The practical side of window replacements
by Jonathan Dickson, P.Eng., BSS
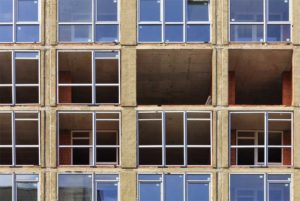
Windows are a critical component of buildings. While they are arguably less energy efficient than the opaque wall alternative, the benefits of windows to building occupants cannot be ignored. Windows are necessary to connect occupants with the outdoors. They bring in light and provide a potential for natural ventilation—both have positive health impacts and improve worker efficiency in office settings. Unfortunately, the installation of a window requires the creation of a hole in an otherwise watertight building envelope, thereby increasing the potential for leakage.
Much has been written about the performance attributes of various window systems, but the practical considerations of a window replacement project are rarely discussed. This article explores some of them, and how they impact building occupants, property managers, consultants, and contractors. While windows are the focus of the article, the recommendations presented are applicable to all glazing systems.
Why are window replacements required?
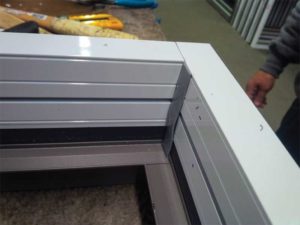
Photos courtesy Pretium Engineering
Window systems are a highly manufactured product as the insulated glazing units’ (IGUs’), gaskets and framing sections are assembled and sealed in a controlled factory setting. The factory-assembled nature of windows is a positive attribute, as human error and weather-related factors are less likely to impact the product’s quality, resulting in a system with a less variable service life than those assembled onsite. A consequence of this manufacturing process is the difficulty encountered during rehabilitation if the primary seals of the window system (those installed between framing sections at the time of assembly) fail (Figure 1). Conversely, site-built assemblies (curtain wall excluded) generally provide easier access to primary seals without the same level of deconstruction required for a window system.
A common approach to addressing a failed window seal would be application of sealant on top of the joint, while the failed internal sealant remains in the system in lieu of deconstruction and reassembly of the window frame. Elastomeric sealants are suitable products but can only be used to address leaks for a certain period of time. This surface application of sealant is a short-term approach to repairing the leak and can only be repeated so many times before building occupants are inconvenienced and potential for damage to adjacent wall elements prevail (Figure 2).
In addition to water leaks, window replacements may also be warranted to address non-water related issues such as thermal comfort, condensation, esthetics, or functionality.
What should be considered during window system selection?
Window systems come in a variety of framing materials, finishes, and IGU compositions and operation types. Many of the options for selection are related to their performance, which is not the focus of this article.