below the exhaust air damper, a new opening was cut into the brick veneer. Then, a 100-mm (4-in.) diameter insulated duct was put through the new opening in the brick and connected to a 100 x 300-mm (4 x 12-in.) goose neck. The insulated duct was connected with the in-line fan in the bulkhead. The goose neck was pointed downward to prevent snow entry. The fan was wired for 120 Volts with a manual speed controller placed in an inspection hatch for adjustment at commissioning and maintenance time.
The in-line heater was equipped with a temperature sensor installed about 1.2 m (4 ft) ahead of the heater and a thermostat set to 15 C (59 F). Additionally, to provide a small amount of fresh air to the indoor space of the living room or bedrooms, a celling grille and damper control was installed in the existing bulkhead. No further equipment was required.
Operation of the VAB/DBZ
At commissioning time, the VAB/DBZ fan was turned on and the fan speed adjusted until the VAB/DBZ cavity exhibited 5 to 10 Pa (0.02 to 0.04 in. H2O) pressure above the ambient pressure of the indoor spaces (measured with a 250-Pa [1-in. H2O] mechanical manometer). If the VAB/DBZ cavity exhibited a pressure higher than 10 Pa (0.04 in. H2O), the fan speed was reduced. (This implies the architectural modifications were well thought-out and constructed.)
If the cavity pressure had not risen to the intended pressure range, there may be too many unsealed openings leading from the pressure zone. These are easily found by listening for air or whistling noises or with a simple smoke test. If it appeared too cumbersome to trace and correct the excessive VAB leakage locations, the system can still perform flawlessly because it is flushing out all residual moisture and forcing the pressure cavity to dry out completely by dilution with dry air. This condition may require more heat and fan energy. It is generally more cost-effective to locate air leaks and continue with a second round of sealing the VAB/DBZ pressure zone. (There was no need for a second round of pressure zone sealing in this project.)
For the system to perform as intended, its supply must always be outdoor air, and never indoor air from corridors, elevator shafts, mechanical rooms, or any other indoor heated space or unheated crawlspace. This is because outdoor air almost always has a dewpoint temperature lower than the outdoor temperature; it cannot condense anywhere within the walls or any cavity within a building enclosure. For the brief periods when the outdoor humidity is at 100 per cent (e.g. during a rainy day or a snowstorm), the actual moisture content of the supply air is so small as to be negligible.
Conclusion
Problems of high humidity in an apartment building or other residential building are often directed at the tenants and/or owners. In nearly 20 investigations of high humidity problems undertaken in Canada, not one of those investigations was directly related to the tenants or owner’s lifestyle conditions. This is not to say none exist, but they are truly rare.
The application of a VAB/DBZ system is failsafe concept, except when the VAB/DBZ fan is turned off. If the pressure difference is high and within the range of the intended control limits, then the cavity pressure pushes a small amount of dry cavity air to the indoor spaces. By lowering the pressure difference to 5 Pa (0.02 in. H20), then even less or no cavity air will enter the apartment spaces. The cavity pressure contained by the VAB prevents the entry of humidified air into the pressure cavity volume thereby preventing condensation within the pressure cavity.
Alternately, if the pressure zone is not as well sealed as expected, the pressure in the cavity will be low or undetectable, but the flow of outdoor dry air into the pressure zone will be high. This larger supply of outdoor heated air will dilute and expel humidity from the pressure zone quickly and permanently. This is why it is called a failsafe method. It performs its objective satisfactorily regardless of the design quality, the pressure zone’s construction, or the rate of supply air changes within the VAB/DBZ cavity.
There are many types of apartment buildings where this technology would perform better than most architectural solutions. This is not because the architectural intent is incorrect, but because it cannot be built to the expected standard of quality available. Standard apartment buildings with concrete end shear walls often experience this type of condensation problems. This technology is easily adapted to these building types. Wood-framed apartment buildings can also benefit from this technology, particularly where firewalls exist to conduct condensation air into attics and under roof surfaces.
In the case of the apartment building featured in this article, the operation of the VAB/DBZs of the two test apartments performed as expected. The indoor humidity fell to normal levels within two months of startup and has remained stable ever since. Later, the VAB/DBZ technology was applied to the remaining apartments of this complex. It has performed correctly in all units with minimal intervention and returned the indoor conditions of temperature and humidity in all apartments to normal levels.
Notes
1 See Rick Quirouette’s, “Designing the Virtual Air Barrier” in the July 2013 issue of Construction Canada. (back to top)
2 For more information, see “Moisture sources in houses,” from Conference Proceeding Building Science Insight at www.irc.nrc-cnrc.gc.ca/pubs/bsi/83-2_e.html. (back to top)
3 See Note 1. (back to top)
Rick Quirouette, B.Arch., is a senior building science specialist with almost four decades of experience in building science and technology. He is a life member of the Alberta Building Envelope Council (ABEC) and a past-president of the National Building Envelope Council (NBEC). Operating as Quirouette Building Specialists Ltd., he can be reached at rick.quirouette@sympatico.ca.