Vapour diffusion and condensation control for commercial wall assemblies
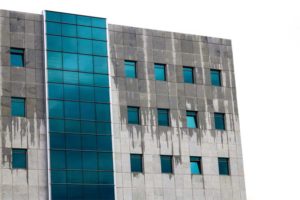
by Alejandra Nieto
As building codes change in North America in response to the call for greater energy efficiency, builders, architects, engineers, and specifiers continue to see a move toward tighter building envelopes requiring increased insulation levels. While this comes with many benefits from the perspective of thermal performance, reduced energy consumption, and lower environmental impact, it also poses a number of challenges. Most consequential is the need to effectively control moisture. Yet, with a multitude of options for commercial insulation and wall assembly design, the guidance offered by energy and building codes can range from non-existent to confusing despite the fact moisture control remains a primary concern impacting occupant comfort, safety, and durability (or potential failure) of the wall assembly and/or its components. So, what is a best-in-class insulated commercial wall assembly? The truth is, it depends on a wide array of variables such as climate zone, insulation type, vapour permeability, and membrane selection. Yet, it is these exact variables that provide the answers to a more functional and effective wall system, its components, and the placement of each within the wall assembly.
Vapour diffusion
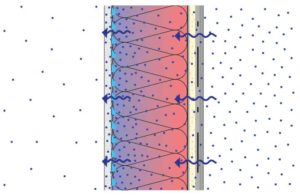
An important consideration is vapour diffusion. When vapour diffuses, it moves from the warm to cold side because warm air can hold more water than cold air. Overall, the direction of the vapour drive has important ramifications to the placement of materials within a wall assembly. Improper placement of materials can affect a wall’s drying potential and can lead to condensation on colder surfaces, damaged materials, and fungal growth. To control vapour diffusion, vapour retarding materials are used. While all materials can act as vapour retarders to some degree, vapour retarders and vapour barriers are classified by their permeance or ability to let vapour pass through, measured in perms. Class 1 materials are the most impermeable, allowing the least amount of vapour to travel through the wall, while each subsequent class of vapour retarding materials is increasingly permeable, allowing for more vapour movement. Overall, the control of vapour diffusion must be a balance. The goal should be to minimize or manage wetting sources, while maximizing the drying potential, should moisture be introduced during construction or the materials get somehow wetted in service. This is particularly important, because while vapour diffusion is generally thought of as a negative process, in fact it is the only process through which the interior of most wall assemblies is able to dry in service. This is especially important with today’s highly insulated wall assemblies, as more insulation means less heat energy is available to dry moisture from within the wall assembly. Special consideration must also be given to placement of the vapour control layer, which will be highly dependent on climate and seasonal vapour drive where a given building is being constructed.