Virtual air barrier and dynamic buffer zone for a heritage building envelope
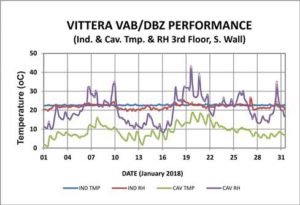
Figure 1 illustrates the wall composition of the south and west elevations of the building. The north and east elevations are similar but with a terra cotta stone cladding instead of a brick veneer. Insulation or well-defined wall cavities were not found in the test openings. It was hypothesized from the crushed masonry infill the exterior wall would transmit cavity pressure around the building envelope. In a separate investigation of the wall cavity porosity, a pressure test of the wall cavity was undertaken.
A commercial vacuum cleaner acting as an air pump was connected to an exterior wall test opening on the north side of the third floor. All other test openings previously drilled on the same floor were sealed with a poly sheet, about 1.5 m (5 ft) square, to the plaster finish. When the air pump was turned on, it was noted the poly sheet covering the test openings on the opposite side of the building inflated slightly to the indoor side of the floor, an indication the cavity was exhibiting pressurization even with all manner of unknown leakage paths through the exterior wall cavities.
Architectural interventions
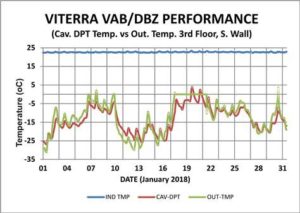
In order to prepare the building envelope for VAB/DBZ, several architectural modifications were undertaken to seal the cladding and exterior wall indoor finishes to better contain the cavity pressure including:
- the restoration and repointing of the exterior terra cotta mortar joints and cladding stones;
- two vertical compartment seals through the exterior wall at the junctions of the main building with the adjacent tower;
- vertical air seals between the exterior wall and elevator shaft to minimize the loss of cavity pressure into the shaft;
- air seals between the exterior wall rough openings and the new window frames;
- foundation to exterior wall connection and the exterior wall to roof/attic slab were both sealed for the purposes of pressure containment; and
- indoor foil faced gypsum board with narrow cavity between gypsum board and existing plaster finish was installed to seal the exterior wall on the indoor side (the foil faced gypsum provides a small insulation value, [radiant cavity] to raise the indoor surface temperature in winter for occupancy comfort).
Mechanical pressurization system
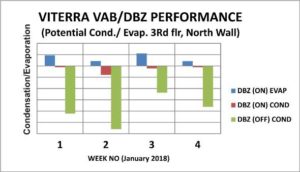
Based on the previous determination of exterior wall areas an initial estimate for the supply air volume was determined to be about 3540 L/s (7500 cfm). The fan head pressurization of the VAB/DBZ ventilation system was limited to 250 Pa (1 in. H2O). Figure 2 (page 38) illustrates the VAB/DBZ duct system from the outdoor fresh air intake to the connections in the exterior walls in the horizontal sectional view. The DBZ mechanical system comprises a fresh air inlet with rain penetration control, fan as air handling unit (AHU), gas heater for the outdoor supply air, and all associated ductwork (coloured grey and pink). The ductwork is fully insulated from the air inlet to the duct heater. The ductwork downstream of the heater to the duct connections did not require insulation. Since the VAB/DBZ supply air is heated well above the indoor winter DPT, the risk of downstream ductwork surface condensation is minimal. This limited the indoor RH to not exceed 50 per cent during winter season.
The final DBZ mechanical system specifications for the Viterra Building and makeup air unit data are:
- maximum supply airflow – 3540 L/s (7500 cfm);
- maximum fan head pressure – 250 Pa;
- heating capacity – 188 kW (649,000 Btuh);
- a bypass to allow adjustment of the unit volumetric flow rate during commissioning of the air-side system;
- pressure independent variable air volume (VAV) boxes in order to control supply air to each floor and wall cavity pressure tied to a near constant pressure-looped duct main;
- a ‘balancing’ duct to equalize pressures in dual risers where appropriate;
- duct insulation of 76 mm (3 in.) on unheated air (i.e. upstream of the makeup air unit);
- manual duct dampers at exterior wall connections for balancing;
- fire dampers at fire separation penetration; and
- system controls, including monitoring sensors and data collection devices.