Using ground-penetrating radar with concrete
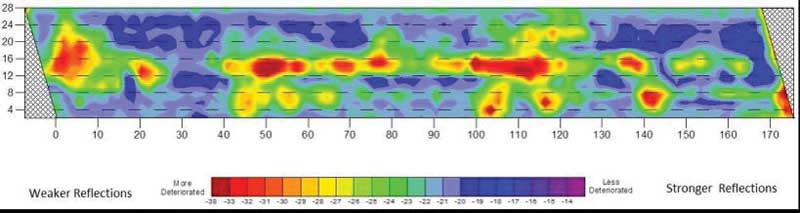
Bridge deck condition assessment
The extent of deterioration in the bridge decks is routinely investigated using GPR. The result is a map of rebar reflection amplitudes, from which areas of differing degrees of deterioration are delineated.
As shown in Figure 1, the areas with the lowest rebar reflection amplitudes (yellows and reds) correspond to a portion of the bridge deck containing the most distress in terms of concrete deterioration and/or rebar corrosion. ASTM D6087, Standard Test Method for Evaluating Asphalt-covered Concrete Bridge Decks Using Ground-penetrating Radar, is used to assess the range of reflection amplitudes corresponding to expected bridge maintenance. Assessment of the maintenance requirements indicated by the GPR data is augmented by visual inspection and other accessory condition information, such as previous maintenance records.
Bridge inspection techniques and equipment have come a long way, and the development of improved ground-penetrating radar technology has enhanced inspection results substantially. GPR is gradually becoming a mainstream application in the toolbox of methods for evaluating bridge conditions, but it also has further uses as explored in the rest of this article.
Cutting applications
Non-destructive testing methods are greatly preferred for locating buried metal targets or electrical conduits in existing structures, including not only bridges, but also buildings. If embedded or buried obstructions are hit during concrete cutting, the results can be disastrous—from project delays and cost overruns to worker safety hazards. Cutting rebar that is strengthening the slab steel beam structure could mean damage, or even cause the structure to fall. Cutting electrical conduit, on the other hand, can result in a job shutdown or lead to serious injuries.
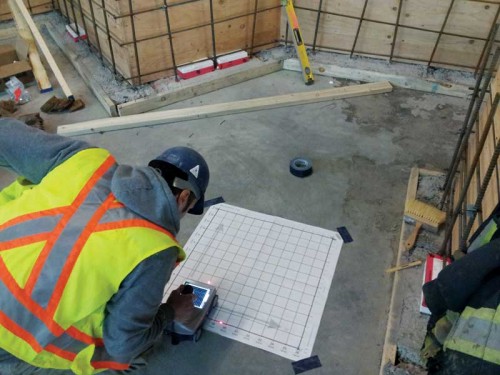
Take the example offered by Matt Aston of Ground Penetrating Radar Systems (GPRS), located in Toledo, Ohio, which uses GPR technology to provide critical information on utilities, materials, and other obstructions in or under structures. At what should have been a simple job to cap a hospital sanitary line, a concrete cutting firm used a jackhammer to break through a wall. Unfortunately, on the other side of the wall was an electrical closet. The 0.4-m2 (4-sf) area contained 20 to 25 electrical conduits running through it, which were all broken or destroyed. Power had to be shut down to the kitchen for the 400-bed hospital, with catering arrangements made for two or three meals before power was restored.
“The hospital president called me to a meeting to ask what it would have cost to scan the area,” says Aston. “I told him it would have cost in the range of $600 to $700 [U.S.]. Instead, their spending for electrical repairs and food was around $200,000.”
For many decades, X-ray technology was the predominant non-destructive technique for locating and identifying embedded targets. While this method is still useful, concrete scanning using GPR has overtaken X-ray technology for trying to locate rebar, post-tension cables, or conduits prior to concrete cutting or any other destructive procedures.
Unlike radioactive X-ray technology, concrete imaging equipment can locate targets and their depths safely, without the need to vacate the jobsite. Additionally, whereas X-ray technology is very expensive to purchase, most GPR equipment is affordable and much easier to use.
Tips and best practices
While GPR is not perfect (e.g. it does not penetrate recently poured [i.e. days-old] concrete as well as older material), its use helps contractors know what hazards are buried in or below concrete slabs or underground and the potential for enormous cost and inconvenience if any services to the building or operations are interrupted.
For those looking to purchase their own GPR equipment or seeking to partner with a concrete radar firm, there are a few general best practices. GPR equipment for scanning concrete takes a beating, so it must be durable and rugged. It should also be easy to use, with an intuitive and bright display and high image resolution. For example, with high-performance GPR data-acquisition systems and 400-MHz antennas, one can locate underground utilities and obstructions to a maximum of 2.4 m (8 ft) in depth beneath the surface, and then provide results immediately.
A range of proprietary assemblies can offer a simple user interface, plug-and-play GPS integration, and WiFi-enabled data transfer capabilities, with various types of antennas. Some include lightweight hand-held devices that can locate rebar, conduits, post-tension cables, and voids up to depths of 508 mm (20 in.), while also determining concrete slab thickness in real-time.
There is growing support for the industry-wide training/certification program being developed by the American Society for Nondestructive Testing (ASNT) and the Concrete Sawing and Drilling Association (CSDA) over the past few years. The program will codify the practices for cutting contractors to provide owners, architects, engineers, general contractors, and government officials with a valuable pre-qualification tool that acknowledges sound business practices.