Understanding Metakaolin: Specifying for high-performance, durable concrete
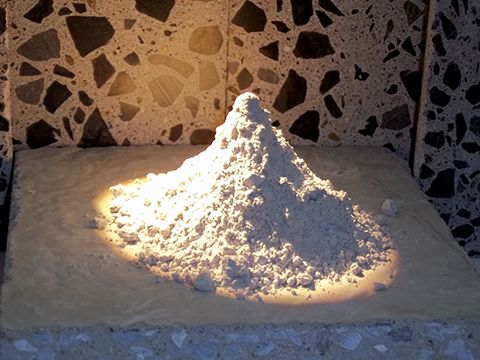
By Jean-Claude Leduc, Asct, and Jacques St-Onge
Already in use in the United States and in many European countries, metakaolin is still little known in Canada. Nevertheless, both international projects and early domestic experiences have shown the additive makes for durable, attractive, and more environmentally sound concrete. Thanks to metakaolin’s excellent binding properties, it allows for the production of high-performance concrete, along with offering many other advantages, as explored throughout this article. Proper batching is a must, however.
A resistant, esthetic, and environmental product
Metakaolin is a natural pozzolan classified under Canadian Standards Association (CSA) A-3000-08, Cementitious Materials Compendium. A ‘pozzolan’ is a siliceous or siliceous and aluminous material that, in itself, possesses little or no cementitious value, but, in finely divided form and in the presence of water, reacts chemically with calcium hydroxide at ordinary temperature to form compounds possessing cementitious properties (per ASTM C618, Standard Specification for Coal Fly Ash and Raw or Calcined Natural Pozzolan for Use in Concrete). Thanks to this capability, metakaolin can be added to concrete to enhance some of its properties. Metakaolin is obtained via the calcination of either:
- kaolin, which is a result of feldspar alteration in granitic rock; or
- kaolin clay, which is produced when kaolin makes its way into secondary deposits. (Most known Canadian deposits are in Saskatchewan.)
Calcination occurs between 650 and 900 C (1200 and 1650 F) with no decarbonation reaction, which means when kaolin is heated, there is no carbon dioxide (CO2) emission. In Québec, the off-white variety of metakaolin is favoured due to its esthetics, enabling lighter-coloured concrete. This results in a reduced heat island effect and cooler, less energy-intensive structures thanks to an improved solar reflectance (i.e. albedo). With this property, using metakaolin can help obtain credits in the Canada Green Building Council (CaGBC) Leadership in Energy and Environmental Design (LEED) program for Sustainable Sites (SS) Credit 7.1, Heat Island Effect: Non-roof.
Metakaolin can be added to any type of concrete, and its fineness allows for smoother and more durable facings. This makes them ideal for any cement intended for architectural purposes—applications such as noise barriers, concrete slabs, and architectural panels. From a chemical perspective, by combining metakaolin with calcium hydroxide (i.e. free lime) via pozzolanic reaction, it becomes a hydraulic binder (i.e. calcium silicate hydrate [CSH]) that traps lime inside cement- and lime-based concrete.
The pozzolanic reaction therefore serves to reduce the amount of free lime in the material and limit efflorescence, significantly enhancing mechanical performance and product durability (i.e. resistance to environmental chemical attacks such as sulfation, chloride, and carbonation).
Metakaolin also helps keep cement hydrated. In certain formulations and under certain conditions (e.g. suitable heat treatment or choice of admixture), it can improve the performance of concrete of all ages.
When cement is mixed with water, free lime is obtained—therefore, efflorescence in concrete makes it less resistant. By introducing metakaolin in the mix, the metakaolin reacts with the free lime liberated by the reaction between cement and water, during the concrete hydration process, to create an element with cementitious properties that contributes to increasing the concrete’s resistance. The concrete reaches the desired level of maturity faster, and the metakaolin can even increase the resistance of young concrete, which helps increase productivity for precasting.