Underlying Considerations for Overcoating: Lessons learned for metal building façades
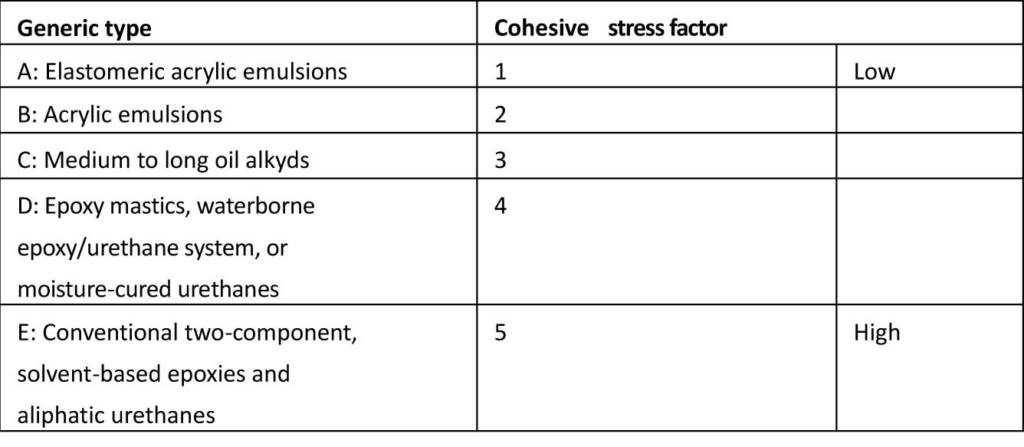
Choosing an appropriate overcoat system
When selecting an overcoating system, it is important to consider the cohesive stress exerted on the existing system will vary with generic type (Figure 3).
Nonflexible, conventional two-component epoxies and aliphatic urethanes will develop more cohesive stress upon curing than more flexible coatings such as acrylic emulsions, medium-to-long alkyds, moisture-cured urethanes, and epoxy mastics.
The higher the film thickness of the overcoat, the greater the cohesive stress on the existing paint system. Applying two-component epoxies at 12 mils DFT to an aged paint system with marginal adhesion could result in the old system pulling apart at its weakest adhesion link—between coats or from the substrate.
Geographic location also plays a crucial role in the selection of an appropriate overcoat system. In areas where frequent freeze/thaw cycles occur, coating systems are subject to more stress, so flexible, low-cohesive-stress overcoat systems are the appropriate choice.
Among the new coating products intended for use as overcoats on minimally prepared, sound-rusted steel and previously coated surfaces is a single-component, mastic waterborne acrylic coating that can be applied in a wide range of environments. This coating offers 200 per cent elasticity, which enables it to expand and contract with the substrate as the temperature varies.
The development of new infrared (IR) heat-reflective pigments in finish coatings can significantly reduce the amount of heat absorbed and retained by a metal building’s exterior wall and roof surfaces. The result is savings in fuel and cooling costs.
While most reflective coatings are white, coatings manufacturers have been able to incorporate IR-reflective pigments into field-applied, air-dried fluoropolymers offering a wide range of colours. This new technology enables the architectural community to gain the benefits of heat-reflective coatings without having to sacrifice colour and esthetics. The use of IR-reflective coatings on a structure can also earn points in four Leadership in Energy and Environmental Design (LEED) categories, described in Heat Island Reduction Option 1 (non-roof and roof). (Details on these categories can be found in LEED v4 for Building Design and Construction, Sustainable Sites (SS) Credit,: Heat Island Reduction, pages 38 to 39.) LEED requires roofing materials used on low-slope roofs with a slope of less than 2:12 to meet an initial solar reflectance index (SRI) of 82 (64 for three-year aged SRI). Steep-sloped roofs with a slope of more than 2:12 must have an initial SRI of 39 (32 for three-year aged SRI).