Using brick veneer and metal studs for strong walls
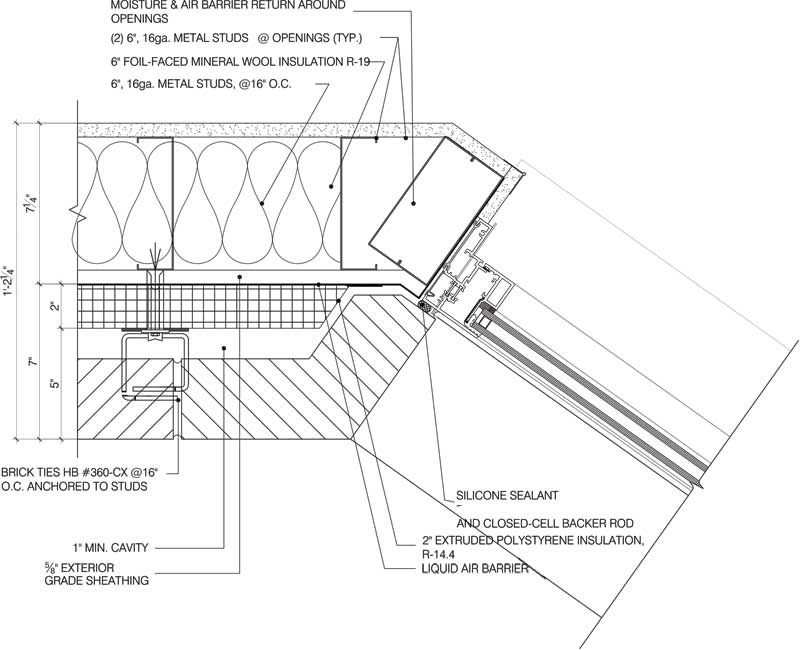
Image courtesy Centria
At the construction site
During this author’s various inspections of the exterior wall installations, the drywall or masonry contractor installed the insulation board. Unfortunately, sloppy installation of the XPS insulation boards occurred in many of these cases. As a result, the R-value suffered.
Contractors often cut insulation board using a hand-saw, which sometimes leaves gaps up to 19 mm (¾ in.) between the uneven edges of the boards. Some of the boards had 135-degree corners, which was a problem if it met up with other boards with 90-degree, square corners. When the boards met in this fashion, a triangular-shaped gap in the continuous insulation was left. In another instance, at narrow window or door jambs of 102 mm (4 in.) with double or triple studs, the insulation was sometimes not installed at all (Figure 1).
When a designer calls for a liquid air barrier to be installed over the exterior gypsum board sheathing (that is, behind the 51-mm [2-in.] XPS insulation board) the elastomeric coat has low permeability, and will also act as a vapour barrier. When foil-faced mineral wool insulation with R-19 is to be installed within the metal studs, the foil located at the inside face of the wall will act as the second vapour barrier. The dewpoint in this wall system will be located between two vapour barriers, which should be verified by condensation analysis for both summer and winter conditions. Only one vapour barrier should be installed at the winter warm side of this wall (for the northern climate zones).
In many cases, the insulation board was cut out to install the masonry ties. However, after the ties were installed, these spots were left with a 51-mm (2-in.) square opening.
All these insulation deficiencies would jeopardize the continuous R-value of the wall system. Far too frequently, insulation boards are installed with insufficiently tight joints. To achieve these tight joints, contractors should cut XPS insulation boards with a table circular saw.
Insulated composite backup panels
Innovations for the BV/MS backup exterior wall can be derived from the insulated composite backup panel (ICBP) system. The ICBP has panels with two face shells made out of galvanized steel with the polyisocyanurate (polyiso) insulation between. Panels are available with a 51 mm (2 in.) thickness with R-14, and a 76 mm (3 in.) thickness with R-21. Panels are 813 mm (32 in.) wide with tongue and groove longitudinal (horizontal) joints, which has factory installed gaskets. Thus, when one panel is installed over another, the longitudinal joints between the panels automatically seals, ensuring a foolproof installation.
Generally, panels are 3.7 m (12 ft) long, although 6-m (20-ft) panels are available. In these products, only one joint between the panel end and the steel stud should be sealed at the construction site with a butyl sealant. L-shaped masonry ties should be installed into the horizontal joints between 812-mm (32-in.) wide panels. The tie vertical leg is installed over the tongue part of the panel and attached to the stud with the screw, which attaches the panel to the steel stud. Masonry ties should be installed at 406 mm (16 in.) on center (oc) vertically, and additional L-shaped masonry ties, with shorter horizontal legs, should be installed in the middle of the panel width with tape to seal the screw penetration through the panel.
As an exterior wall metal panel, ICBPs are installed as a backup with BV/MS, but lack an esthetic finish. Since the face of the ICBP system with sealed seams is not sensitive to any moisture, the air space between the brick veneer and the ICBP could be reduced to 25 mm (1 in.). Also, the ICBP system is suitable for rainscreen wall system design.
Single-step installation of an ICBP system could substitute the three steps of installation of exterior gypsum board sheathing, vapour/air barriers, and insulation board with considerable labour savings. During a large-scale project, four to six weeks could be cut from the construction schedule with a substantial cost savings to the owner.
One of the first large-scale projects with an ICBP system was built south of Boston. The four-storey, 20,438-m2 (220,000-sf) office building’s exterior walls were enclosed by the panels in the winter within 10 working days. BV/MS would take three times as long because the contractor needs scaffolding to install it. The brick veneer was installed with warmer weather in April.
Specifying the insulated composite backup panel system simplifies the backup wall installation of brick veneer/metal stud assembly and eliminates potential problems. The system could be installed in the winter to enclose the building envelope. It provides cost savings for building developers, specifically for large-scale projects.
Michael Gurevich is a masonry consultant at the New York City Brickwork Design Center (NYCBDC), which conducts free seminars on a variety of topics—such as barick veneer metal stud backup exterior walls—for CSI and American Institute of Architects (AIA) chapters. He has 30 years of experience working with exterior masonry walls. Gurevich holds a master’s degree in structural engineering from Belarussian State Polytech University in Minsk. He can be contacted via e-mail at nycbdc@aol.com.