Understanding formaldehyde emissions and health
Products made with UF adhesives are most often found in building interiors because they have a lower tolerance to moisture and humidity, especially when the ambient temperature rises. Under high moisture and humidity, hydrolysis of the UF bond occurs, reversing the bond-forming reactions and increasing the rate of formaldehyde emissions. Consequently, UF adhesives are at a performance disadvantage to other thermosetting wood resins.
Producers of UF adhesives have been able to modify their formulations to reduce emissions and create products that comply with most global standards. Unfortunately, this has often been at the expense of product efficacy. Manufacturers who switch from a traditional UF adhesive to a low formaldehyde-emitting adhesive often experience drops in both product performance and manufacturing efficiency.
UF adhesives containing melamine as a co-reactant are often called melamine urea-formaldehyde (MUF) adhesives. The melamine provides improved strength and durability to the adhesive, while reducing the hydrolysis rate, which helps lower formaldehyde emissions from the adhesive relative to UF adhesives.
Due to their formaldehyde-emitting potential, wood products made with UF adhesives do not help a project earn points under LEED’s EQ Credit 4.4.
No-added-urea-formaldehyde adhesives
Adhesives falling in the middle of the formaldehyde-emitting spectrum are categorized as no-added-urea-formaldehyde (NAUF) adhesives. Unfortunately, this can be a confusing term for consumers and others unfamiliar with the terminology. NAUF can be easily misinterpreted to mean there is no formaldehyde of any kind in the adhesive, but these adhesives contain formaldehyde reacted with phenol (PF) or melamine (MF). Still, wood products made with these adhesives can help a project qualify for EQ Credit 4.4 because they are considered to be lower-emitting than UF adhesives.
Adhesives made with PF resins are typically found in products such as construction-grade plywood and OSB, which require high durability, along with moisture and weather resistance. They are less commonly used with interior wood products than UF resins.
An advantage of PF adhesives is their very low formaldehyde emission rate thanks to the resistance of the resin to hydrolysis by water. PF adhesives also have certain disadvantages. They are more expensive than UF adhesives, have higher processing requirements to cure, are very dark in colour, and may be unsuitable for use with some manufacturing equipment.
Other NAUF adhesives are created with MF resins. Typically found in interior-grade products requiring greater strength and improved moisture resistance, these adhesives cost more than their UF counterparts and may be unsuitable for use with some manufacturing equipment. MF adhesives generally emit more formaldehyde into the environment than PF adhesives.
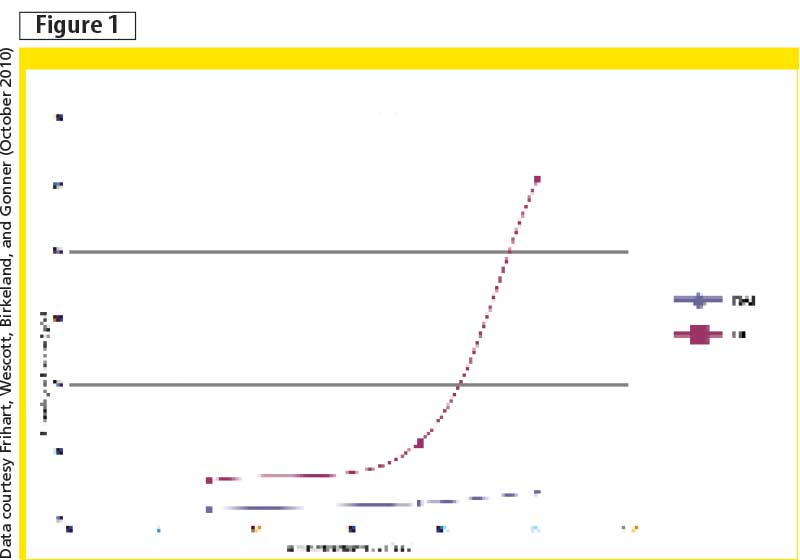
Factors influencing formaldehyde emissions
Several factors determine the amount and rate of formaldehyde emissions from wood-bonding adhesives. The first is the nature of the bond between the chemical used to make the adhesive and the formaldehyde. The weaker the bond, the more likely formaldehyde will escape into the environment. Urea-formaldehyde has the highest emission levels because its bond with formaldehyde is weakened when it reacts with water in the air—a chemical reaction called hydrolysis. As a result, the higher the temperature and humidity, the more formaldehyde is released into the environment (Figure 1).
There can also be a direct link between the concentration of formaldehyde-based adhesive in the end product and formaldehyde emissions. The higher the concentration of formaldehyde in a product, the higher the product’s emission levels.
Another determinant of formaldehyde emissions is where the adhesive is located in the end product. For example, particleboard and MDF have adhesives throughout, making them more likely to emit higher levels of formaldehyde. When these products are covered with another material, it may help reduce emissions, depending on the porosity of the covering material. When the top layer of a wood product, such as engineered flooring, is covered with a veneer, the rate of off-gassing is slowed, although not completely eliminated.
Conclusion
In the face of escalating concerns about the impact of formaldehyde on human health, many adhesive industry researchers, as well as producers of manufactured wood products, are investing time and resources to reduce formaldehyde emissions from wood-bonding adhesives. Others are aggressively developing and promoting no-added-formaldehyde adhesives, which neither contain nor release any formaldehyde into the environment.
Separating fact from fiction about the ever-changing range of adhesive options is critical for specifiers, architects, and designers in Canada, the United States, and around the world. Based on the facts, informed decisions can be made about manufactured wood products that are in the best interests of their clients and, at the same time, have a positive impact on the air quality in the projects they build and design.
Dwight Chapman is strategic marketing manager for Ashland Incorporated, responsible for Soyad adhesive systems used in building products. He has more than 28 years of technical, sales, and marketing experience with adhesives, specialty paper chemicals, and flexible laminated materials. For the past five years, Chapman has been involved in developing and marketing bio-based adhesive systems for the wood industry. He can be reached at dwight_chapman@ashland.com.