Thermally improving curtain wall systems
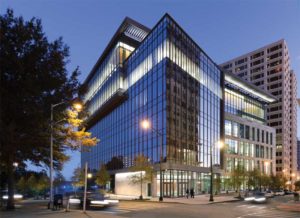
By Helen Sanders, PhD
Curtain walls are ubiquitous worldwide, delivering sleek, easy to install, and highly glazed building façades. Curtain wall systems provide excellent access to daylight and views that are desired by building owners and occupants for health and productivity. However, the increasing stringency of building codes has created a conflict with delivering highly glazed buildings because glazed areas are known to be less thermally efficient than opaque walls.
Curtain wall systems present an even larger conflict because their opaque, spandrel areas cannot easily match the thermal performance of an opaque wall assembly (concrete, steel stud wall, etc.). For a curtain wall system to achieve comparable performance to a mass wall with the same window-to-wall ratio, the thermal performance of the curtain wall’s transparent areas must be substantially greater than in a mass wall system to make up for the poorer opaque wall performance. Additionally, current thermal modelling of spandrel areas over-estimates the thermal performance, leading to gaps between expected and delivered performance.
Over the years, the industry has relied heavily on increasing performance of low-emissivity (low-e) coatings to improve curtain wall U-factors (thermal transmittance). However, the centre of glass (COG) U-factor is only part of the picture.
Focusing on preventing heat flow through the COG only, rather than considering the assembly as a whole, is the thermal equivalent of damming a river at its centre, yet forgetting to block water flow all the way to its banks. In the case of the river, the water just flows around the edges of the dam and the flow is not stemmed. Similarly, in the case of the curtain wall, the energy still flows around its perimeter—through the frame and edge of glass (EOG)—even if the COG conductance is low (Figure 1).
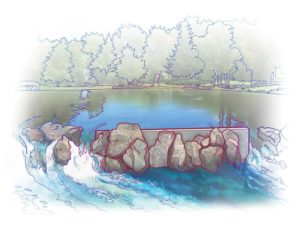
Image courtesy Technoform
Managing thermal bridging at interfaces and connection points is critical to delivering expected performance. Specifications can be used effectively to establish performance expectations and ensuring these are managed and delivered through the construction process.
Curtain walls are complex systems, and need to fulfil not just thermal requirements, but also those for air infiltration/exfiltration, water management, and structural performance, to name just a few. If not specified completely, including appropriate verification of design and installation performance, a significant gap between expected and as-built performance can occur.
The required high thermal performance can be achieved in curtain wall systems with enough focus on upfront design details, management of interfaces, and the execution phase.
Balanced design: Specifying the edge
The thermal transmittance (U-factor) of fenestration comprises the area weighted average of the thermal transmittances of the frame, EOG, and COG. The frame consists of the opaque elements holding the glass. EOG comprises the perimeter area of the insulating glass unit (IGU) containing the spacer and sealants, and COG refers to the vision area of the glazing.
Due to the area weighting, in curtain wall with smaller openings and more framing members, the frame and edge seal thermal transmittance dominate the overall U-factor compared to designs with larger openings where the glass area-to-metal perimeter ratio is higher. The National Fenestration Rating Council (NFRC) uses standard sizes for different fenestration types (e.g. fixed window, awning, skylight, etc.) to allow comparisons between different systems of the same fenestration type. When specifying the U-factor performance of curtain wall, it is important to specify the whole assembly U-factor and what size the required U-factor target is based on: NFRC or project size.
According to NFRC 100, Procedure for Determining Fenestration Product U-factors, thermally improved performance for aluminum fenestration requires a small, low-conductivity thermal isolator of minimum 1.6 mm (63 mils) between interior and exterior framing elements, whereas the thermally broken performance requires a significantly wider thermal barrier of at least 5.3 mm (210 mils). Thermally broken systems, therefore, deliver higher thermal performance than thermally improved systems.