Turning retrofits into success stories with IMPs
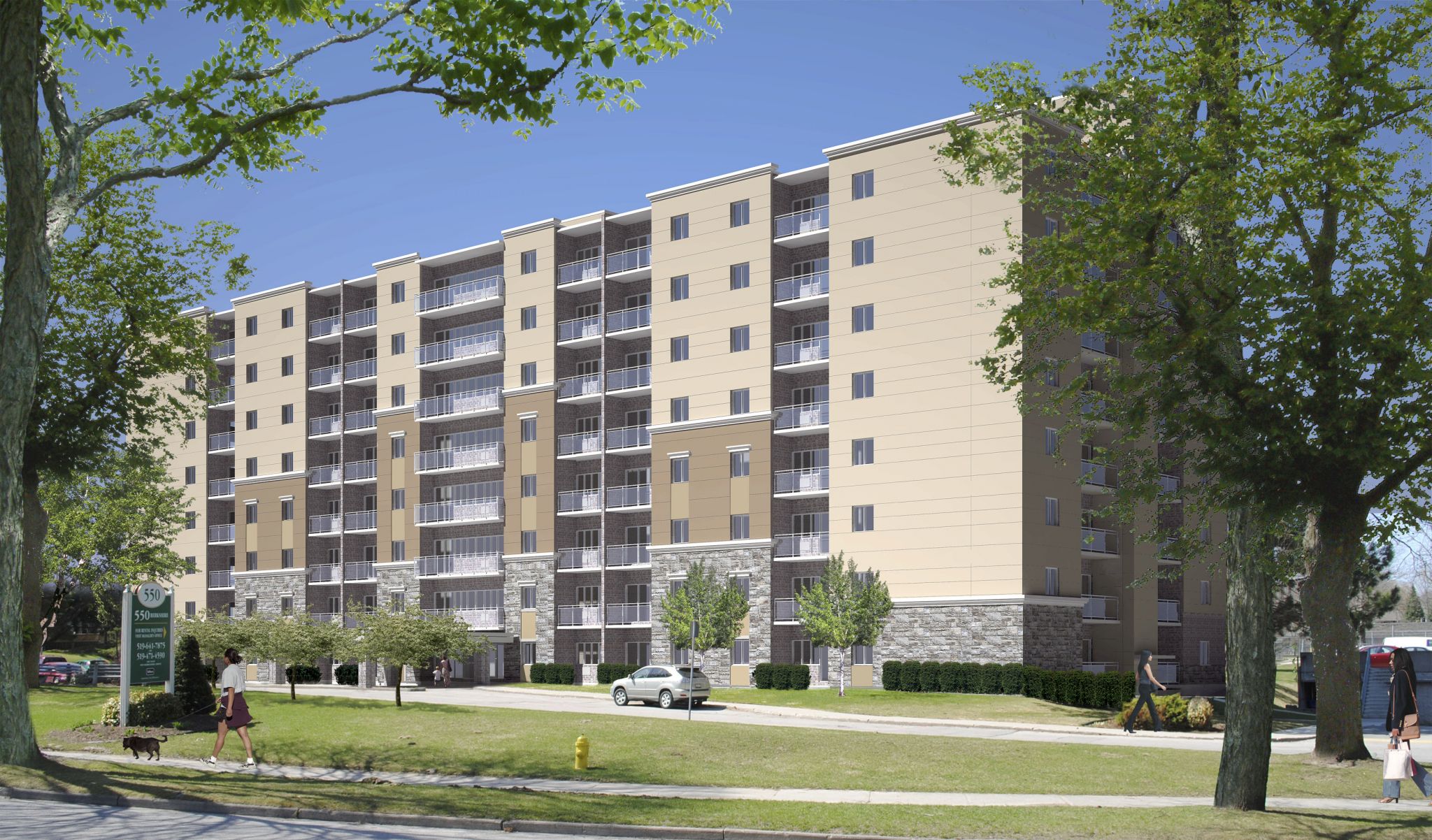
By Paul Bertram, CSC, FCSI, CDT, LEED AP, and Ian Manser, CEM
Driven by the principles of high-performance energy (HPE) buildings through government, energy codes, and the green building movement, building energy designs across Canada and around the world strive to improve. The increasing focus on the implementation of energy-efficiency requirements, for both new construction and deep energy retrofits for commercial and public buildings, begins with envelope-first energy efficiency, reduced energy demand loads, and related greenhouse gas (GHG) reductions.
This article focuses on the benefits of deep energy retrofits using the addition of exterior insulation, specifically insulated metal panels (IMPs), to improve the performance of existing building enclosures.
National solution to a global problem
The 2012 International Energy Efficiency Scorecard compiled by the American Council for an Energy-efficient Economy (ACEEE), ranks 12 of the world’s largest economies on 27 different energy-efficiency indicators, roughly split between measureable metrics and energy policies.
- more than 78 per cent of global gross domestic product;
- 63 per cent of global energy consumption; and
- 62 per cent of the global carbon dioxide-equivalent emissions.
With a score of 37 of 100, Canada ranked second-to-last, only beating out Russia. This signifies ample opportunities for Canada to improve its performance as compared within these global benchmarks.1
The nations scoring in the top rankings harvest residual benefits, such as increased marketplace competitiveness, the ability to create employment, and a more stimulated national economy. With Canada’s well-documented energy resources—including abundant opportunities for implementation of low- and non-carbon fuels such as solar and geothermal—the country can compete in a world of rising energy prices and increasing global competition for energy resources.
Another oft-quoted statistic is, on a global scale, residential and commercial building sectors account for 35 to 40 per cent of total energy consumption.2 Considering this, and to make the most efficient use of its regional and national energy supply opportunities, Canada has a growing commitment to energy conservation in these areas.
Today, successful retrofits stretch across the country. Toronto is now considered a leader when it comes to energy retrofits of existing buildings and currently provides a “Better Buildings Partnership” program for increasing the energy efficiency of existing buildings. With more than 2200 projects completed as of March 2014, and a cumulative energy savings of nearly 3 million MWh, the results of this collection of programs speak for themselves.3
In particular, the municipal, academic, social services, healthcare (MASH) program connects building owners and managers with incentives that facilitate the implementation of new energy conservation technologies in existing institutional buildings.
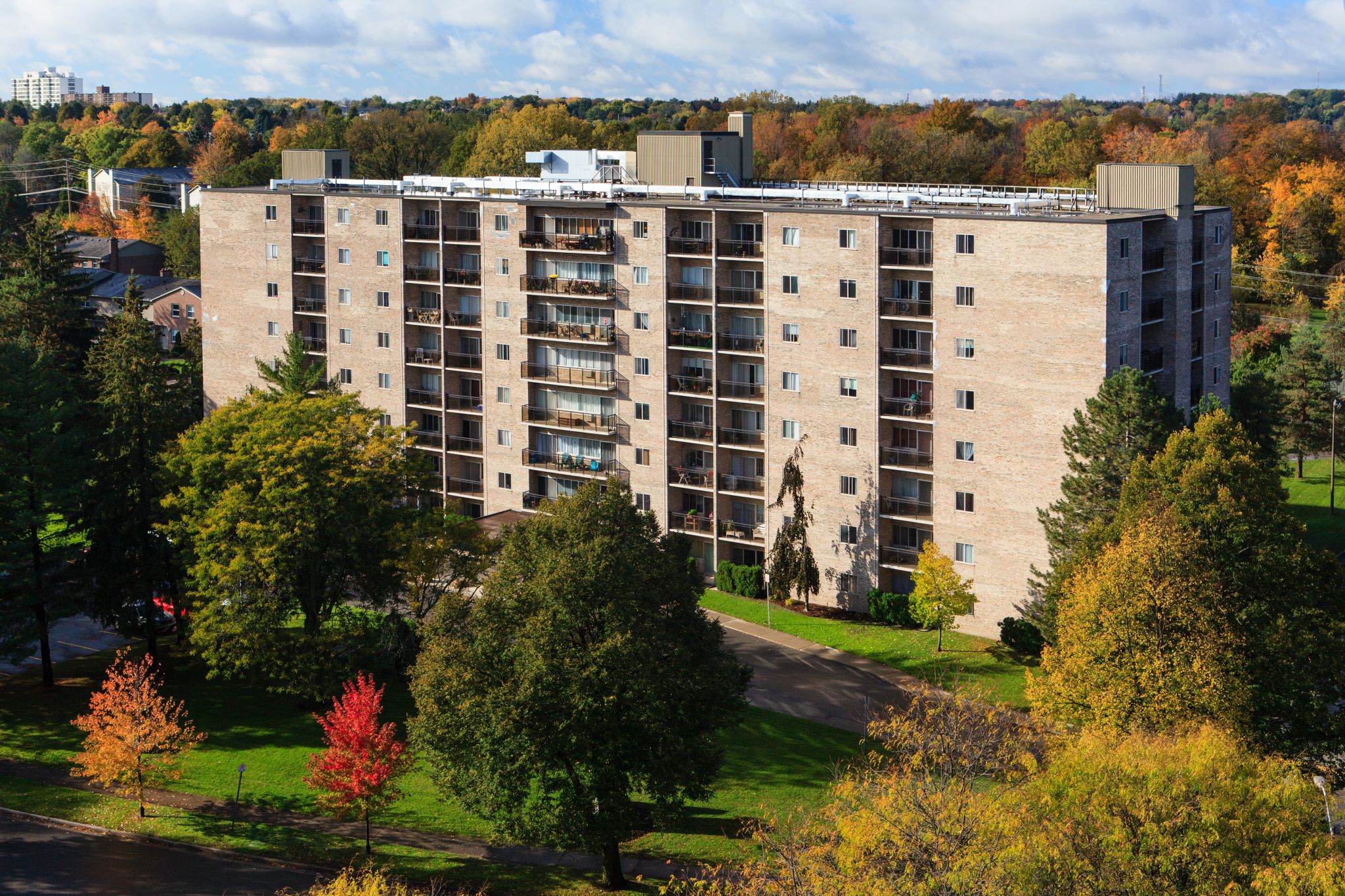
Understanding the role of deep energy retrofits
Energy efficiency improvements in existing buildings tend to be addressed by upgrading outdated systems—such as lighting and building control assemblies—with modern, better-performing technologies. One of the greatest sources of improvement can be realized by upgrading HVAC technologies to take advantage of improved distribution and environmental management, along with the efficiency improvements developed over the last few decades. However, without similar improvement to the building envelope, the potential savings made possible by these new technologies can be significantly limited.
A design-centred, whole-building approach to a retrofit, in which all the interactions in a building’s systems are considered, can yield substantially higher energy savings. Known as deep energy retrofits (DERs), these projects aim for energy savings upward of 50 per cent over previous HVAC costs. The term ‘deep energy retrofits’ may not be familiar to every building professional, but the concept certainly is. The basic philosophy is prompted by Leadership in Energy and Environmental Design (LEED) third-party certification program and an internationally accepted benchmark for the design, construction, and operation of high-performance buildings, promoting a whole-building approach.
Given the average percentage of HVAC costs exceeds 35 per cent of total energy consumption, maintaining high performance requires a focus on long-term capabilities throughout a building’s lifecycle, starting with a quality envelope design. Multiple building systems jointly designed, rather than as a sum of individual parts, provide a process that aligns with aggressive energy savings targets. While a whole-building design plan for energy efficiency upgrades focuses on the integral retrofits of multiple building systems, starting with an optimized building envelope design—considering thermal environment, durability, airtightness, and weather resistance—creates the baseline construction allowing the potential savings for other retrofit energy conservation measures (ECMs) to be maximized.
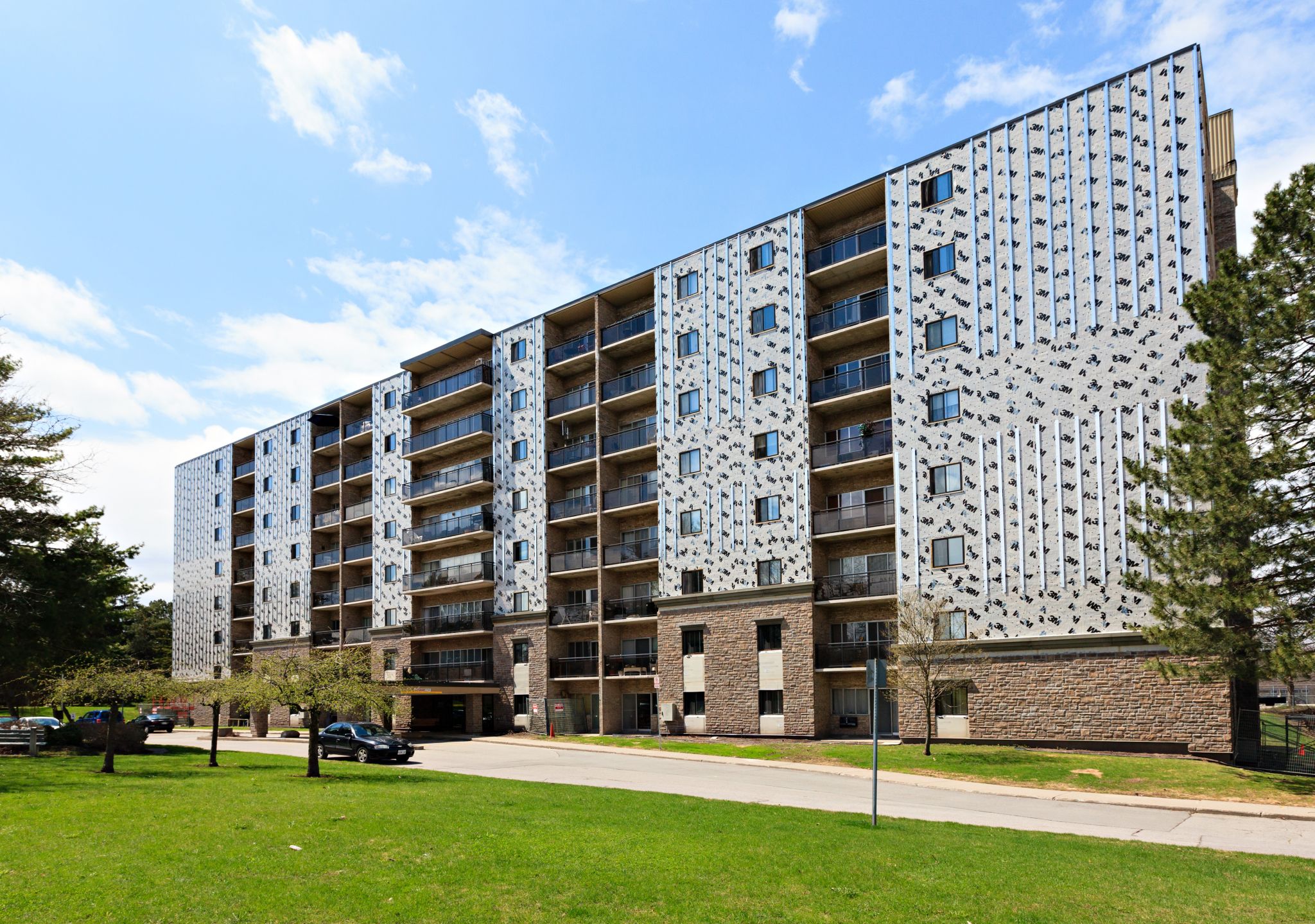
In this context, an energy-efficiency, envelope-first DER strategy is fairly straightforward—controlling the movement of energy between the interior and exterior environments, as mechanically adding or removing energy is expensive. It starts with improving the enclosure’s insulating value with optimized thermal performance of opaque roofs, walls, and windows and sealing against air leaks.
Once the enclosure is airtight and thermally optimized, the project team can more easily ‘right-size’ energy conservation measures such as HVAC, lighting, hot water, and building controls. This technique refers to the ability to install systems designed for the size and energy needs of the building to operate at the highest efficiency.
Insulated metal panels prove their place in a DER
In the past, insulation retrofits of existing buildings typically involved the filling of framed cavity walls with additional insulation. This limited the amount of effective thermal resistance that could be added due to the existing stud cavity or strapping depth, the thermal resistance of the insulation material, and the amount of thermal bridging present in the framing. To overcome these limitations, the addition of insulation to the exterior of existing buildings has been demonstrated to be an effective means to provide higher effective R-values for opaque envelope assemblies. IMPs, whose standard installation involves attachment to the outside (or inside) of the building structure, provide a viable means of achieving additional thermal resistance in these circumstances.
The benefits of this approach extend beyond added thermal resistance. IMPs are factory-assembled wall and roof cladding components typically consisting of a polyisocyanurate (polyiso) insulation core, encapsulated between impermeable interior and exterior steel skins, with factory-formed joints providing a homogeneous installation.
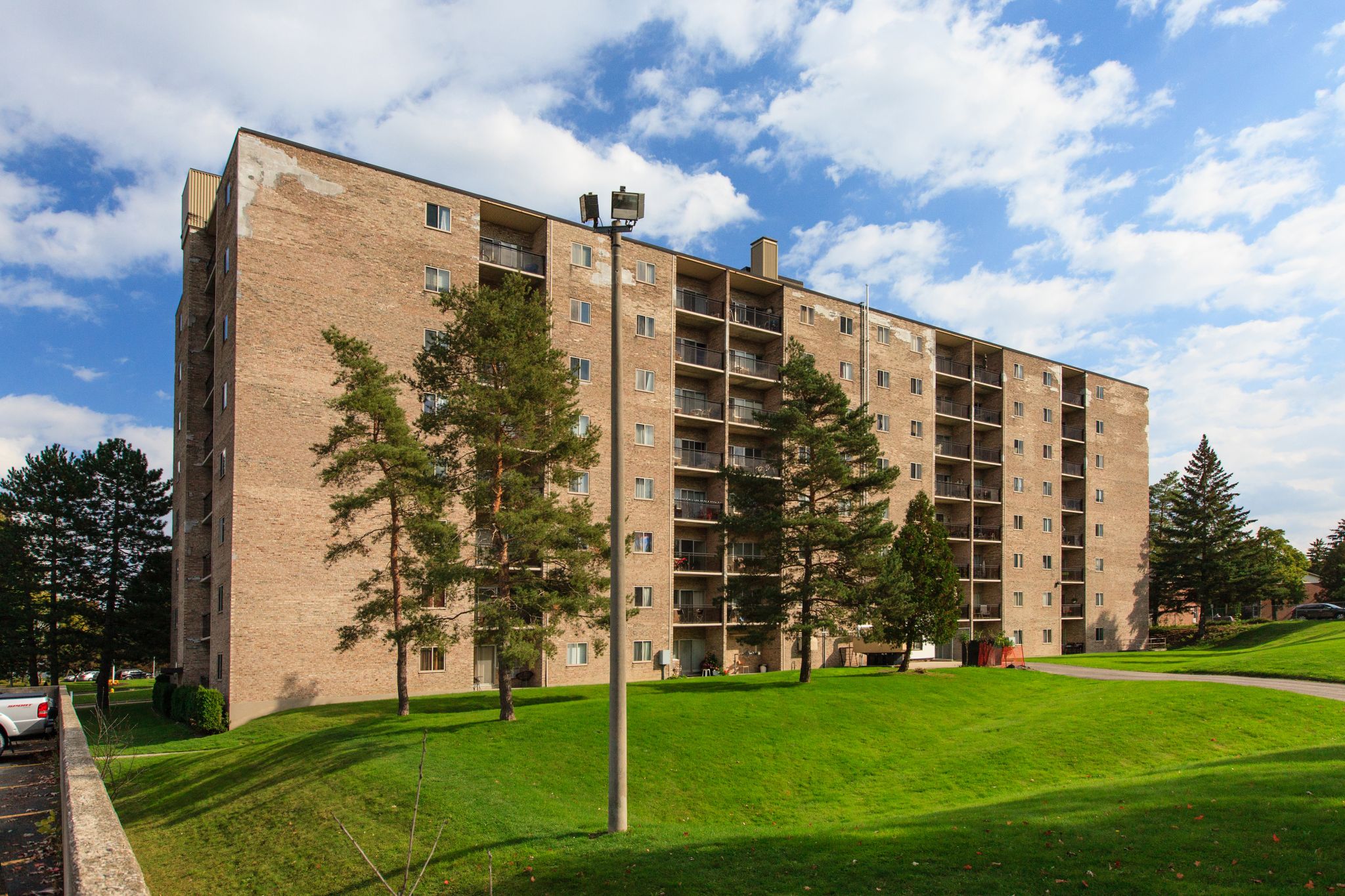
Off-site manufactured systems, like IMPs, provide a high level of fabrication quality control that more consistently performs as designed when implemented in the field and throughout the building’s life. Additionally, IMP’s single-component construction offers potential for a quicker installation time, with less trades and related construction defects.
A tighter building enclosure with right-sized energy conservation measures delivers an optimized high-performance energy building. Using IMPs, thermal continuity and performance are achieved across the entire building envelope, and the composite panel’s span capability enables attachment to steel framing with minimal thermal bridging. Additionally, the impermeable facers and joint designs mean the important air and water barrier are integrated into the panel’s design.4
A recent design trend has seen IMP panels being used as the barrier component of a rainscreen wall system. This allows architects and designers to add the functional thermal improvements required to meet the energy reduction targets without altering the aesthetic design goals.
Additional unique attributes of IMPs include:
- low air infiltration/exfiltration rates;
- high service life;
- little to no site-related construction waste;
- less trades with trained erection crews; and
- meets ‘control’ functions of a wall or roof (i.e. air, moisture, heat, light, sound) in a single component.
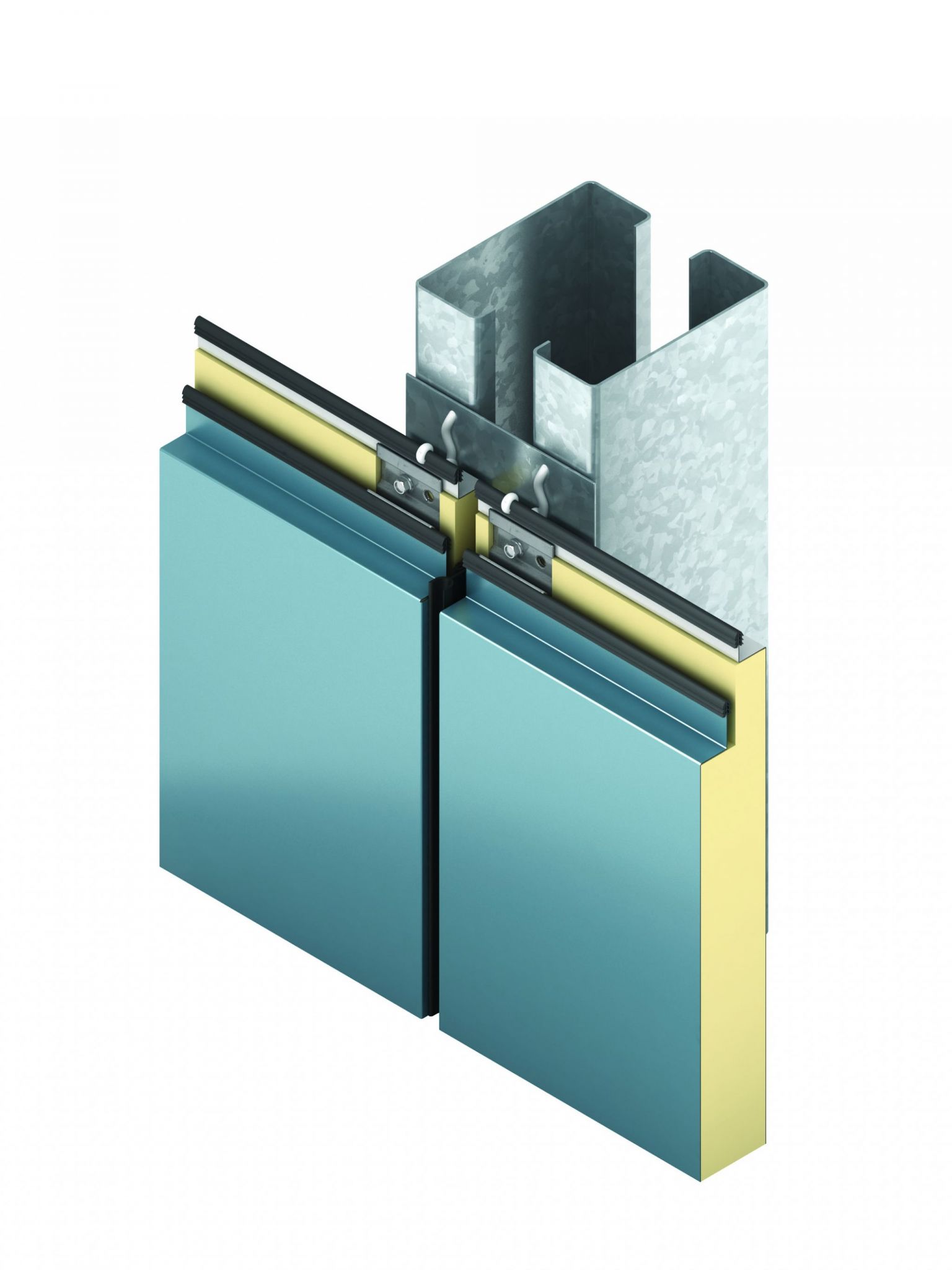
Meeting control functions with IMPs
IMP panels are available in many configurations, depending on esthetic and functional requirements. Optimal IMPs used for DERs will have interlocking joints to control air and water penetration and provide thermal continuity. This design incorporates a pressure equalization chamber that also minimizes thermal bridging with airtightness. The pressure equalization chamber is shielded from the outside by an overlap between two impermeable panel facings, thus minimizing rainwater passage into the joint driven by gravity and air pressure difference. Intercepted rainwater is effectively drained back to the exterior.
Vapour management is maintained through the panel’s fundamental nature. Inward vapour drive is controlled by the impermeable nature of the IMP exterior skin. Outward vapour control and condensation resistance is maintained through control of the condensing surface temperature. With the panel installed over a previously uninsulated building, there would be little concern of interstitial condensation in any climate zone for any commonly available panel thickness.
IMPs employ a secondary water-resistive barrier (WRB) and air barrier behind the panels, which is fundamental to the system design. The airflow control is maintained through an air barrier that is continuous with all other enclosure elements, and located on the existing structure’s exterior. All materials inboard of the control layers are considered interior of the building, and the IMP’s impermeable liner skin, combined with joint-encapsulated sealants and flashing details, provide built-in, upfront redundancies for optimized performance. The IMP functions as not only the exterior cladding, but also air/water control barrier and primary thermal resistance layer.
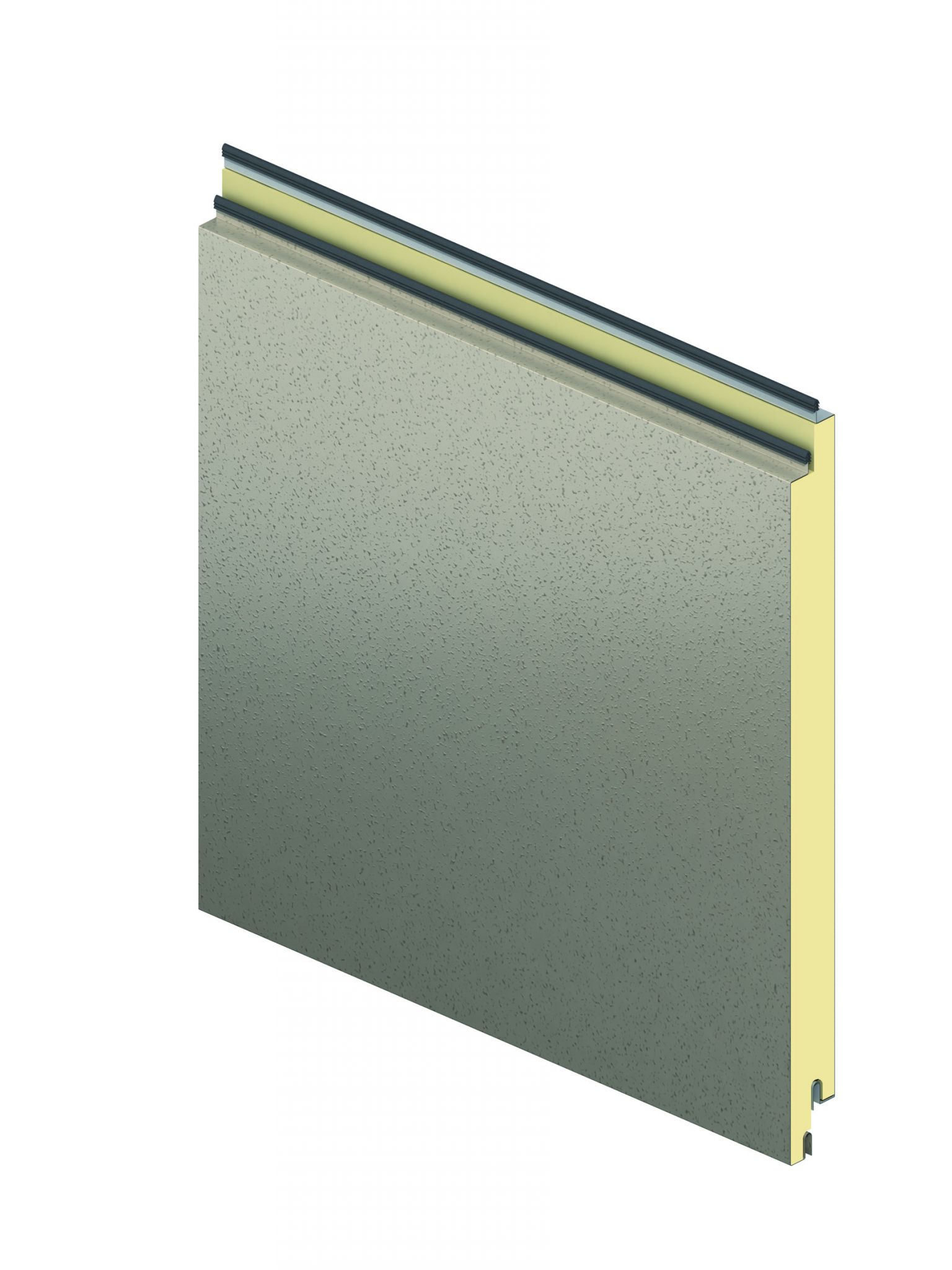
Conclusion
Any existing building project delivering 50 per cent or more of retrofit building energy efficiency improvement is considered a success. This can be reached by evaluating poor-performing buildings with an envelope first, whole-system approach, while executing high-quality renovations of the enclosure using IMPs, upgrading mechanical systems, and adding renewables where possible. With more DERs turning into success stories, Canada may find itself on the other end of the ACEEE scorecard soon.
Notes
1 For more, visit www.aceee.org/portal/national-policy/international-scorecard and www.ssti.us/wp/wp-content/uploads/2012/07/internation-energy-efficiency-scorecard.pdf. (back to top)
2 See www.unep.org/sbci/pdfs/sbci-bccsummary.pdf for more information. (back to top)
3 For more information, visit bbptoronto.ca. (back to top)
4 ASTM 1363, Thermal Performance of Building Materials and Envelope Assemblies by Means of a Hot Box Apparatus, is the standard for determining the U-value of the IMP and requires test specimen to include the effect of joint details between adjacent panels. ASTM C518, Standard Test Method for Steady-State Thermal Transmission at a Mean Temperature of 75 F; is also used for R-Value reporting. Finally, IMPs are also approved for NFPA 285: Standard Fire Test Method for Evaluation of Fire Propagation Characteristics of Exterior Non-load-bearing Wall Assemblies Containing Combustible Components. (back to top)
Paul R. Bertram Jr., CSC, FCSI, CDT, LEED AP, is the director of environment and sustainability for Kingspan Insulated Panels North America. He represents the company on various U.S. Green Building Council (USGBC), American Society of Heating, Refrigerating, and Air-conditioning Engineers (ASHRAE), ASTM, International Code Council (ICC), and National Institute of Building Science (NIBS) groups. Bertram is also a past-president of CSI. He can be contacted via e-mail at paul.bertram@kingspan.com.
Ian J. Manser, CEM, is the North American manager for Kingspan’s energy services department. A Green Associate under the Leadership in Energy and Environmental Design (LEED GA), he has more than 18 years of experience working with industry experts and design professionals in the advancement of building energy conservation and generation. Manser can be reached at ian.manser@kingspan.com.
To read “A Success Story in The Making,” click here.