University Builds Up with Timber Addition: The first Canadian law school in three decades is built in Kamloops, B.C.
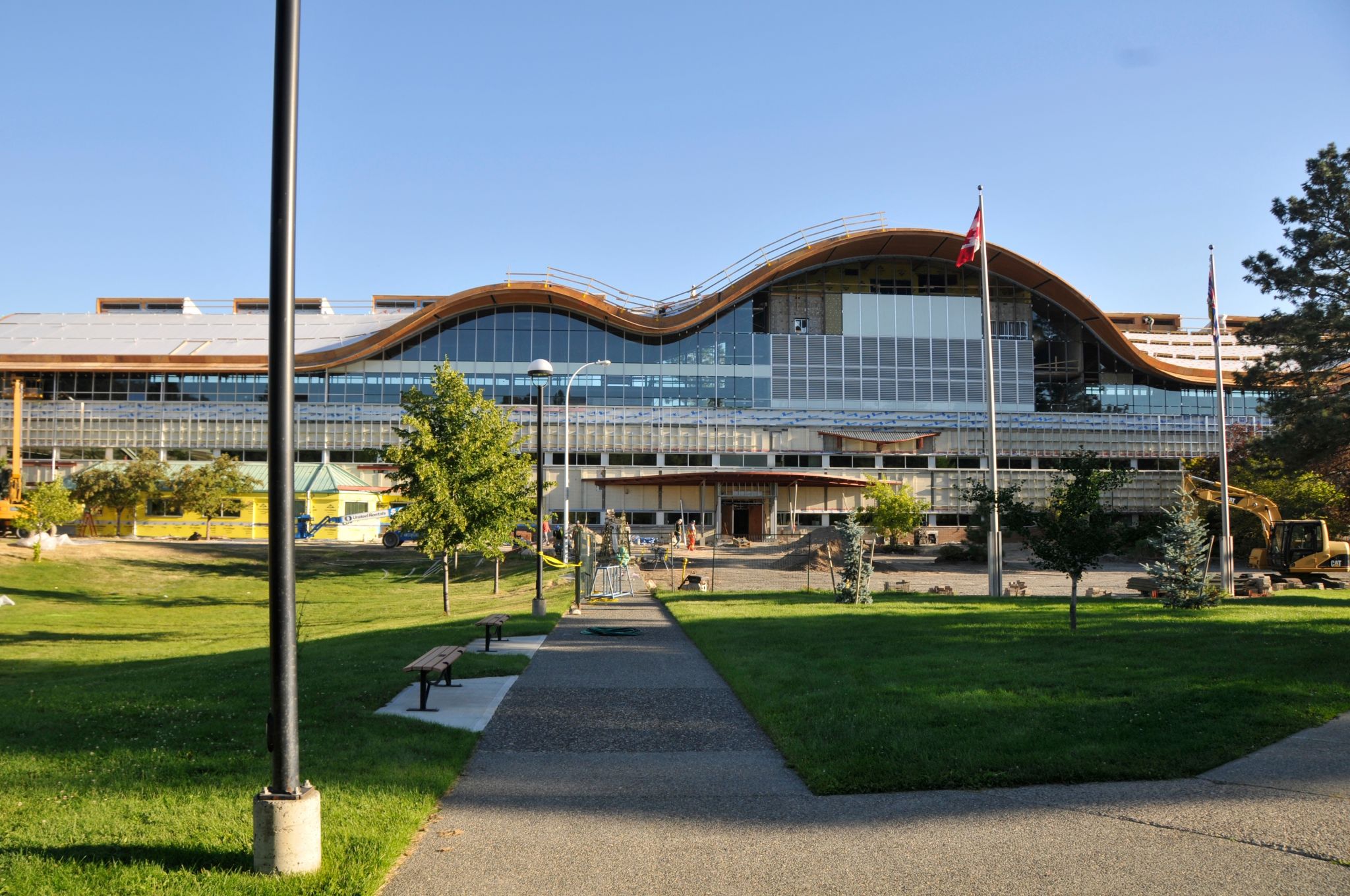
By Michael Leckman, DEC.Arch., B.Arch., MRAIC
Last year, Thompson Rivers University (TRU) in Kamloops, B.C., opened the country’s first new law school in more than three decades. As a result, the push was on to move the new cohort of lawyers out of a temporary location and into a permanent home. The growing university had a site in mind—the new law school location would be constructed atop Old Main—an existing two-storey, 122- by 26-m (400- by 84-ft) concrete structure built in 1970, housing classrooms and offices.
The design team—led by Diamond Schmitt Architects—took inspiration from Kamloops’ mountainous landscape and planned an undulating roofline echoing the features of twin peaks, Mounts Peter and Paul, which are prominent on the city skyline. The transformation took place over 12 weeks of last year’s summer break and included:
- 3716 m2 (40,000 sf) of program space;
- panoramic vistas from the third- and fourth-floor addition;
- space filled with daylighting and airflow;
- use of local timber materials; and
- roof installation.
Addressing the roof first
The accelerated schedule called for a prefabricated roofing assembly; its tender went out before the rest of the building in December 2011 to get a head start on shop drawings. The team decided to use a 3.5-m (11 1/2-ft) wide prefabricated panel that could be placed directly onto the building’s 3.7-m (12-ft) existing bay system, says Ian Boyle, P.Eng., of structural engineering firm, Fast+Epp.
The initial plan called for steel columns and beams spanning 11 m (36 ft), and wood panel infill. However, the fabricator proposed a wood system using glued-laminated timber (glulam) beams to save time and money. This introduced another matter—putting a timber structure on the third and fourth floors of an existing building would not meet building code for this structure’s height and assembly occupancy. This required a negotiation with the City of Kamloops.
Code consultant James Ware (LMDG Building Code Consultants) notes the 2005 national model codes changed from prescriptive- to objective-based. Before the change, designers would have to develop an equivalent to a requirement based on the prescriptive code, says Ware.
“The objective-based building codes now specifically identify the intent of each code requirement providing designers and authorities common ground from which an alternative solution can be developed, reviewed, and accepted,” he explains.
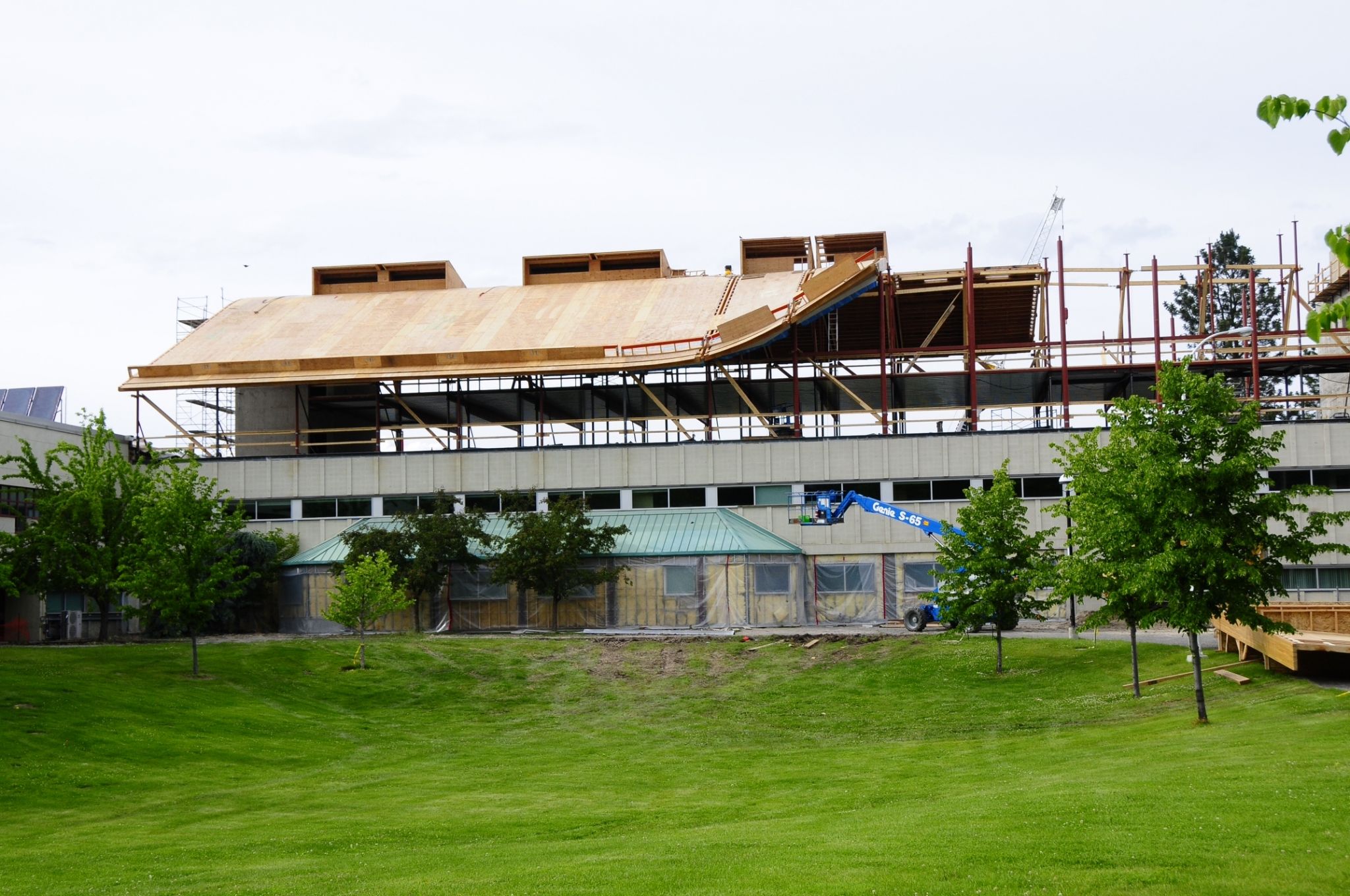
An objective-based building code, and the appropriate fire-risk assessment whose findings are incorporated into the design, enables projects to use various materials and designs such as the use of wood structures otherwise required to be of non-combustible construction.
The law school’s design has a double-height atrium in the centre of the plan with classrooms, a library, and offices and meeting space on either side. The long façade across the north side has two storeys of program area while the south side has one floor of high-ceiling space for reading rooms and a moot court. The interior is largely clad in acoustic wood planks in beech veneer.
Addressing compliance issues
The fire-risk assessment included modelling to determine the expected size of a fire, its flame height, and the potential of a flashover condition within a given fire compartment.
“This analysis identified the hazards associated with the proposed wood structure and roof elements, and provided the parameters with which an alternative solution could be implemented,” says Ware.
The alternative included the use of fire-retardant treated wood for the roof sheathing—19-mm (3/4-in.) fir plywood—and the use of a heavy timber dimensioned roof structure attributed with an inherent fire-resistance rating. Additionally, the solution called for an enhanced system using fast-response sprinklers and an increased density to provide a higher level of performance of the fire-protection system than otherwise required.
In the early stages of the project, other compliance issues were also addressed. The university’s reference scheme, developed to determine project cost and viability, indicated no additional weight was to be added to the existing structure. Extensions were proposed to bear the addition on giant piers on either side of the building. However, this would reduce the amount of light penetration into the existing poorly lit building and compromise light and views on the addition. Boyle, working with the original Old Main drawings, recognized the need to maximize all available space in the existing building, while also creating a structure as lightweight as possible.
The engineers found additional capacity in the structure and footing, and a devised seismic reinforcement strategy calling for replacing 20 per cent of the masonry hallway walls with cast-in-place reinforced concrete. Some existing joists were upgraded to accommodate the law library, where the sheer weight of books was a factor. Working within the existing building footprint and expanding the scheme to one-and-one-half floors from the university’s original scope of a single-floor addition set the stage for a cost-effective and elegant structure to rise above the existing Old Main.
For the prefabricator, this project was not the most elaborate roof assembly it had tackled—a B.C. manufacturer produced the wooden roof for the Richmond Oval skating facility elsewhere in the province.1 Project manager Daniel Kravcak says a typical building requires two or three drawings, but Old Main needed 40. This was a result of the aggressive schedule where designing, making shop drawings, and fabricating were concurrent in order to produce 92 panels consisting of 64 typical and atypical panels and 28 clerestory infill panels. Kravcak estimates the cost savings of the all-wood system to be in excess of $100,000 compared to a steel structure.

The beam, joist, and plywood panels range in weight from 1587 to 2041 kg (3500 to 4500 lb) and the crane was specified for 4309 kg (9500 lb) because of rigging. The 11-m (36-ft) spans ranged in depth from 572 to 229 mm (9 to 22.5 in.), including cantilever extensions. Snow restraint was prebuilt into the panel based on a snow consultant’s study of where accumulation was expected.
Restrictive time and budget constraints meant the roof delivery and installation was carefully strategized. Forty-two truckloads of materials made the journey to the site. The 3.5-m (11 1/2-ft) size of the panels was the maximum transportable size, without having pilot cars on the road. “During one trip, we put a tarp over a panel because it was raining and we were pulled over by the police. We were fined for the extra width and had to use a pilot car to complete the delivery,” says Kravcak.
What’s old is new
The prefabricated panels arrived onsite finished with cedar soffits and pre-treated with a clear fire-retardant coating. With the main steel columns in place, installing the panels was fairly straightforward. The riggers on the ground used four chokes, tilted the panels to the desired pitch, and hoisted them into place. Once fastened in place with steel bolts, the panel-to-panel connection was reinforced with a plywood diaphragm. Kravcak says he learned from the Richmond Oval experience not to prefabricate the waterproofing, but have it installed onsite as this removes liability for leaking and adds a quality control for the application onsite after the delivery.
The roof’s supporting columns were engineered to make it seem to float above the existing structure. The slender 125-mm (5-in.) columns almost disappear behind the mullions within the space. The expressive wave form of the roof not only reflects the mountain peak it faces, but it also conceals Old Main’s large mechanical penthouse. With operable windows and clerestories where warm air naturally gathers, the design allows for natural ventilation strategies in shoulder seasons.
The ceiling system expresses the curves of the roofline where the double-height space of the atrium accentuates the roof’s highpoint. Similarly, the double-height library and reading room capture the most dramatic curves of the interior.
One of the improvements made to Old Main through the renovation was the addition of generous glazing and ample natural lighting. To balance daylighting and solar heat gain, the roof tapers and extends outward 1.8- to 4-m (59- to 13-ft) beyond the glass line. To provide continuous sunshading, even on the very tall glass windows, the overhangs are deeper where the roof curves upwards.
The grey concrete block of the existing Old Main was also in need of refreshing. A lightweight skin was added to the existing cladding, giving a contemporary appearance unifying it as the base to the addition. To reinforce the horizontal lines of the existing windows, a large-scale brick base and horizontal siding cost-effectively conceals the former façade.
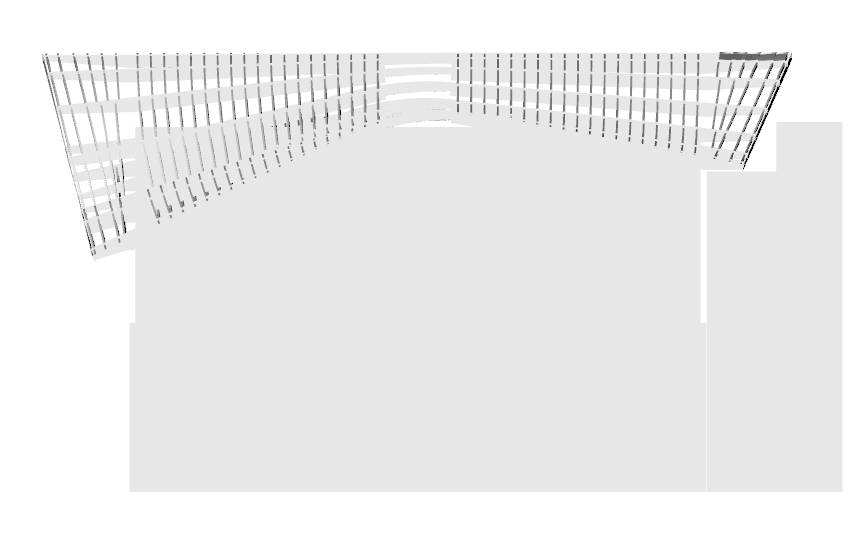
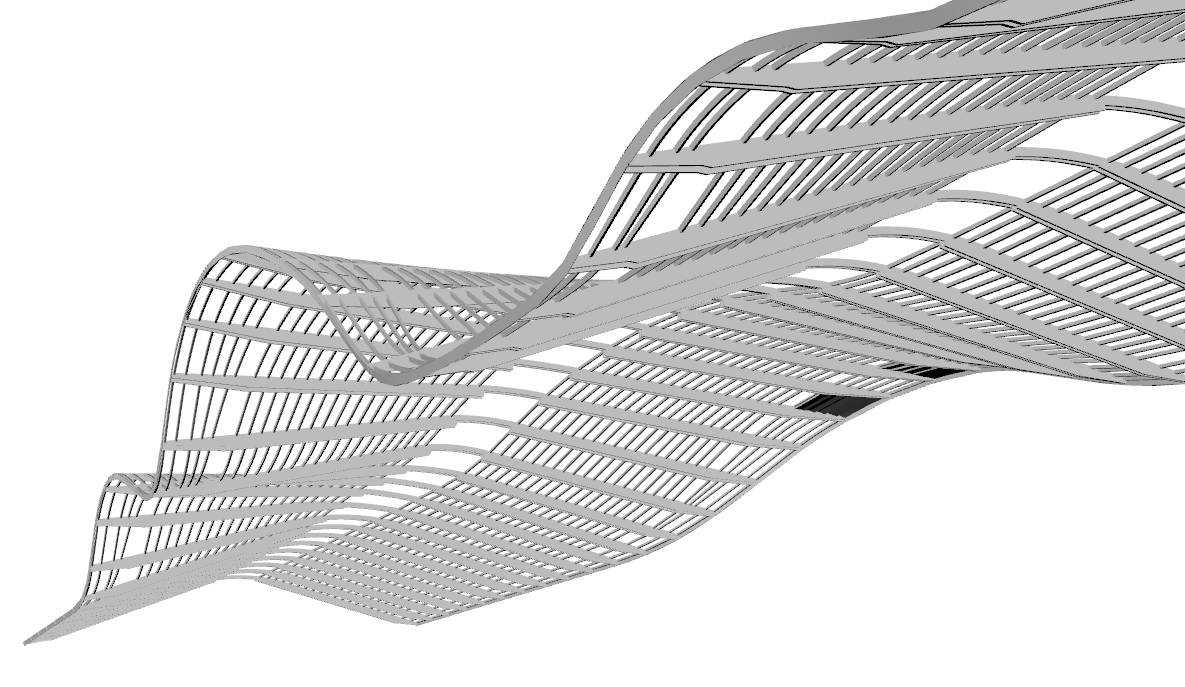
Conclusion
Boyle says with each new timber structure, the material becomes more widespread, making it easier to meet codes. Research projects are underway in Canada and elsewhere to permit timber in taller buildings, but it is still not a common practice.2 The combined efforts of architects, engineers, consultants, and manufacturers will continue to advance the possibilities.
Notes
1 To read more about the Richmond Oval, see the article, “Why Wood Works: Designing the Richmond Olympic Oval” by Jim Taggart, Dip. Arch,. MA, MRAIC, in the November 2009 issue of Construction Canada. (back to top)
2 To read more about the use of timber in tall buildings, see the article, “Mid-rise Makeovers: B.C. Code Changes Encourage Building With Wood” by Jim Taggart, Dip. Arch., MA, MRAIC, in the September 2012 issue of Construction Canada. (back to top)
Michael Leckman studied building science at Vanier College in Montréal, and architecture at the University of Toronto (U of T). He has worked with Diamond Schmitt Architects for more than 20 years. Leckman serves as vice-chair of the City of Toronto Design Review Panel, and acts as a guest critic, lecturer, and mentor at schools of architecture across Ontario. He can be contacted via e-mail at mleckman@dsai.ca.