Thermally improving curtain wall systems
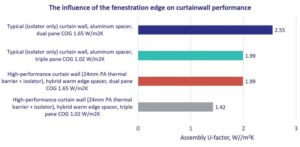
Image courtesy Technoform
It is, therefore, important to specify more than just “warm-edge” spacer in project specifications; otherwise, what ends up installed in the project, may not meet the overall thermal performance requirements for the system. Ideally, the type of warm-edge spacer with material specifics should be specified. This not only ensures the thermal performance is consistent with delivering the performance of the assembly, but also the spacer is appropriate to the application. For example, some edge spacer systems, while having good thermal performance, are more suited for residential-type applications and are not appropriate for use with dual-seal polyisobutylene/silicone edge seal systems or in structurally glazed applications.
It is important to require insulating glass certification from a reputable certification program, such as through the joint Insulating Glass Certification Council (IGCC)/Insulating Glass Manufacturers Alliance (IGCC/IGMA) program or the Insulating Glass Manufacturers Association of Canada (IGMAC) program, which is part of the Fenestration and Glazing Industry Alliance (FGIA). It is also important to require submittals of ASTM E2190, Standard Specification for Insulating Glass Unit Performance and Evaluation, test reports for the spacer and sealant system that are proposed for the project. These reports must demonstrate high performance for durability and gas retention. The most stringent certification programs require test units to be made on the production line in the presence of an auditor annually and then sent for testing according to ASTM E2190.
Another conclusion to be drawn from the data in Figure 8 is a PHSS spacer results in the same thermal performance improvement as non-metal types. The high desiccant carrying capacity box profile and thin solid stainless steel envelope around the back and sides of the hybrid spacer, delivers the same benchmark durability as the stainless steel and aluminum box spacer with the thermal performance of non-metal spacer. In recognition of this, leading insulating glass certification bodies allow the substitution of hybrid box spacers for stainless steel without additional testing.
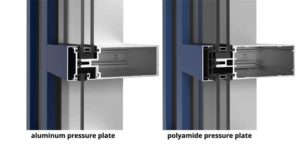
Images courtesy YKK AP America Inc.
Figure 9 shows images of the structural glazing in the newly renovated Space Needle, which required the use of a high-performance hybrid warm-edge spacer to meet the stringent Seattle energy codes. The Atmos level’s (observation deck) classic reverse curtain wall had to be preserved. Therefore, enhanced performance at EOG was needed to control the flow of heat from the large external mullion (acting as a heat sink) to the inside. On the Loupe (restaurant) level, a high-performance warm-edge hybrid box spacer was specified again for the oversized IGUs with unsupported edges to block heat flow at the edges. The hybrid system was called out in the specification because of the thermal performance and the rigidity needed to manage the torsional stresses at the head and sill edge support conditions.
Condensation resistance
It is especially true in curtain wall systems U-factor and the condensation resistance are not correlated well. As a result, one cannot assume a system with a low U-factor will deliver the expected condensation resistance. Improving the U-factor of a curtain wall system means reducing the amount of metal framing and increasing the use of engineered plastic thermal barriers, yet condensation resistance can improve with increasing metal mass on the interior mullion. As a result, it is important to specify condensation resistance along with U-factor performance.
There are several measures of condensation resistance (read the article, “Effectively Specifying Fenestration; Managing thermal, structural, and durability performance,” published in the November 2017 issue of The Construction Specifier). The most common are condensation resistance (CR), as defined by NFRC—a calculated value—and condensation resistance factor (CRF), as defined by the American Architectural Manufacturers Association’s (AAMA) 1503, Thermal Transmittance and Condensation Resistance of Windows, Doors and Glazed Wall Sections, an FGIA standard, and based on measured values. Even though they share the same scale from zero to 100, the systems are not the same and cannot be compared. It is important to be clear on which metric is specified, and ensure submittals provided to demonstrate compliance are consistent with the chosen performance system.