Using SPF insulation in zero-net energy buildings
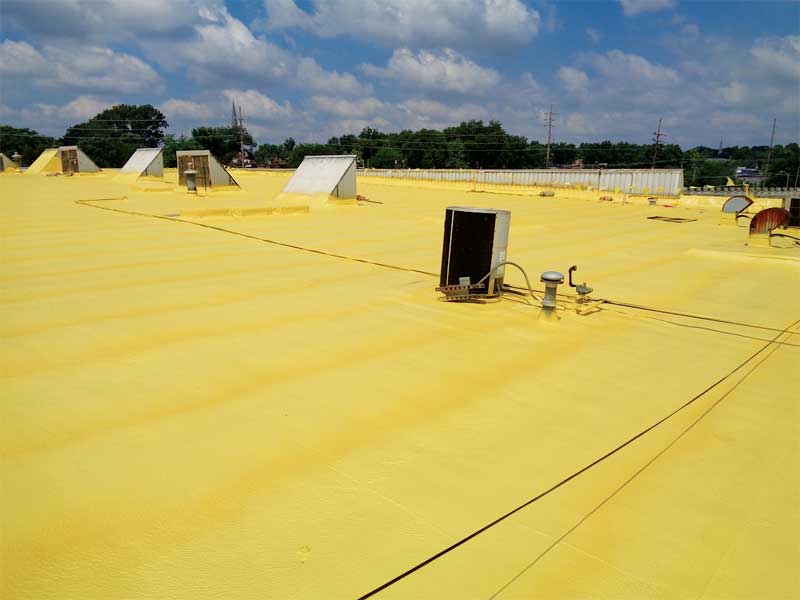
Equipment care and proper material storage and temperatures
Professional SPF installation equipment must be cared for properly to ensure safety, effective installation, and the optimal performance of SPF. This essential care includes regular inspection, cleaning, and repair. Additionally, proper storage and maintenance of the equipment is critical to ensuring it works properly and effectively.
Contractors must have a supply of spare parts in each vehicle to minimize downtime should equipment failure occur during foam insulation installation. A spare parts inventory should include spray-gun parts (or a backup spray gun), extra hoses, second set of drum pumps, and key wear-parts for the proportioner, compressor, and generator.
Manufacturers provide suggested temperature ranges for the storage of sprayfoam chemicals, and these guidelines must be adhered to as a means to maximize their shelf life and to ensure they may be applied correctly and without difficulty. During installation, proportioner controls should be set to the manufacturer-recommended temperatures and pressures to produce ideal SPF. Properly stored sprayfoam chemicals typically have a six-month shelf life.
Manufacturers will have mandatory labelling requirements for their drums as referenced in CAN/ULC S705.1, Standard for Thermal Insulation: Spray-applied Rigid Polyurethane Foam, Medium-density−Material Specification. Drum labels will provide lot codes and expiration dates on the B-side materials. These details are recorded in the daily worksheet or record each contractor must produce in compliance with CAN/ULC S705.2 installation standards.
SPF in roofing
In roofing, SPF acts as a water barrier, air barrier, and thermal insulator. As a lightweight material, sprayfoam can be particularly suitable when:
- the roof deck is an unusual configuration or shape (e.g. domes);
- a slope application is needed to provide controlled drainage;
- the roof substrate includes many penetrations
(e.g. photovoltaic [PV] panel supports); - the roof is being applied to a structure located in a region of extreme weather cycling; and
- the existing roof covering is to be maintained.
Sprayfoam’s positive qualities in roofing applications range from versatility to a lengthy lifespan and durability. The physical properties of the material change little over time, leading to a lengthy life with regular care and maintenance. It also strengthens the building envelope in many ways.
SPF roofs boast a compressive strength of 275 to 415 kPa (40 to 60 psi), requiring no adhesives or fasteners. Adhesion is uniform and very high, which is a key factor in places where severe weather such as hail, wind, and rain are problematic. With extreme weather and storms often the toughest test for any roof, they are thus significant factors in the selection of a durable and resilient roofing system. SPF ranks high among the competition for roofing solutions when it comes to weather and storm resistance.
When applied to the interior side of a roof, closed-cell SPF can increase a building’s resistance to wind uplift during severe storms. Where SPF is applied to built-up roofing systems (BURs) and metal substrates, it increases resistance to wind uplift even further. A study conducted by the University of Florida in 2007 found applying closed-cell sprayfoam under a roof deck provides up to three times the resistance to wind uplift for wood roof sheathing panels when compared to a conventionally fastened roof. (See “Wind Uplift Behavior of Wood Roof Sheathing Panels Retrofitted with Spray-applied Polyurethane Foam,” by this article’s co-author, Duncan, and Jinhuang Wu, PhD, prepared for the University of Florida in 2007.)
When the U.S. National Institute of Standards and Technology (NIST) examined roofs following 2005’s Hurricane Katrina, it found buildings with sprayfoam roofs performed rather well without blow-off of the SPF or damage to flashings. The 2006 report, “Performance of Physical Structures in Hurricane Katrina and Hurricane Rita: A Reconnaissance Report,” found only one of the examined SPF roofs incurred notable damage, and that damage was confined to only one per cent of the total roof system. The report concluded SPF kept the roofs intact, prevented moisture from entering the buildings, and protected the structures from hail and debris.
Short warm seasons and high precipitation can limit the opportunities to install SPF roofing systems in Canada compared to the United States. Standards are currently in development for 3-lb, or greater, closed-cell and higher-density foams used for roofing.
When installing SPF roofing, the following must be considered:
1. All substrates must be clean, dry, and free of excessive debris prior to installation.
2. Any liquid water present on the roof surface can result in blisters occurring between the foam and the deck. Thus, the substrate must be examined to ensure for dryness.
3. Sprayfoam may also generate fine airborne particles, which can inadvertently deposit themselves onto finished surfaces such as window glass, and nearby automobiles. To minimize the dispersion of these particles, tents and screen systems may be needed during installation.
4. Generally speaking, SPF is not applied to the roof when wind speeds exceed 9 km/h (15 mph) or if the temperature falls below 0 C (32 F).