Thermally improving curtain wall systems
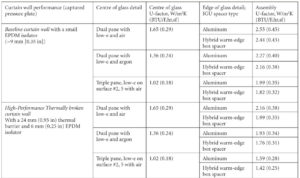
Image courtesy Tubelite Inc.
Even when specifying assembly U-factor requirements, it is still important to differentiate between thermally improved and thermally broken curtain wall. Experts recommend a best practice of specifying the minimum size of the thermal break in addition to the U-factor requirement. For curtain wall, the recommendation is to require a polyamide thermal barrier with a minimum width of 19 mm (¾ in.)—and wider if higher performance is needed.
Figure 2 shows whole unit (assembly) U-factors (NFRC size) for:
- a curtain wall system with a relatively small ethylene propylene diene monomer (EPDM) thermal isolator; and
- a higher performance thermally broken curtain wall system with 24 mm (945 mils) dual polyamide thermal barriers along with a 6-mm (¼-in.) EPDM isolator for a range of COG U-factors and insulating glass edge spacer types (Figure 3).
Figure 4 displays a subset of the data in Figure 1 to illustrate the greater impact of improving frame and EOG performance on assembly U-factor. In this example, there are two ways to achieving an assembly U-factor of 1.99 W/m2K (0.35 BTU/F.hr.sf). In the lower performance curtain wall, triple-pane glazing is required. However, by choosing a high-performance thermally broken curtain wall and a high-performance warm-edge spacer in the IGU, only a simple, low-cost, air-filled, dual-pane, low-e IGU is needed to meet the same performance. Improving the frame and EOG first allows for greater flexibility in choice of the COG, and provides a more balanced approach.
Pressure plates
The thermal performance of curtain wall systems also can be improved by replacing the typical aluminum pressure plate with a non-metal version made from glass-reinforced polyamide (Figure 5) or fibreglass. These are widely available from multiple manufacturers in a large range of sizes. The addition of a polyamide pressure plate can decrease the system U-factor substantially. Figure 6 shows the temperature profiles for a typical thermally improved curtain wall containing a small thermal isolator with an aluminum and polyamide pressure plate, respectively.
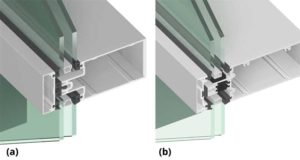
Image courtesy Tubelite Inc.
Using a typical dual-pane, low-e, argon-filled IGU as the glazing infill, the polyamide pressure plate brings the U-factor of a thermally improved curtain wall system down from a high of 2.33 W/m2K (0.41 BTU/F.hr.sf) to 1.87 W/m2K (0.33 BTU/F.hr.sf)—an improvement of 20 per cent. Using a non-metal pressure plate in combination with wider thermal barriers within the mullions can improve thermal performance even more. The curtain wall system installed at the Georgia College of Law building in Atlanta, Ga., incorporates polyamide pressure plates in combination with wide polyamide thermal barriers that were specified to support achievement of the U.S. Green Building Council’s (USGBC’s) Leadership in Energy and Environmental Design (LEED) Silver certification.
Structural silicone glazing
Silicone structurally glazed curtain wall systems typically have better thermal performance than their captured counterparts—all other things being equal. This is due to the elimination of thermal bridging associated with metal pressure plates and related fasteners. Figure 7 compares the performance of a captured curtain wall, a two-sided structurally glazed curtain wall, and a four-sided structurally glazed system. The four-sided structurally glazed system has a U-factor 10 to 18 per cent lower than the fully captured system using aluminum pressure plates, depending on the insulating glass edge spacer used. The data in Figure 7 also demonstrates the relative impact of using a high-performance warm-edge spacer in the IGU instead of a highly conductive aluminum spacer.
In a typical captured curtain wall system, a high-performance warm-edge spacer reduces the assembly U-factor by 0.11 to 0.17 W/m2K (0.02 to 0.03 BTU/F.hr.sf) or ~5 to 10 per cent, but the impact of insulating glass edge spacer is even higher in a structurally glazed system. This is because, in the absence of an external frame, the major conduction path from inside to outside is directly through the edge of the glass. Thus, the performance of EOG is even more important in structurally glazed systems. In the example in Figure 7, a high-performance warm-edge spacer reduces the U-factor of the structurally glazed system by 14 per cent or 0.28 W/m2K (0.05 BTU/F.hr.sf). A significant amount, given the performance enhancements needed to meet more stringent code requirements with high glazing areas.
Specifying the edge of glass
Unfortunately, unlike “thermally broken” and “thermally improved,” the performance of “warm-edge” spacer in North America is not well defined. A warm-edge spacer is assumed to be any spacer with better thermal performance than the aluminum box type, which spans a wide range of performance. Figure 8 shows the assembly U-factors of a curtain wall with three warm-edge spacer types: Stainless-steel box spacer, plastic hybrid stainless steel (PHSS or hybrid) box spacer, and a flexible foam spacer—compared to using an aluminum spacer. The stainless-steel box spacer results in only slightly better performance than the aluminum box spacer, yet it is still referred to as warm-edge.