Virtual air barrier and dynamic buffer zone for a heritage building envelope
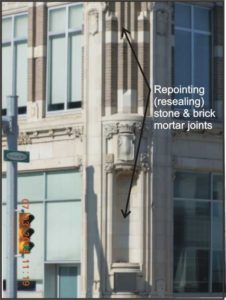
The restoration as well as the design of the architectural requirements of the VAB/DBZ portion of the project was undertaken by this article’s co-author Roger Mitchell, SAA (Ret.), FRAIC, of Regina. The design of the VAB/DBZ mechanical system and controls was provided by Robert (Bob) J. England, P.Eng., of R. J. England Consulting (mechanical engineer), also of Regina and a co-author of this article. Consultation for the application and performance evaluation of a VAB/DBZ for the Viterra building was provided by Rick Quirouette, B.Arch., of Quirouette Building Specialists of Ottawa, Ont. The construction of the cladding and wall restoration, the indoor fit-up, and the VAB/DBZ project was undertaken by PCL Construction as construction manager supported by Brxton Masonry and Tierdon Glass.
The VAB/DBZ concept
The VAB/DBZ is an advanced architectural and mechanical system technology. It has evolved over the past 30 years, from an exterior wall or roof cavity ventilation approach to the more efficient and less costly cavity air pressure control concept. It provides effective and efficient protection to the building façades for an indefinite period of years if operated as prescribed. It is well-suited to masonry heritage buildings as well as other types of structures requiring higher than normal indoor humidity conditions. It has been applied to buildings in Montréal, Ottawa, Toronto, Edmonton, and, most recently, in Regina.
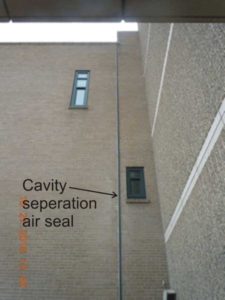
The concept of the VAB/DBZ technology is to lightly pressurize the interior (or cavity) of the exterior wall (or roof cavity) of a building slightly above the indoor pressure at all times during late fall, winter, and early spring seasons. The exterior wall and cladding cavity pressure is provided by a mechanical pressurization (ventilation) system. When operating, the VAB/DBZ system controls an exterior wall (or roof) cavity pressure even as the indoor levels rise or fall with stack effect, wind pressure, mechanical ventilation, and barometric pressure. In this way, the moist indoor air cannot and does not leak (exfiltration) into the cavities of the exterior wall (or roof) to cause a buildup of condensation in winter.
A VAB/DBZ system uses outdoor air for its pressurization (ventilation) air supply through a rooftop unit. The supply air must be taken from the outdoors because the dewpoint temperature (DPT) of the outdoor air is almost always below the temperature of any surface within the exterior wall components. Thus, the outdoor air cannot contribute to condensation anywhere within the exterior wall as the wall cavity surface temperatures are above the outdoor DPT.
To reiterate and emphasize, the VAB/DBZ system’s supply air must never be drawn from the interior of the building, such as a mechanical room, elevator shaft, or stairwell. This is to ensure the new air introduced into a wall (or roof) cavity is dryer than the air in the building and wall cavities of the VAB/DBZ. There are times when the outdoor temperature is cold, but not below freezing (e.g. during rain). When this happens, the VAB/DBZ supply air would exhibit a slightly higher than wall cavity DPT. However, this condition is short-lived and does not contribute significant condensation moisture to a wall cavity.
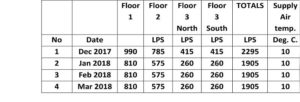
The VAB/DBZ supply air is pumped directly into the exterior wall cavities at specified intervals around the floor perimeter from supply ducts on individual floors. There is no return air in this approach, thus eliminating a significant portion of the assembly cost, not to mention a more effective and efficient system operation.
Viterra building envelope assessment
Prior to implementing a VAB/DBZ on the Viterra building, a review of the architectural conditions of the building envelope was undertaken. To estimate the initial VAB/DBZ supply air requirements, an empirical rule is used. It was determined from previous projects. A heritage masonry wall requires between 12 L/s/10 m2 (25 cfm/100 sf) and 19 L/s/m2 (40 cfm/100 sf) of exterior wall including windows. The project team’s first task was to determine the areas of exterior wall to be serviced with a VAB/DBZ.
A set of architectural documents were found
from the original construction. They provided general information on elevations, building sections, and floor plans for all three floors including an attic-type mechanical room. The building has a 2114-m2 (22,750-sf) floor footprint with high ceilings. Since few detail drawings of the exterior walls were available, test openings were undertaken to determine its composition and cavity conditions. The tests revealed the following:
- terra cotta exterior is 102 or 203 mm (4 or 8 in.) deep;
- exterior wall cavity has masonry rubble infill;
- narrow alignment cavity;
- precast spandrel beam at the ceiling and floor level of each storey;
- two layers of terra cotta masonry on the indoor side below the spandrel; and
- plaster and lath indoor finish (Figure 1).