Thermally improving curtain wall systems
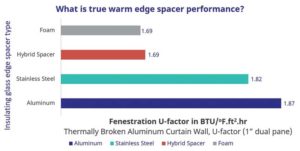
Image courtesy Technoform
Thermal bridges at attachments
Another thermal bridging area to watch is through curtain wall attachments, such as sun shades. Specifying thermally broken attachment mechanisms and requiring thermal simulations to determine the impact on assembly U-factor is important.
Thermal bridges at transitions: Beware of “by others”
Façade engineers often warn of the dangers of ignoring the interfaces of the curtain wall with adjacent building elements and the unintentional thermal bridging that can occur if not managed effectively. The widespread use of the “by others” clause can cause the responsibility for managing the important details of the transitions to be missed. Who has responsibility for tying into the adjacent systems must be specified.
Additionally, sequencing of work around the transitions should be laid out in design documents to the extent possible. This becomes apparent at the mockup stage, but this is often too late and ideally should be laid out in design documents and reviewed in the shop drawings in advance. The following are recommendations for the execution section:
- specify sufficient tolerances are provided to make the transition between curtain wall and adjacent systems possible and the contractor sequenced first leaves sufficient length of transition membranes to tie into the second assembly; and
- for complex projects, consider requiring the submission of an installation schedule covering submittals, fabrication, laboratory, and site mockups, and full construction, which lays out a road map of the work plan, especially sequencing of adjacent systems and quality checks, thereby encouraging collaboration between contractors responsible for adjacent systems.
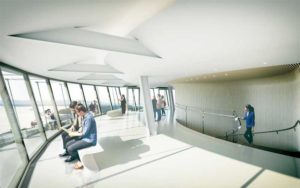
Image courtesy Olson Kundig Architects
Getting what is expected: Quality assurance
It is important to recognize field testing or commissioning of curtain wall is not a replacement for the upfront verification the design itself will meet needed performance. It is important to require submittals of laboratory test reports to validate the curtain wall being proposed meets the specified air, water, and structural performance, according to AAMA/the Window and Door Manufacturers Association (WDMA)/the Canadian Standards Association (CSA) 101/I.S. 2/A440, NAFS – North American Fenestration Standard/Specification for windows, doors and skylights, before the start of fabrication.
The same recommendation applies to requiring submission of test or simulation reports demonstrating the system meets thermal performance according to NFRC 100, providing clear assumptions for glazing infill configuration and components, including EOG details. These details must be consistent with the glass specification or strict rules for evaluation substitution risk must be applied.
These test data will demonstrate if the system performs under perfect conditions. Additional field testing for air, water, structural, and thermal performance can be specified to control for installation quality.
For larger projects, design concepts also could be required to be presented during the bid process, along with performance validation of the proposed solution, to prevent the systems with poorer performance being inadvertently substituted.
Thermal barriers
In addition to specifying the size of the thermal barrier (as identified above), it is important to include requirements to help ensure the appropriate quality of the thermal barrier material and its integration into the aluminum extrusion.