Theory of a self-drying roof
Test hut and lab testing

Modelling is a good tool to help designers predict how a scenario can play out. However, to ensure the model is as realistic as possible, infield testing data should be conducted, and inputted into the model. To determine if the self-drying roof is viable for a cold climate, a third-party test hut and a conditioned room was utilized to test components of the proposed system. The composition of the roof included two-ply modified bitumen roof membrane, two layers of 76-mm (3-in.) vapour permeable mineral wool insulation, smart membrane (permeability dependent on relative humidity [RH]), and a metal deck with holes drilled in to simulate screw holes. The test huts’ interior conditions were typical to operational interior conditions of 22 C (72 F) +/– 3 C (37 F) and 30 per cent RH +/– five per cent, whereas the exterior conditions were the actual climatic conditions in Waterloo, Ont., from June 6 to 10, 2016. To obtain the temperature, humidity, and moisture profiles, sensors were installed horizontally and vertically throughout the test roof enclosure. Moisture was introduced into the roof enclosure at the interface between the two mineral wool roof insulation via a simulated leak of 75 ml (0.15 oz) scheduled twice a day for five days (total of 750 ml [26 oz]). The 75-ml amount was chosen for testing and the intent was to see if the moisture could be removed in a reasonable amount of time (rhe test team plans to validate the drying rate and input that into the model so the amount of moisture in the model could be adjusted accordingly). Operational data obtained from the test roof enclosure’s temperature, humidity, and moisture sensors were then plotted. This would be used for the validation of the hygrothermal model.
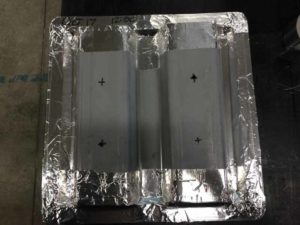
Since material property data required for the self-drying roof enclosure was unavailable in a WUFI software database, relevant testing had to be completed on the smart membrane and the fluted metal roof deck. ASTM E96, Standard Test Methods for Water Vapour Transmission of Materials, was used to determine the vapour permeance of both the membrane and deck. Vapour permeance data was obtained for smart membrane by utilizing ASTM E96’s dry cup and wet cup methods. The vapour permeance data for the fluted metal deck was obtained by just using the dry cup method. However, to simulate in-situ conditions, several samples were created introducing side laps, end laps, and screw holes. The smart membrane had a wide vapour permeable performance ranging from 43 ng/pa.s.m2 (0.75 perms) to 550 ng/pa.s.m2 (9.65 perms) based on low and high RH. Surprisingly, the metal deck had a range of 14 ng/pa.s.m2 (0.25 perms) for side lap joints and an average of 68 ng/pa.s.m2 (1.2 perms) for end lap joints and screw holes in the fluted metal roof deck. Data obtained from these lab tests were added into the WUFI database to develop a validation model.
Validation and North American hygrothermal models
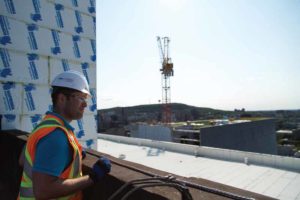
Photo courtesy Soprema
Accurate model predictions can be achieved in WUFI by including data inputs from actual laboratory testing. The WUFI validation model was created using the identical construction materials/orientation and was modified to mimic the data from the test hut roof enclosure. Many hours were spent developing various iterations to mimic the in-situ data from the test hut. However, the final validation model’s drying was within 0.5 per cent of the drying time of the actual test hut roof enclosure. The test hut roof assembly had a drying period of 816 hours (34 days) and the WUFI validation model had a drying period of 812 hours (33.8). It should be noted the test hut roof enclosure’s leak was between the two mineral wool boards whereas the validation model’s leak was located at the interface of the roof membrane and mineral wool board.
Seventy-eight hygrothermal models were created in WUFI, covering 13 climatic regional zones across North America, with three colour roof membranes (white, grey, and black). All modelled roof assemblies comprised a roof membrane, mineral wool thermal insulation, smart membrane, and metal deck. The thickness of the mineral wool insulation was dictated by the thermal requirements of the climatic regional zone for which the roof enclosure was being modelled. Both active and passive ventilation were introduced in the metal deck flutes (half the models) to minimize the diffusion of moisture into and out of the roofing assembly. The WUFI model simulation began on October 1, 2016, and continued for 8760 hours, ending on October 1, 2017. The 750-ml water leak was introduced on April 1, 2017, as one wetting event occurring at the interface between the roof membrane and the mineral wool insulation. The drying period for the 78 models was plotted and a performs/caution/warning designation was identified for each scenario. A successful self-drying roof was dependent on two criteria:
- the insulation did not increase in moisture content of 0.8 per cent by volume; and
- a drying period longer than 2880 hours.