Theory of a self-drying roof
by Rockford Boyer
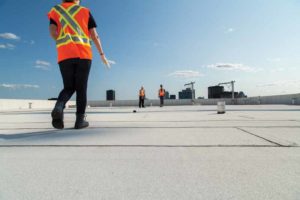
An effective method for a contractor, designer, or manufacturer to visit the inside of a court room is for the building enclosure to develop a leak! A 2011 article in the Journal of the American Institute of Architects revealed 40 per cent of issues are caused by moisture. With water vapour-related issues making up almost half of the problems, 70 per cent of the litigations interviewed had one issue in common—the roof.
The moisture-related roof issues discussed in the journal could be broken down into the following causes:
- 60 to 70 per cent was attributed to poor construction methods and workmanship;
- 20 to 25 per cent was the cause of poor design; and
- the remaining 10 per cent was due to material failure.
The roof enclosure is one of the most important components of the building. However, the average cost for the roof is approximately two per cent of the overall construction cost, as per the article mentioned above. Even if the overall roof cost increases, the chances for a leak-free assembly will almost be impossible if it is badly designed, have poor construction techniques, and lack third-party inspections.
Moisture ingress at the roof level has the potential to negatively affect the durability and resiliency of the enclosure, leading to an increase in operational and maintenance costs. Roof failures and wet roofs also have a large impact on the environment, such as the landfilling of waste materials and increasing carbon emissions with the manufacture and transportation of new products and increased heat flow.
Moisture ingress into the roof enclosure typically occurs through three conditions:
- physical bulk water entry;
- roofing material moisture content (construction moisture and through interior vapour diffusion) and;
- air leakage.
Bulk water leakage through the roofing membrane can be caused by commonly occurring damages from poor workmanship, such as blistering, incomplete laps, membrane punctures, wrinkles, splitting, abuse, and neglect, and inadequate penetration seals and flashing. Roofing materials, specifically moisture-sensitive ones, can become damp or saturated when installed or stored under wet conditions. The installation of an incomplete air and vapour membrane on the metal deck has the potential to allow moist air/vapour to enter the roofing enclosure through the mechanisms of diffusion and convection. Under certain conditions, the difference in pressures can help moisture-laden air and vapour to enter the roof enclosure and condense on the underside of the membrane. Since current construction practices allow the moisture to enter the enclosure, the introduction of a ‘smart’ roof design to promote self-drying will help increase the roof’s durability, resiliency, and thermal performance.
Thermodynamic solution
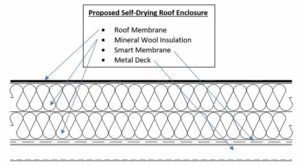
Images © Rockford Boyer
To develop a better understanding of how a roof works under specific environmental loads, an understanding of the second law of thermodynamics is necessary. In basic terms, the law says energy shall maintain a state of thermodynamic equilibrium—hot to cold, high pressure to low, and high to low vapour. In a cold climate, the roof will be hotter than the interior space under summer conditions. Therefore, the heat flow will be from hot to cold (exterior to interior). If a leak occurs at the roof membrane level during the summer (cooling season), the moisture will try to migrate from a high concentration area to one of low concentration, such as the roof enclosure to the occupied space below. The moisture will not be able to equalize as a vapour retarder would generally be located on the warm side of the insulation and does not allow for effective moisture transport to an area of lower concentration.
The conditions during the heating season are reversed as the heat from the interior occupied space will want to migrate up through the roof enclosure to the exterior colder temperature. Moisture will follow the same path as the heat during the winter months (hot to cold). Due to the vapour pressure and cold temperatures, if the vapour retarder is not continuous, there will be a possibility of condensation at the underside of the roof membrane.
An incomplete or defective roof membrane/vapour retarder will allow air, vapour, and moisture to enter the roof enclosure and migrate freely based on the interior and exterior conditions, thereby negatively impacting the roof’s performance and durability. The enclosure must be allowed to achieve equilibrium to increase its resiliency.
New construction materials can help roof enclosures equalize (dry) when wet—two such technologies are vapour permeable thermal insulation and variable vapour permeable smart vapour retarder (Figure 1). Drying to the interior can theoretically be achieved by replacing the standard non-vapour permeable insulation (traditionally polyisocyanurate [ISO]) with vapour permeable (mineral wool) insulation, and using a variable vapour permeable smart vapour retarder instead of a standard vapour retarder. Inward drying at the vapour retarder interface of the roof enclosure is recommended as there needs to be an ultra-low vapour permeable membrane protecting the components and space below.
The intent of using two vapour ‘open’ materials is to efficiently diffuse and dry the moisture from the area of high concentration (leak) to the area of low concentration (interior occupied space) by using the second law of thermodynamics and energy from the sun.
Theoretically, during the cooling season the moisture/vapour will diffuse through the vapour permeable insulation (via the variable vapour permeable smart membrane) and to the interior where the moisture could be removed by means of venting. The energy from the sun (membrane colour) will impact the drying period as the amount of radiation absorbed will dictate the temperature gradient through the roof enclosure. During heating days, the roles will be reversed due to the temperature’s gradients (i.e. inside to outside). While this scenario makes sense in theory, can it work in practice and possibly be modelled to demonstrate the ‘in-situ’ performance?