Understanding cementitious decorative overlays
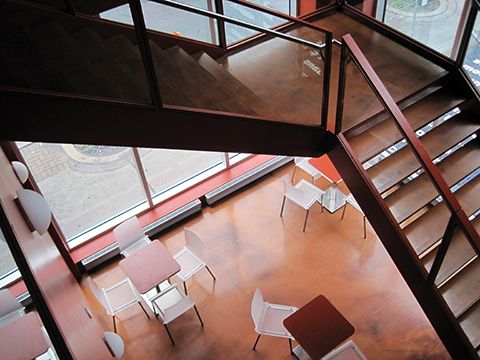
By Giovanni Natale
Overlays were born in the modern era out of necessity. (For simplicity’s sake, and for the purpose of this article, the term ‘overlays’ will be used instead of ‘polishable self-leveller’ or ‘wear-course self-levellers.’) When concrete needed to be refurbished and restored, but could not be elevated to the decorative concrete status, another material was needed to fill the void. Thanks to manufacturers’ research and development labs, formulations of engineered cements, commonly known as overlays, were developed. Overlays exhibit similar characteristics to concrete, but in a much thinner version—typically 9.5 to 50 mm (3/8 to 2 in.). Designers have come to expect overlays to look and perform similarly to concrete.
Many components within the decorative overlays are very similar to those of concrete—mainly the sands, portland cement, and the esthetic. These similarities cause concrete and overlays to be classified as the same family of building materials. Overlays are designed to give a concrete substrate its intended functionality and offer optimal performance.
Concrete has historically been used as a supporting material for structural applications, as well as a bed or substrate for embellished coverings. Only recently has the popular term ‘decorative concrete’ evolved and led the industry to think more in terms of the material as a finished product, rather than solely as a supporting structural building material. This is a new tool in the design professional’s toolbox that can complement certain décor styles. What does one need to know about these construction materials to use them in project design?
Any time concrete is to be transformed and used as a decorative final wear course, the concrete must be evaluated to ensure it is in suitable shape. Designers should check the uniformity of the existing concrete to ensure it is acceptable, or learn whether it needs to be repaired. However, patching and repairing concrete often leaves a sporadic, discoloured look that is not esthetically pleasing.
Concrete may be unusable in terms of decorative applications when:
- cracks needing repair cannot be camouflaged and will stand out because of their shapes and colour difference once repaired;
- spalls or rough concrete in need of repair shows visible colour variations and non-symmetrical shapes once repaired; and
- additions of new concrete slabs adjacent to old ones show colour differences as well as highlight the aggregates different concretes contain.
These are only a few reasons why the existing concrete may not be suitable for a decorative makeover. Whenever concrete is unable to be directly treated and refined into a decorative floor, the use of a cementitious overlay can be a solution.
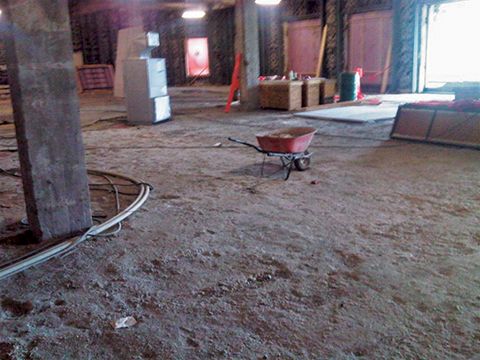
Overlays are designed and manufactured to restore concrete to its original condition—similar to what it may have looked like the day after it was poured and finished. From that point, numerous other decorative options are possible. The most popular solutions are those requiring diamond polishing and clear resinous protective coatings. Both these systems can be pigmented and can contain integrated terrazzo strips or sawcuts to define shapes, colour schemes, and logos. They can also incorporate broadcast stone, glass, or metal. By using these ideas, the possibilities are almost limitless for the designer.
Surface preparation
The first step in the successful installation of these decorative overlays is to have a properly prepared substrate. All repairs or alterations to the concrete are usually done before surface preparation. In general, fast-curing, polymer-modified mortars that achieve high early strength are used for the repairs to accelerate the delivery of the project.
The non-profit industry association, International Concrete Restoration Institute (ICRI), provides a guideline to surface preparation for those dealing with concrete repair. The ICRI also provides a system of Concrete Surface Profile (CSP) chips numbered from CSP 1 to CSP 10, which give a clear visual indicator of the profile needed. Manufacturers recommend the appropriate CSP required for their products—simplifying the task for a design professional when writing specifications for tender.
A profile of CSP 3, produced by means of shotblasting, seems to be relatively common within the industry. Additionally, the use of a two-component, 100 per cent solids epoxy primer into which a 16-mesh clean silica quartz sand is broadcast to refusal can create a suitable profile for the overlay.