Thermal breaks prevent heat loss
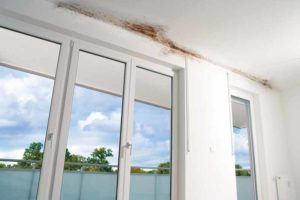
STBs eliminate energy loss
An STB is a fabricated longitudinal assembly about as wide as the exterior building wall and as high as the floor slab. It creates a structural insulated foam break between the interior floor and the exterior balcony to minimize thermal conductivity between the two masses, while optimizing loadbearing capacity.
STBs for concrete construction contain engineered stainless steel rebar for casting into the concrete slab on the interior side and the concrete balcony on the exterior side, yielding structural strength equivalent to that of conventional reinforced concrete extensions of floor slabs.
STBs for steel construction are equipped with flanges and bolts for fastening to steel floor joists on the interior side. On the exterior side, they are fastened to cantilevered balcony supports or to other steel connections, such as canopies, signage, sunshades, rainscreens, roof-mounted equipment, and fencing.
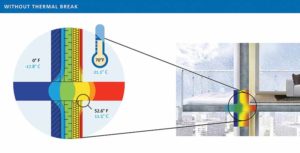
In this author’s experience, when compared to non-insulated connections, STB achieves a 90 per cent reduction in thermal conductivity in the connection area for standard loadbearing scenarios. This translates into average annual reductions of 14 per cent in energy use and carbon footprint for the overall building.
The reduction in energy required to heat the building also allows corresponding reductions in heating system size/capacity, resulting in savings on capital equipment and ongoing operation and maintenance of mechanical systems.
Lastly, thermally isolating balconies using STBs improves comfort for occupants and value for developers by increasing the warmth and usability of interior floor space.
STBs help comply with tighter codes
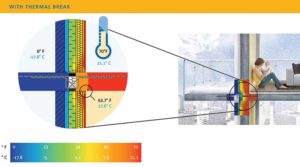
STBs help buildings comply with tightening building codes mandating higher energy efficiency and ci.
The American National Standards Institute/American Society of Heating, Refrigerating and Air Conditioning Engineers/Illuminating Engineering Society (ANSI/ASHRAE/IES) 90.1, Energy Standard for Buildings Except Low-rise Residential Buildings, was revised in 2016 to require energy-efficiency modelling for uninsulated assemblies in building envelopes, including balconies and perimeter edges of floor slabs and parapets.
The 2016 update of ASHRAE 90.1 offers three paths to compliance: the prescriptive method, the energy cost budget (ECB) method, and the performance rating method (PRM).
The prescriptive method specifies details of building elements such as:
- ci;
- specific R-values for components depending on construction type and geographic region; and
- glass-to-opaque-wall ratios limited to 40 per cent of wall surface.
The ECB method is a performance-based system for determining compliance and is available as a free web program. ECB compares two models of a building: the proposed building as designed and the budget building design (a structure of the same size and constructed to minimum ANSI/ASHRAE/IES 90.1 prescriptive requirements), calculating costs and identifying areas needing change. The program simulates the building’s proposed energy costs, comparing them with those of the code-compliant structure and indicating whether the proposed costs are less than or equal to the baseline, and thus compliant. ECB can also summarize a building’s energy performance as a percentage of the ANSI/ASHRAE/IES 90.1 standards.
In PRM, the project team applies software modelling tools to prove the building will perform at least as well as under the prescriptive requirements with an equal or lower annual energy cost. PRM is also used for ‘beyond code’ programs such as Leadership in Energy and Environmental Design (LEED) or the International Green Construction Code (IgCC).