The sustainability aspect of net-zero energy-ready build
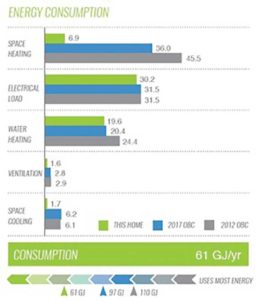
Further modelling revealed additional measures could have been taken to further reduce 61 GJ of energy consumption in the NZER houses, including the inclusion of triple-glazed windows and an air source heat pump hot water tank. These two measures would have reduced the annual energy consumption by another 10 to 15 GJ a year. At the time, both were expensive technologies to implement, but thankfully these costs have now come down and such measures can be implemented on projects to further reduce energy consumption.
Net-zero house and sustainability failures
Before getting into how this house failed from a sustainability perspective, one must think about the definition of sustainability. Sustainability consists of fulfilling the needs of the current generations without compromising the needs of future generations. The NZER house constructed for the author considered operational carbon; however, at the time, an analysis of the embodied carbon was not completed. For a building to be truly sustainable, both the operational and embodied carbon must be low to ensure a limited negative impact on the environment. The three materials driving a high embodied carbon value for the NZER house include concrete, the brick cladding, and extruded polystyrene (XPS) insulation (Figure 2).
To reduce the embodied carbon of concrete, there are alternative mixes available such as supplementary cementing materials (SCMs). The SCMs replace a portion of the Portland cement, which improves the environmental footprint of concrete by a reduction in the greenhouse gas emissions (GHG) and air pollutants. Often, SCMs are byproducts from other industrial processes, so by using these materials in concrete mixes, materials are diverted from landfills. Bricks are also improving their environmental footprint with the introduction of manufactured bricks which do not require high temperature firing and limit the use of materials, such as Portland cement, in the manufacturing process. If low-carbon bricks are not available, alternative cladding options include fibre cement panels, or carbon capturing products, such as wood or wood composite claddings (Figure 3).
HFC versus GPS insulation
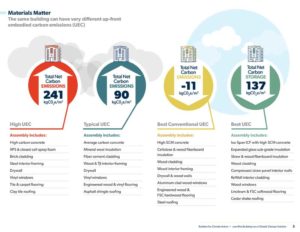
The graphic in Figure 2 could be referencing the old formulation of XPS foam insulation, however, is the new formulation any better and what is the difference between the two formulations? The old formulation of XPS is manufactured with HFC–134a as the blowing agent, whereas the new formulation is manufactured without the HFC–134a, or with a blend which limits its amount. The product received depends on the location.
As of January 2021, Environment and Climate Change Canada (ECCC) prohibit any individual to manufacture a foam product which contains a hydrofluorocarbon (HFC) blowing agent. In the U.S., the Environmental Protection Agency (EPA) stated that in 2015, the use of HFC–134a would end January 2021; however, it later retracted the mandate in favour of Proposed Rule 23, which was implemented under a program called Significant New Alternatives Policy (SNAP).1
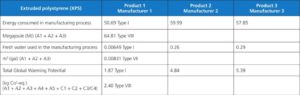
The EPA will accept the use of HFC–134a in three specific “blends.” It should be noted only one XPS manufacturer was leading the charge against the revision, while other XPS manufacturers agreed they could produce a product without HFC–134a. In summary, any XPS product manufactured and sold in Canada cannot contain HFC–134a, while certain states in the U.S. allow XPS to use a blend of HFC–134a, while other states require XPS insulation without it.
So, how much better is the new XPS formulation than the old formulation? How does a graphite expanded polystyrene rigid insulation (GPS) compare to XPS, and could it replace XPS foam insulation to achieve a sustainable solution for NZER or NZE housing? Often, individuals looking to build sustainable houses select expanded polystyrene (EPS) because its blowing agent, pentane, has a very low global warming potential (GWP). GPS is simply EPS insulation that has been infused with graphite to enhance the product’s thermal resistance. The new formulation of XPS insulation reduced its energy consumption during the manufacturing process by approximately 2.14 megajoule (MJ) (Table 2), a small but measurable amount.
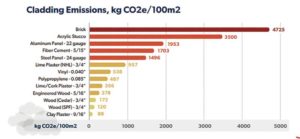
Depending on the type of GPS insulation, the product will either have substantially lower energy consumption during the manufacturing process than XPS insulation or a slightly higher value. For some reason, the freshwater used in the manufacturing process increased by 0.09 m3 (23 gal) moving to the new formulation of XPS insulation and represents a freshwater usage which is roughly 40 times higher than a GPS insulation.