Understanding flooring performance data to optimize specifications
The variability in abrasion resistance testing
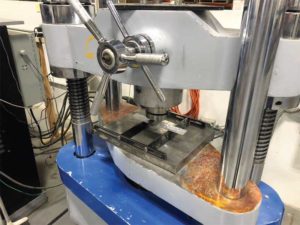
ASTM D4060-14 evaluates a floor coating’s abrasion resistance using an automated taber abraser with a weighted, abrasive wheel to scuff the surface of a rigid coated sample. Lab technicians pre- and post-weigh the sample to determine how many milligrams of coating are lost after a set number of cycles.
The reproducibility and repeatability of this test is highly subjective “due to changes in the abrasive characteristics of the wheel during testing,” per ASTM D4060-14. Further, the smoothness of the coating’s finish can cause varied results. Coatings with greater textures may also demonstrate higher abrasion potential simply because the abraser will grind off the coating’s ‘peaks’ before reaching a smoother area. Even if the smooth area of the coating has low abrasion potential, the weight of the lost original peaks suggests a lower overall abrasion resistance.
When comparing testing data among floor coatings, specifiers need to ensure the tests used the same wheel weights and the same number of cycles for more accurate comparisons. Additionally, as noted previously, they should ensure the data uses the same units of measurement.
Subjectivity in chemical resistance testing
ASTM D1308-02(2013), Standard Test Method for Effect of Household Chemicals on Clear and Pigmented Organic Finishes, is a useful measure of a floor coating’s endurance when exposed to cleaning solutions or spills. Lab technicians conduct the test by soaking a cotton ball in a chemical reagent and resting it on top of a coated sample, covered or uncovered, for a specified duration under controlled temperature and humidity conditions. However, the reported results are subjective and are expressed via a visual, nonquantitative evaluation of the coating’s surface condition after chemical exposure. Hence, coatings manufacturers’ chemical resistance assessments are not directly comparable.
When evaluating chemical resistance, specifiers should consider the subjective nature of reported data and compare samples rated by the same lab at the same time, if possible, to ensure results are at least somewhat comparable. It is also important to understand chemical resistance and stain resistance is not the same. A floor coating with excellent chemical resistance against changes in gloss, blistering, softening, or loss of adhesion may still stain.
Optimizing product selections
Specifying an optimal floor coating system for a specific environment can lead to enhanced efficiencies, improved performance, reduced life-cycle costs, and other benefits. This is why it is important to make careful, informed coatings selections. Given the variability and subjectivity of certain ASTM tests, it can be difficult for specifiers to make sound selections. To help, here are a few tips.
Compare relevant side-by-side testing
Make sure the products being compared were tested in the same manner at the same time in the same lab and with the same technician. These parameters ensure objectivity and standardization for the reported data. Also, it is important to make sure the tests are relevant to the application.
Evaluate case histories
While lab tests are helpful, there is no substitute for real-world performance. Some products will perform poorly in accelerated testing environments and exceptionally in the field, or vice versa. It is beneficial to look to relevant application case histories to verify product performance.
Avoid sole-source specifications
Specifications listing a specific product—whether explicitly or by default because other materials cannot meet the published requirements—can artificially inflate the job costs without providing any extended service life benefit. It is advisable to expand the specification and entertain requests for viable alternatives if they enhance performance.
Explore the data
Be sure to question the relevance and accuracy of data points and ask a reputable coatings manufacturer to explain why certain data is important for specific applications.
Design the concrete for the application
It is important to remember the concrete substrate is the lowest common denominator in the resinous flooring equation. First, it is crucial to make sure the concrete’s compressive, tensile, and flexural strength properties meet the facility’s performance requirements. Then, ensure the specified coating offers better performance than the concrete in these categories, understanding the flooring will not perform significantly better, but that it should not fail before the concrete.
Following the guidelines above can help specifiers improve the validity and relevance of their specification requirements, ultimately leading to optimal floor coating selections that ensure long service lives and minimal life-cycle costs for asset owners.
ASTM TESTING TERMS DEFINED |
Precision: The closeness of agreement among test results obtained under prescribed conditions. A precision statement provides guidelines for allowable variances.
* For more information, read Pat Picariello’s “Fact vs. Fiction: The Truth about Precision and Bias,” published in ASTM Standardization News, March 2000. |
Casey Ball is global market director – flooring, food & beverage and pharmaceutical for Sherwin-Williams Protective & Marine Coatings. Ball has specialized in the flooring and coatings market with the Sherwin-Williams Company for 17 years. He has certified coatings inspector accreditation from National Association of Corrosion Engineers (NACE) International and certified concrete coatings inspector accreditation from the Society for Protective Coatings (SSPC). He holds a bachelor’s degree in business from Wilmington College and earned his MBA in marketing from Franklin University. He can be reached at casey.a.ball@sherwin.com.