U-Factor: Beyond compliance to standards
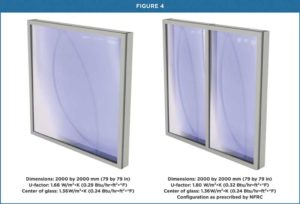
Context and Criteria
The standard method for determining U-factor values is used to establish basic criteria, allowing a comparison of products during the preliminary stages of a project, or to ensure compliance with the NECB’s prescriptive requirements. U-factor data determined by this approach are ubiquitous in the commercial building and fenestration industry. It is imperative to understand the context in which the values were determined to better assess how the results may be influenced.
Two components emerge in the standard method for determining U-factors:
• The protocol, which is the procedure to be followed to carry out the computer simulation or the physical test; and
• The specimen, which is the product itself.
It is expected that all parameters of these two components will be exhaustively defined, allowing an equal comparison of fenestration products.
Among the protocol’s many criteria are:
• The calibration of measuring devices;
• The software versions to be used in case of simulation, or the installation of the specimen in the case of a physical test;
• The indoor and outdoor temperature differentials;
• The location of temperature reading points on the simulated or physical specimen;
• The wind speed(s); and
• Any additional reference standards.
As for the specimen, the objective is to measure its performance; however, other factors also have an impact on the resulting U-factor. Some of these factors may not be integral or consistent with the product’s design. The variations in these factors can be especially important in the case of curtain wall systems. Curtain walls offer many options to customize a commercial building envelope’s appearance and performance. Reviewing Figure 2, one can see how non-standard fenestration systems can impact an overall U-factor and why specifiers must carefully review their data.
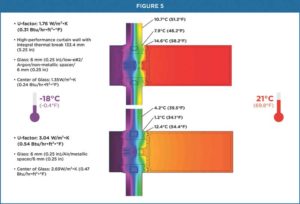
Defined Dimensions
To provide a framework for specimens’ standard analysis, NFRC 100 prescribes dimensions for each type of fenestration product (see Figure 3).
Standard dimensions make it easier to compare similar products’ U-factor values. For different fenestration systems, standard results are not a good indicator in product type selection because they cannot be compared on an equal basis. The U-factor performance of a casement window compared with dual-action window serves as a good example.
Compliance with these dimensions and configurations remains important to compare the same type of fenestration products. Particularly in the case of aluminum curtain wall products, the ratio between the framing members and the glass is a key aspect in the measurement of thermal transmittance. Furthermore, to disregard prescribed configurations for curtain walls and only use the overall dimensions for determining standard U-factor would produce an inaccurate result (see Figure 4).
The simulation in Figure 4 shows the same model of high-performance curtain wall with an integral thermal break and with all the same components in the 2000 x 2000 mm (79 x 79 in.) size. The difference between these models is that one on the left is undivided due to a mistaken assumption regarding the configuration requirement. The one on the right is divided in two vertical lites as prescribed by NFRC-100. The difference in results comes from the aluminum mullion division that generates more heat transfer. This comparison is a good indication on how more aluminum mullions on a design can influence the performance.
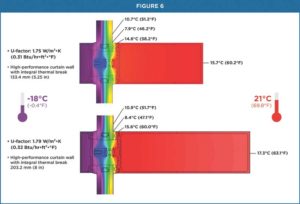
Validating Variables
Using the same curtain wall system, Figures 5 and 6 demonstrate how altering two variables–glazing type and mullion depth–can affect U-factor values and lead to different performance results.
The choice of insulated glazing units (IGUs) and the depth of the mullions are outside NFRC 100’s prescribe approach. As shown above, these have a notable influence in the curtain wall system’s U-factor and thermal transmission. It is very important to coordinate the framing specification with the glass specification, so the separate components combined can achieve the desired U-value required for the project.
There are a variety of IGUs that may improve the overall performance of a fenestration product, especially for aluminum curtain wall systems. An overall system U-factor will depend on the choice of glazing. The use of high-performance IGUs may compensate for lower thermal performance elsewhere in the curtain wall system’s design. It is possible to separate the system’s overall performance (Ut) from the performance of the aluminum framing (Uf). Again, keep in mind that the frame’s lower thermal performance may be mitigated by the IGU’s higher performance.
Frequently, the IGU is selected and specified independent of the fenestration system’s framing based on project-specific needs. For optimal performance, these should be reviewed together. It is imperative to ensure consistency between the complete system’s specified U-factor and the IGU’s capacity to support the overall system requirements. For example, specifying a U-factor of 1.65 W/m² • K (0.29 Btu/hr•sf•F) for both the IGU and the overall fenestration product is a required performance impossible to achieve.
As for the importance of mullion depth, this also is dependent on the particular needs of the project. Structural performance and safety should always be the first priority. In general, a deeper mullion will have a positive affect on condensation resistance, but it can also can have a negative affect on thermal transmittance. This is an important consideration when designing the project and its curtain wall and fenestration systems, as well as in analyzing the data provided as proof of compliance to meet thermal performance specifications, building codes, structural requirements, and energy efficiency goal.