Using SPF insulation in zero-net energy buildings
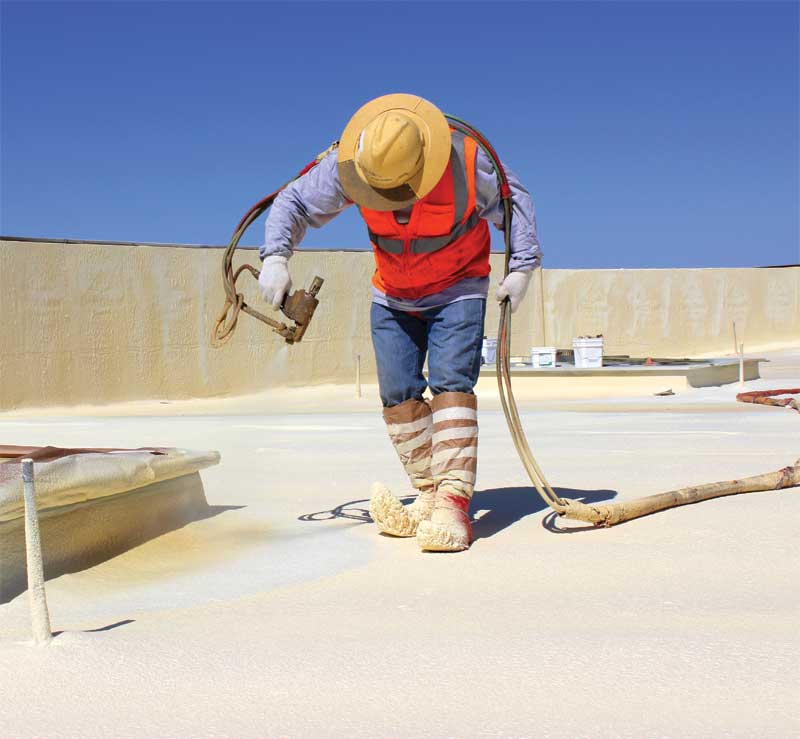
Proper sprayfoam installation
A wide range of polyurethane foam products is available in various densities and open-cell content, each exhibiting different performance characteristics such as moisture resistance, R-value, and compressive strength. Foam selection also affects installation characteristics, including the maximum lift thickness per pass and allowable substrate temperatures that in turn affect foam coverage.
SPF is created by mixing equal volumes of two liquid components—the ‘A-side’ (which contains polymeric isocyanates [pMDI]), while the ‘B-side’ (proprietary blends of polyols, blowing agents, catalysts, fire retardants, and surfactants). Since SPF is essentially manufactured onsite during installation, installers must follow specific guidelines, techniques, and measures to maximize the product’s lifetime performance and to ensure safety for both themselves and the eventual users of the space. Such measures are outlined in published, code-referenced standards like CAN/ULC S705.2, Standard for Thermal Insulation: Spray-applied Rigid Polyurethane Foam, Medium-density−Application.
It is imperative to protect against contact with chemical vapours and aerosols from SPF, which are developed during and shortly after application. Appropriate protective measures minimize the risks associated with exposure through inhalation, skin, and eye contact and include spray-zone containment, coupled with adequate ventilation during installation, safety training for all those involved, personal protective equipment (PPE) for the full duration of the install, and a medical surveillance program for field crews.
PPE for chemical protection includes a chemical-resistant full bodysuit and headsock to cover skin, along with chemically resistant gloves and eye protection. Respiratory protection for interior insulation requires use of a supplied air respirator (SAR). In accordance with the Canadian Centre for Occupational Health and Safety (CCOHS), all insulation contractors, like any other construction trade, must employ proper fall protection as well as safety programs that include using ladders, scaffolding, and working in confined spaces like attics and crawlspaces.
Additionally, overspray from SPF insulation applications must be controlled to prevent it from getting on unintended surfaces. Finished surfaces, as well as window glass, must be properly covered and masked to prevent damage from overspray.
Substrate and environmental evaluation
SPF adheres to various construction materials including metal, wood, and concrete very well. However, licensed installers must ensure surfaces are completely dry, and free of oils, grease, dirt, and debris as outlined in the code-referenced application standards.
It is also important to assess weather when applying sprayfoam. While the product may be applied in various climatic conditions, it is important to follow the manufacturer’s recommendations and its Canadian Construction Materials Centre (CCMC) Evaluation Listing installation limitations. Sprayfoam and related coatings should not be installed when there is ice, frost, surface moisture, or visible dampness present on the surface to be covered. Surface moisture can react with SPF chemicals resulting in poor-quality foam and/or lack of adhesion.
Adhesion is a key field test of the SPF system and the licensed installer is required to conduct a series of field tests for adhesion and density on every project, every lot change of chemical, and every eight hours. These tests are conducted using field test kits installing contractors must have on their spray rigs. The results of these tests must be recorded on daily worksheets and submitted to the third-party certification organization for review and retention.
In some SPF insulation installations, priming of the substrate surface may be required, especially when applying foam to large metal surfaces. Primers can greatly enhance adhesion between the SPF and existing substrates. Primers can help seal porous substrates and improve adhesion to metal substrates.
Installation of protective coatings and coverings
If exposed to sunlight or certain artificial light, SPF should have a covering or coating to protect it from ultraviolet (UV) light degradation. Additionally, sprayfoam products require thermal barriers—(fire- protective) coatings of coverings—in most instalations, as they are considered combustible construction materials.
Typically thermal barriers tend to be 12.7-mm (½-in.) gypsum and 19-mm (¾-in.) plywood. Recently, CCMC has provided guidance on the acceptable use of intumescent paints as an alternative solution providing thermal barriers. Consultation with authorities having jurisdiction (AHJs) should provide acceptable code-compliant or alternative solutions to designers for the creation of correct stamped drawings and specifications.