Understanding waterproofing
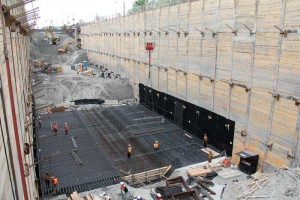
Photos courtesy W. R. Meadows
Waterproofing system placement
It should be determined whether the material is to be applied on the positive or negative side of the wall. Both of these present advantages and disadvantages and require specific systems to perform effectively. It is essential the selected system provide waterproofing, dampproofing, and capillary action, be continuous, and remain durable for the life of the structure.
Positive-side waterproofing systems are applied to the exterior of a structure, sometimes referred to as the ‘wet’ side; this is the predominant choice of waterproofing. Typically, this is the most effective type of waterproofing, as it not only protects the interior of the structure from moisture infiltration, but also blocks entry of moisture into the concrete substrate. Positive-side waterproofing, as a result, can protect against corrosion of reinforcing steel in the concrete or, in climates susceptible to freeze-thaw cycling, deterioration of the concrete. However, one of the limitations of this material is it can be difficult and costly to repair once installed. All types of commercially available waterproofing systems can be applied on the positive side of a wall.
When it comes to negative-side waterproofing, systems are applied to the interior surface, or ‘dry’ side of the concrete. It is essential negative-side waterproofing withstand hydrostatic pressure, but also possess some level of breathability (i.e. water-vapour permeability) to prevent problems due to entrapment of water vapour and capillary pressures in the substrate.
Non-breathable coatings—such as epoxies and urethanes—can delaminate from the surface due to vapour entrapment and movement. Proven systems used in this sort of application consist of crystalline materials or cementitious coatings. An advantage of negative-side waterproofing is these systems are ‘accessible’ when repairs are needed. A disadvantage is water penetrates into the substrate, resulting in potential issues with corrosion or freeze-thaw deterioration, as previously mentioned.
Material options
Once all these considerations have been addressed, it becomes time to review the actual materials and systems available. It is important to consider the type of approach to be followed and to select the specific system based on its performance requirements. Due to the sheer number of waterproofing technologies and systems, the focus of this summary review will be on some of the materials used commonly in design and construction below-grade applications.
Sheet membranes
Sheet membranes can consist of self-adhesive, thermofusible (i.e. torch-on) and certain blindside waterproofing membranes. A major advantage of sheet membranes is factory-controlled thickness, with no onsite fabrication required. Self-adhesive membranes are manufactured with styrene-butadiene-styrene (SBS)-modified bitumen, which provides excellent elongation and recovery characteristics.
Additionally, SBS modification of the membrane prevents ‘drying out’ by facilitating retention of bitumen oils. Application of these materials requires use of a primer before application to consolidate any laitance on the substrate. Application is relatively easy, with no special tools or equipment required.
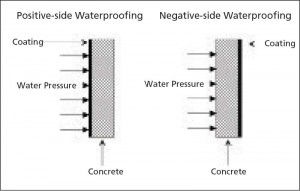
Image courtesy Gemite
Thermofusible membranes are also composed of SBS-modified bitumen, and require a propane torch to melt the backing and soften the bitumen. Use of this system addresses some of the shortcomings of self-adhesive membranes, as the heating allows the membrane to ‘flow’ together, providing continuity and complete coverage of joints, penetrations, and other details. These systems, however, require application by skilled installers and can be quite dangerous to use.
Regardless of the type of sheet membrane, one challenge with their use is ensuring all penetrations, joints, and other details are covered, providing complete continuity of the membrane. In addition, protection of these membranes is required with the use of a protection or drainage board, with rigid insulation also serving this purpose before coverage of the membrane.
Fluid-applied membranes
Various fluid-applied membranes are available, including hot-applied, cold-applied, water-based, and solvent-based materials. Each type comes with its own set of benefits and limitations. One common advantage they all share is they provide a monolithic waterproofing membrane, addressing the joint and detail issues encountered
with sheet membranes.
Hot-applied rubberized asphalt membranes demand specialized equipment and installers; like the thermofusible membranes, they can be dangerous to apply due to the high temperatures required for material application. Cold-applied systems appear to be gaining in popularity for a number of reasons; they are typically sprayable, providing significant reduction in the applied costs of the materials, and they provide the continuity mentioned previously.
Fluid-applied membranes are offered in one- and two-component formulations, and it is essential to ensure the correct material is selected for the job. Some of these can be applied to ‘green’ concrete, while others cannot. Again, these membranes also require the use of a protection layer before being covered.