Using acetylated wood for structural applications
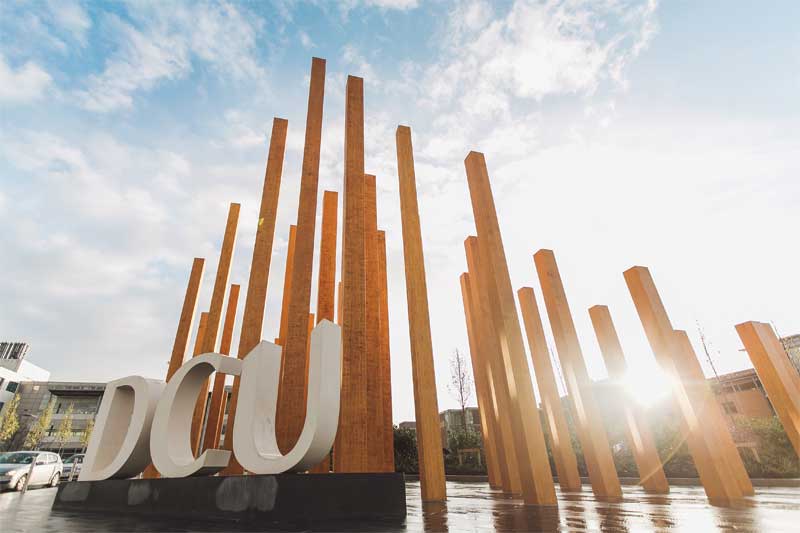
By Steve Morrison
Most architects and engineers have historically defaulted to steel and concrete when designing tall buildings, bridges, and other towering structures. Over the past few years, however, commercial designers have begun to reconsider the suitability of wood as a structural building material.
Compared to concrete and steel, wood is less expensive, generally easier to work with, and more sustainable. It is made from carbon dioxide (CO2) captured from the atmosphere by trees and stored in wood, where the carbon will remain locked for the entire lifespan of the material.
As urban centres become denser—and as demand for residential and commercial skyscrapers surges—use of structural wood, particularly in tall buildings, could make a marked difference in the air quality of those cities and in the health of the environment in general.
One of the primary limitations on using wood for structural applications is its vulnerability to fungal attack. Preservatives resolve some of this concern, but raise another: the lingering effects of toxins (such as those released by pressure-treated wood) on indoor air quality (IAQ). The few species of wood that naturally resist fungal attack tend to be in limited supply, fairly short-lived, and difficult to glue. This is one of the reasons architects have shied away from specifying wood for structural use on the exteriors of edifices located in damp climates.
Since the introduction of acetylated wood to the market nearly a decade ago, however, using wood for tall structures has become an increasingly attractive alternative to using concrete and steel. In 2008 and 2010, acetylated wood replaced traditional construction materials on two structurally demanding, heavy-traffic bridges in the Netherlands. Since then, structural beams made from acetylated wood have also replaced concrete foundations in a house in Scotland. The modified wood also stood in for conventional timber for the columns of a veranda at a sustainable, five-storey care complex in Amsterdam, the posts of a prominent, 16-m (52.5-ft) architectural sculpture at the entrance of Dublin City University (DCU), and the structural components of several other architectural structures around the world.
Acetylation’s advantages
A process developed more than 80 years ago, acetylation modifies the wood at a molecular level to alter its reaction with water. This permanently alters wood’s propensity to absorb and release water—the quality that makes it swell and shrink. Taking the place of those water-absorbing free hydroxyls are stable acetyl groups that do not bond with water. Wood naturally contains acetyl molecules; the nontoxic acetylation process simply increases their levels so the wood no longer responds as usual to moisture. This reduces its tendency to shrink and swell by more than 70 per cent.
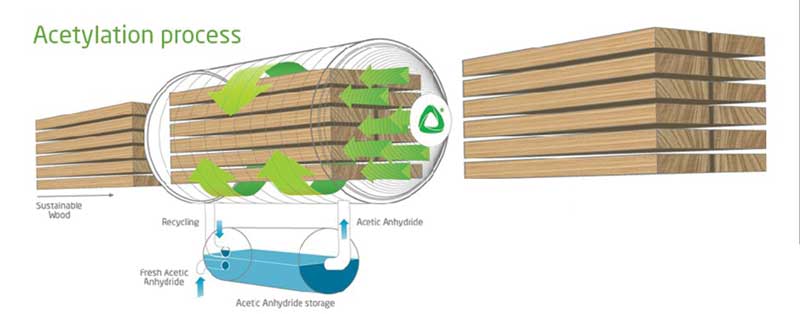
The process also renders the wood inedible to insects and parasites like fungi and far more resistant to rot and decay than unmodified wood. The result is a durable, dimensionally stable product with the natural beauty of wood.
Since this modification permeates the wood, the full cross-section of members up to 75 mm (3 in.) thick remains moisture- and fungus-resistant, even when the core is exposed during cutting and machining—unlike treated conventional wood.
The dimensional stability provided by acetylated wood’s resistance to shrinking and swelling is one of its primary advantages. Changes in the moisture content of the surrounding environment can cause large structural members made from unmodified wood to split—especially at the point where they are joined by steel connection plates. Acetylated wood is less likely to do so. This modified wood also does not suffer from moisture-induced pits and fissures, which can trap water and increase the moisture content of the wood, creating an appealing breeding ground for fungi.
In one 16-year-long test, large stakes—some made of acetylated wood and others of unmodified wood—were planted along the edge of a Holland canal. Over the course of those years, the acetylated wood did not decay, but the untreated wood was destroyed. Other tests in the United States, Australia, and Japan proved the modified wood was up to 20 times more resistant to termite damage. These qualities render acetylated wood virtually free of the need for preventative maintenance, unless a coating is applied for esthetic reasons. In that case, the finish may need periodic reapplication.