Understanding flooring performance data to optimize specifications
Beware of substrate bias in compressive, tensile, and flexural strength tests
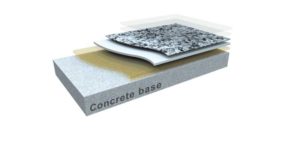
To better understand ASTM testing data, it is critical to review five standards likely to appear in the mix of data comparisons for flooring specifications.
First, this article will focus on three test methods—for compressive, tensile, and flexural strength—which can be misleading due to the tests being performed on floor coating samples not adhered to a concrete substrate. Each test should yield results exceeding the properties of an average concrete substrate, which is certainly desirable. However, the reported test values will not match real-life performance because they do not consider the floor coating’s application to a weaker concrete substrate. Based on the reported data alone, a specifier may expect the flooring system to perform to its published ratings, not realizing the concrete underneath is likely to fail well before these levels.
Concrete flooring substrates are commonly poured at a thickness of 102 to 152 mm (4 to 6 in.) (Figure 1) and typically feature average performance values of:
- compressive strength: 28 to 35 MPa (4000 to 5000 psi);
- tensile strength: 2 to 3 MPa (300 to 400 psi); and
- flexural strength: 4 to 6 MPa (600 to 800 psi).
Each property above can be enhanced by adding reinforcing elements, with the concrete slab ultimately needing to be designed so that it meets the performance requirements of the environment.
Resinous floor coatings are applied to concrete slabs at a thickness of only 3 to 6 mm (118 to 236 mils) (Figure 1). Even at this low thickness, the floor coating will have better compressive, tensile, and flexural strength than average concrete. However, these higher values may cause confusion for specifiers, who may assume they can realize this performance level from the entire floor. In reality, because the concrete is the lowest common denominator, the performance of the flooring system essentially becomes that of the concrete. For example, a floor coating with a higher compressive strength than concrete may hold up under a heavy load, while the concrete underneath may be subject to failure. While the coating may remain intact, the floor has failed, as coating adhesion issues are sure to follow.
ASTM testing results for compressive, tensile, and flexural strength can still be helpful for making general product comparisons despite their limited relevance to the concrete substrate. However, it is important for specifiers to understand some nuances for each test method that may affect their comparisons of interlab data.
Compressive strength
ASTM C579-18 measures a material’s resistance to deforming or breaking under an applied compression force. Following the standard’s Test Method B protocol, a flooring manufacturer or lab will cast a 50-mm (2-in.) cube of a coating material. A technician will then determine how much force can be applied to the cube before the sample crushes (Figure 2).
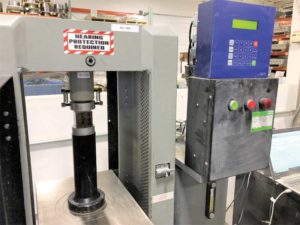
Values obtained via this testing method may not correlate to the real-world application of the coating at its normal thickness. The applied coating’s strength will still be greater than that of average concrete. This is why the concrete could theoretically crush and crack before the coating, making a coating’s higher reported value almost irrelevant for product comparisons. Specifiers simply need to design the concrete to meet service demands and then ensure the specified floor coating’s compressive strength is higher than the concrete’s rating.
ASTM C579-18 provides a comparable value among test specimens, allowing specifiers to assess reasonably accurate testing values from product data sheets. Still, those values may not be precise, as this testing method has a 15 per cent allowable variance for reproducibility due to sample preparation variability.
To overcome the deficiencies of this test method, specifiers may want to look to the coating’s elongation properties to ensure it can bridge any cracks that may eventually form in the concrete substrate.
Tensile strength
ASTM D638-14, Standard Test Method for Tensile Properties of Plastics, determines a floor coating’s resistance to breaking under the stresses of being pulled apart (tension). It rates a coating’s elongation capability (pulled apart), which is the opposite of its compressive strength (pushed together).
Using a prepared dumbbell-shaped test specimen of a floor coating, a lab will insert the sample into a testing apparatus. The machine pulls the sample in one plane to determine how much it stretches before deforming drastically (elongation at yield) or breaking (elongation at break).
When evaluating flooring systems based on tensile strength, specifiers need to ensure the coating will adhere tightly to the concrete substrate. As a resinous flooring system cures and its chemical crosslink tightens, the coating will exert a lateral (tensile) force on the concrete. A similar force occurs as vehicle traffic moves across the floor and transfers that lateral energy to the bond line between the concrete and flooring. If the tensile strength of the concrete is too low, the flooring system could delaminate from the concrete substrate in either the curing or vehicle traffic scenario.
To reduce delamination potential, specifiers should select concrete with a minimum tensile strength of 1.7 MPa (250 psi). This is usually easy to accommodate, as the tensile strength of average concrete is about 2 to 3 MPa. Tensile strength can be as high as 14 MPa (2000 psi) for resinous coatings. It is important to remember the actual performance of the applied floor coating will ultimately be much closer to that of the concrete substrate, not its lab-tested values, which are independent of concrete.
When comparing products’ tensile strength data, the data may not provide apples to apples comparisons, as ASTM D638-14 says, “Tensile properties are known to vary with specimen preparation and with [the] speed and environment of testing.” To make a truly direct comparison, specifiers need to review data from equally thick samples prepared and tested side by side-in-the same lab.
Flexural strength
ASTM D790-17, Standard Test Methods for Flexural Properties of Unreinforced and Reinforced Plastics and Electrical Insulating Materials, must also be reviewed within the context of the concrete substrate, as tests usually are performed independent of a substrate. Lab technicians prepare a rectangular cross-section specimen of coating material and then use a three- or four-point loading system to apply a bending load to the specimen (Figure 3). The sample’s measure of deflection before its outer edges rupture is its flexural strength.
For the lab-tested resinous flooring samples, ASTM D790-17 results may be in the 14 to 28 MPa range, but the flexural strength of average concrete is only 4 to 6 MPa. Therefore, the concrete substrate will break under much lower flexural stresses than the flooring system. If the concrete cannot handle an applied load, then a thin coating on top will not make much of a difference, making the higher reported flexural strength results nearly irrelevant when comparing flooring systems. Specifiers should design the concrete for the facility’s requirements and then specify coatings with higher flexural strength than the concrete. Additionally, when reviewing the testing data, specifiers should understand reported data may not be accurately comparable among the products, as ASTM D790-17 says, “Experience has shown that flexural properties vary with specimen depth, temperature, atmospheric conditions, and strain rate.”