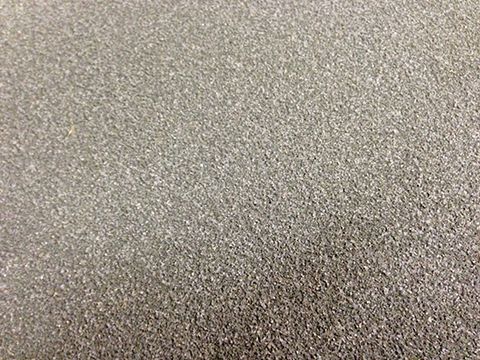
Overlay characteristics
Basic concrete is a composite made of portland cement, sand, aggregate, and water. While more complex concrete designs are readily available, however, this basic concrete recipe will easily yield concrete in the range of approximately 25 to 35 Mpa (3626 to 5076 psi) of compressive strength. In contrast, a typical cementitious overlay will provide anywhere from 30 to 50 MPa (4351 to 7251 psi) in compressive strength.
The engineering of an overlay is much more elaborate in its basic formulation, mainly because it is used in very thin applications—most commonly at 9.5 to 19 mm (3/8 to ¾ in.) thickness—far below the 50-mm (2-in.) minimum requirement for concrete. Therefore, when using thin construction materials such as cementitious overlays, these materials require superior adhesion, better cohesiveness of the cement matrix, higher compressive strength, and greater flexural strength to perform similarly to the concrete mass on which they are installed.
To meet these requirements, sophisticated formulations using special hydraulic cements are used to accelerate cure times and minimize shrinkage. Polymers are used in the formula to increase adhesion and flexural capabilities and to improve the cohesiveness of the cement matrix.
The rheology-modifying agents are used to minimize segregation and bleeding, in order to achieve high fluidity and long working time. High-efficiency super-plasticizers are incorporated in those formulas. The result is ‘engineered cements’ or overlays, and these formulations require extensive testing to offer high performance.
Installation of overlays
Once the primer has set and the un-bonded excess sand has been removed, the overlay is ready to be installed. Experienced crews versed in overlay placement understand the importance of properly staging workstations, strategically planning the size and direction of the pour, and having the correct number of skilled workers on hand. The use of such specialized crews is highly recommended as final results rely greatly on correct installation of the overlays.
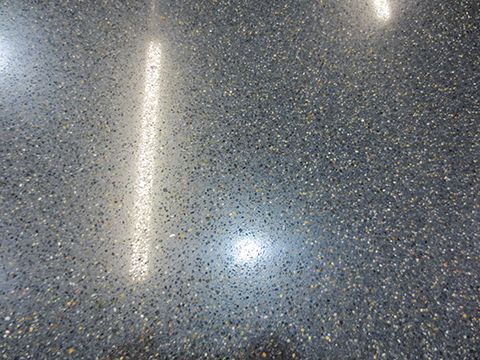
At this stage, the floor may have been designed with decorative separator strips, metal inserts, or simply formed some other way to make shapes and colour patterns. In either case, the options are almost inexhaustible, as the design professional can work with colour pigments, forms and shapes. Decorative glass, stone, sand, or metals can also be incorporated into the finish, which yield interesting effects when exposed by diamond polishing.
Once the overlay is installed, it is comparable to an artist’s canvas. Colour pigments can be integrated within or installed over top of the overlay with products such as stains or dyes once it has set—creating even more possibilities.
Overlays can be advantageous because they:
- are more economical than replacing concrete;
- can be laid down as thin as 9.5 mm (3/8 in) and as thick as 50 mm (2 in.);
- lend well to designs, including;
- colouring or addition of aggregates and decorative elements; and
- offer a unique look and feel.
However, overlays have disadvantages because they:
- are cement-based, which can result in cracks;
- require skilled craftsmen; and
- are a manmade product, and can potentially have a mottled variable look.
Clear protective resin coatings
One option for finishing the overlays is to use clear protective coatings such as epoxy, poly-urethane, or poly-aspartic coatings or specialized waxes. This final step ensures the stain protection needed for a durable long-lasting floor.
Advantages of these coatings include:
- relatively fast execution;
- ability to re-coat years later if needed;
- being an economic option;
- provision of a good barrier against staining; and
- salt-resistance.
Some of the disadvantages include:
- a synthetic, plastic look—which may be undesirable;
- subject to scratching (especially epoxies);
- the tendency of certain products to darken the colour of the floor; and
- the production of outgassing traces, in the form of pinholes, moon, or fish eyes on the surface due to displacement of air/moisture from the substrate through the coating before it has a chance to cure.