The practical side of window replacements
Floor-by-floor
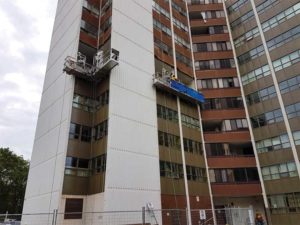
The floor-by-floor method would see all glazing systems on a single level (or large sections of a floor) being replaced at a single time (Figure 4). This option has multiple advantages such as:
- overall inconvenience to building occupants is reduced as individual spaces need to be accessed for only a few consecutive days to complete work (potentially on multiple elevations);
- minimal security is needed as all crews are on the same floor at a single time;
- efficient execution of sequenced work or multiple scopes of work (e.g. balcony guards and slabs, overcladding, cladding repairs, etc.) as all crews are within the same work area and have access to a larger surface area; and
- easier execution of strip window assemblies or other glazing systems that tie together horizontally.
There are also disadvantages to this method of execution. The primary disadvantage would be that this method is not always practical. If multiple elevated platforms (e.g. swing stages) are used in parallel to complete work sequentially, floor-by-floor requires all crews to operate at the same efficiency. If a crew works slower or a platform is not used due to mechanical or weather delays, the whole process slows down to accommodate everyone. Often this method starts as a floor-by-floor execution but quickly transforms into a hybrid model as one crew carries onto the next floor due to delays by other teams. If it is mandated that all the work must be carried out on the same floor, the project cost increases accordingly to account for foreseeable delays.
The floor-by-floor method can also be carried out by mast climber with its own set of practical considerations (discussed later).
Drop-by-drop
The vast majority of window replacements in occupied buildings are completed using a drop-by-drop approach. In this method, a suspended platform is used to replace all windows sequentially on a specific vertical drop of a building before moving to another location (Figure 5). This procedure is often used with multiple platforms (most commonly swing stages) on different drops at a time. As a result of the use of multiple independent platforms, this execution method is more practical than floor-by-floor. Conversely to the floor-by-floor, this method requires more interior security as crews are on multiple floors at the same time and will also result in more inconvenience to occupants as the same space will need to be accessed multiple times (often weeks apart) to replace windows at different locations.
How should the exterior be accessed?
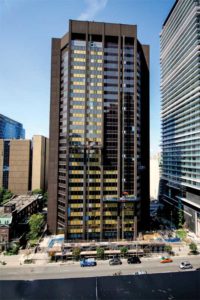
Accessing the exterior of a mid- or high-rise building makes up a large portion of the overall cost of a window replacement project. Access is an important aspect to consider as it has potentially large implications to project schedule and cost. The exterior of tall buildings can generally be accessed in one of two ways: swing stage or mast climber.
A swing stage is a counterbalanced, suspended work platform tied back to the buildings anchor system at the roof level. The swing stage is often the least expensive means of exterior access to carry out work and offers the most flexibility. However, there are exceptions where a mast climber warrants consideration. A mast climber is expensive and would likely not be cost effective unless a more holistic rehabilitation program is being untaken (e.g. balcony or wall rehabilitation and over cladding), or if the glazing area is a substantial portion of the wall. A mast climber is beneficial when an extensive amount of work is required within the same horizontal line. Horizontal strip windows and curtain wall systems are prime candidates for a mast climber if the building orientation is conducive to the use of one. A swing stage may also result in a longer schedule if a project constraint is to minimize interior transportation of materials. For example, existing windows are to be removed and all new materials are to be brought to the work area via swing stage. Since swing stages typically have a weight capacity of around 454 kg (1000 lb) and require two persons for operation, the glazing system is often brought to the ground before the platform is loaded with the new system, potentially increasing the timeline compared to a mast climber.
A mast climber rests on grade with intermediate lateral tie backs to the building (Figure 6, page 40). Most of the tall buildings facilitate underground parking, meaning the weight of the mast climber rests on a suspended slab (podium deck). This requires shoring of the underground levels to carry the weight of a mast climber that is intended to carry several people and hundreds of pounds of materials. At-grade building features, such as awnings or canopies, and pedestrian and vehicular traffic need to be considered. If the building contains multiple overhangs, changes in plane, balconies, or terraces, the mast climber becomes less practical compared to swing stages that more readily adapt to these conditions. A single mast climber needs to follow a floor-by-floor approach and since all workers are on the same platform, the potential for one crew to work ahead of the others is minimized. The mast climber is also less susceptible to wind-related delays, thus allowing for a less variable schedule.
While the contractor controls means and methods for execution of the work, a specifier is recommended to ask for alternate pricing during the tender phase to allow for an educated decision on means of access and its impact on project time and cost.