The Theory of R-value Relativity: The impact of thermal conductivity on building enclosure durability
Theory vs. real world
Although lab tests can help determine the individual characteristics of a product, these characteristics can drastically change when installed or tested as a system. In turning lab test theories into understandable or real project situations, a well-known hygrothermal modeling software program, WUFI-ORNL/IBP, can assess the combined heat and moisture transfer in building components based on building type and local interior and exterior environments. In WUFI-ORNL/IBP, a user generates personalized assembly constructions from a wide range of default materials, climates, and conditions to predict their in-situ performance.
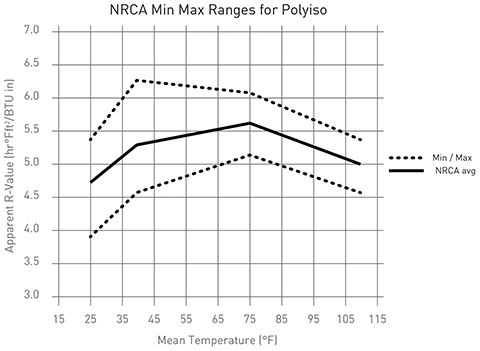
Sometimes, data associated with generic or default materials can be inaccurate, assumed, estimated, or missing completely. This is the case with one of the generic polyisocyanurate (polyiso) materials located in the WUFI-ORNL/IBP database for North America. Figure 2 references the generic default material located in the North American database, whereas Figure 3 is derived from out-of-scope testing and resembles actual in-situ temperatures. The two graphs show a discrepancy between the temperature versus the R-value for the default value, as well as the actual tested value for a similar insulation material type.
The objective of this comparison is not to discredit the software program, but rather to educate users on encouraging manufacturers to input actual test data into the software database. Product manufacturers must take responsibility in providing accurate hygrothermal data to building professionals to ensure designs are as realistic as possible. Figure 4 depicts a realistic thermal prediction of an ASHRAE-compliant wall with the use of three common continuous insulation (ci) materials.
Thermal conductivity and building durability
How can R-value affect the durability of a building assembly? Primarily, it does so based on the condensation potential of the condensing plane (in the case of Figure 4, this would be the sheathing board). A higher potential for condensation can occur when low temperatures, high humidity, and low-permeable materials are present within a building assembly.
Air leakage, which ex-filtrates from the interior to the exterior, also has a negative impact on interstitial condensation. This is especially true if non-permeable components are used. Predicted maximum temperature swings for extruded polystyrene (XPS) and mineral wool insulation types are 3 C (7 F)—between 7 and 4 C (46 and 39 F)—whereas, polyiso has a maximum fluctuation of 6 C (11 F)—between 6 and 0 C (43 and 32 F).
When calculating the potential condensation hours for a given time period, one should utilize temperature-dynamic R-values, rather than static R-values. Otherwise, it is easy to severely underestimate the hours of condensation predicted, which can lead to such future durability issues as deterioration and mould.
However, it is not detrimental to the building assembly when a small amount of interstitial condensation occurs within it, as long as the drying outweighs the wetting. Research conducted several institutions, such as National Research of Canada (NRC), the British Columbia Institute of Technology (BCIT), and BSCI, demonstrated the drying potential of insulated sheathing when water ingresses or occurs behind/between a building’s insulated sheathing and structural sheathing.1 In addition, BCIT research revealed higher permeable insulated sheathing dries 50 per cent sooner than non-permeable insulated sheathing.
Another solution that minimizes moisture damage to building assembly components––even when using non-permeable insulation––is locating all insulation outboard of the air-, moisture- and vapour-control layers. Theoretically, this ensures the dewpoint occurs in the insulated sheathing material (i.e. sound building-science principles result in durable building assemblies). However, resilience is ensured when materials are placed in locations that allow for drying in both directions, minimize deformation, and provide resistance to moisture and fire damage. This even applies with unexpected failures and improper detailing.