Thermally improving curtain wall systems
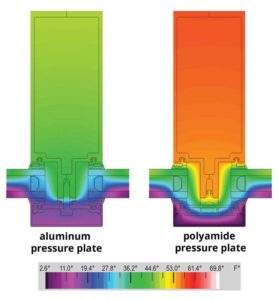
Specifying spandrel
Research has demonstrated there are two major performance issues related to opaque spandrel areas in curtain wall systems (consult Stephane Hoffman’s presentation on “Energy Code Implications for Spandrel Design; Quantifying and Mitigating the Impact of Thermal Bridging” in the Façade Tectonics Institute’s Proceedings of 2016 World Congress).
First, heat flows around the insulation in the spandrel because the position of the insulation is not aligned with the position of the thermal breaks in the metal framing. This allows heat to bypass the insulation via the aluminum frame. Even if the curtain wall is thermally broken, the framing still has less thermal resistance than insulation. Moreover, conventional 2D modelling, per NFRC 100, over-estimates the thermal performance of spandrel by up to 33 per cent because it does not capture this heat flow effectively (consult Stephane Hoffman’s presentation on “Energy Code Implications for Spandrel Design; Quantifying and Mitigating the Impact of Thermal Bridging” in the Façade Tectonics Institute’s Proceedings of 2016 World Congress).
Second, heat flows unhindered to and from the transparent areas flanking the spandrel through long, continuous vertical mullions. Current simulation methods, including NFRC 100, do not include the impact of thermal bridging to transparent areas, which also causes an over-estimation of thermal performance. Research shows thermal bridging to flanking modules can reduce performance by up to 30 per cent (consult Stephane Hoffman’s presentation on “Energy Code Implications for Spandrel Design; Quantifying and Mitigating the Impact of Thermal Bridging” in the Façade Tectonics Institute’s Proceedings of 2016 World Congress).
In fact, not only do spandrel areas have worse performance than opaque mass walls, the standard 2D simulations (such as NFRC 100) used to determine U-factor over-estimate thermal performance. This means curtain wall performance is actually worse than expected unless these heat transfer mechanisms are accounted for and controlled.
To address heat flow around the spandrel insulation, the insulation ideally should be aligned with the glazing and thermal barrier. One example attempting to do this uses a vacuum insulating panel (VIP) within an IGU in the spandrel area (Figure 10). It needs to be accompanied by a high-performance warm-edge spacer to reduce thermal bridging at the edges and wide thermal barriers in the curtain wall framing, which presents best-case spandrel performance (consult Stephane Hoffman’s presentation on “Energy Code Implications for Spandrel Design; Quantifying and Mitigating the Impact of Thermal Bridging” in the Façade Tectonics Institute’s Proceedings of 2016 World Congress).
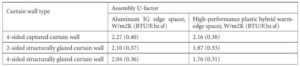
Image courtesy Wausau Window and Wall Systems
It is recommended specifications for spandrel assemblies, where the spandrel height to floor height is more than 40 per cent, require 3D modelling to figure out thermal performance or physical guarded hot box testing according to NFRC 100 to determine performance. In the absence of both, it is best to use the 2D NFRC 100 calculated U-factor increased by 30 per cent (referenced from Yvon Chiasson’s oral presentation on “Building Material: Performance and Geometry Driving Expansion of the Façade Materials Palette” at a Façade Tectonics Institute forum in Toronto in May 2019).
Research shows that in spandrel to floor heights of less than 40 per cent, the impact of the spandrel will not be significantly different than of the transparent areas because heat loss at the edge of frame significantly impacts the value of the insulation (consult Stephane Hoffman’s presentation on “Energy Code Implications for Spandrel Design; Quantifying and Mitigating the Impact of Thermal Bridging” in the Façade Tectonics Institute’s Proceedings of 2016 World Congress).
To address the degradation in performance due to thermal bridging to flanking systems, more creativity is required, and may change the look of the curtain wall. Various strategies have been discussed within the façade design community including:
- reducing the number of vertical members;
- increasing the width of spandrel panels and staggering them from the vision glazing above;
- using a double, or further thermally improved, stack joint in unitized curtain wall;
- placing spandrel insulation further to the outside (into the glazing pocket) to cover the shoulder of the interior framing member; or
- running the long mullions horizontally rather than vertically (referenced from Yvon Chiasson’s oral presentation on “Building Material: Performance and Geometry Driving Expansion of the Façade Materials Palette” at a Façade Tectonics Institute forum in Toronto in May 2019).
This last option would certainly change the esthetics of the curtain wall, but the verticals would no longer run continuously through the glazed and spandrel areas.
As an additional resource, the Building Envelope Thermal Bridging Guide (BETB Guide) commissioned by B.C. Hydro and built on the American Society of Heating, Refrigerating and Air-Conditioning Engineers (ASHRAE) Research Project Report RP 1365, Thermal Performance of Buildings Envelope Details for Mid and High Rise Buildings, provides a large catalogue of many different wall assemblies, including spandrel panels, ranging from poor to high-performance.
The BETB Guide provides performance values derived from 3D thermal simulations for each assembly, which accounts for thermal bridging effects, and which can be referenced for design and specification purposes.