The pillars of concrete strength: Unveil the crucial steps to perfect concrete
By Chris Bennett, iSCS, CDT and Keith Robinson, RSW, FCSC, FCSI, LEED AP
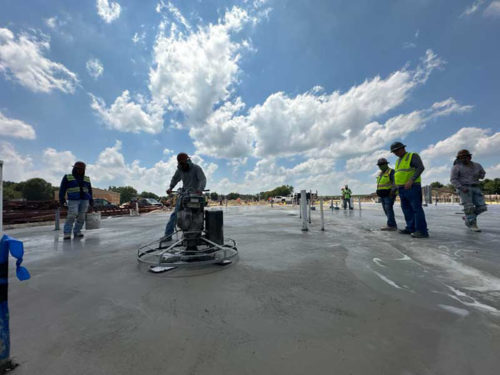
Just as successful specifications enjoy the four attributes of being clear, concise, correct, and complete, concrete also has four steps that are crucial to its success. Those steps are: mix design, consolidation, finishing, and curing. If the four steps work together in concert, the outcome is low porosity, strong, sustainable concrete. However, make changes to one step and not judicious adjustments to the others, and one will find themselves out of step, over budget, and in trouble.
CSA A23.1 states it is the general contractor or construction management teams responsibility to prepare a “Concrete Plan” that defines the expected roles and responsibilities of all parties contributing to the quality of concrete, including mix design, consolidating, finishing, and curing. However, it is up to the entire team to understand and execute this process together, employing performance driven methods, to successfully arrive at design intent.
Mix design
The first step, mix design, is the process of determining the ideal proportions of cement, water, aggregates, and additives to produce concrete that meets a project’s specific requirements. ASTM C 125, Standard Definition of Terms Relating to Concrete and Concrete Aggregates, explains concrete is a composite of cement and embedded fragments of aggregate (rock and sand). When combined with water, the cement binds the materials together creating concrete. The quality and properties of raw materials, including supplementary cementitious materials (SCMs), can vary significantly, affecting the consistency and strength of the concrete mix. The mix design is critical for targeting desired strength, workability, and other properties.
Then the mix design must be carefully adjusted to meet site-specific conditions, such as temperature, humidity, and wind. ASTM C94/C94M, Standard Specification for Ready-Mixed Concrete, provides basic guidance on mixing concrete thoroughly to ensure uniformity and workability. A well-designed mix is essential to ensure the longevity and strength of the structure. It is important to bear in mind that new types of concrete mixes, such as those intended to reduce carbon dioxide emissions, may fundamentally change the behaviour of concrete (i.e. water demands, workability, set times, etc.) and must be handled differently than traditional approaches to avoid dry-shrinkage, deflection, and other potential problems.
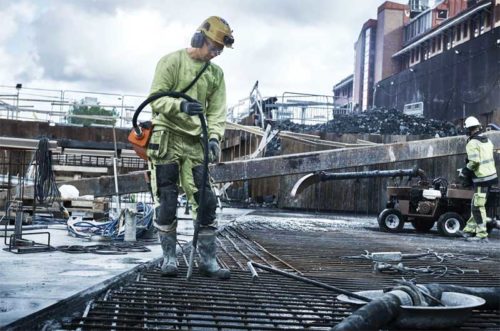
Consolidation
Consolidation (also called compaction) is the process of packing and moulding the concrete within the forms and other structural elements, removing any trapped air pockets that can weaken the concrete’s overall strength. Consolidation is critical because elimination of any gaps or voids in the concrete leads to more uniform strength and higher density. Improper consolidation results in a weaker concrete structure that can fail. ASTM C138/C138M, Standard Test Method for Density (Unit Weight), Yield, and Air Content (Gravimetric) of Concrete, provides instructions for the consolidation needed to produce concrete that can withstand loads and stresses and limit cracks, defects, and avoid shorter life cycles.
Concrete, especially high-consistency mixes, can be over-consolidated, usually from over vibration. In these instances, a thick film of water will form on the surface. This water can negatively impact the concrete with reduced surface strength, lower permeability, and poor esthetics. Seth Mailman, a project manager at Baker Concrete, says, “Concrete placed without proper consolidation will not perform as expected. Understanding the relationship between design and construction with respect to concrete is necessary to ensure the final product performs as expected.”
Finishing
The third phase, finishing, is the process of smoothing out the surface of the concrete to achieve a desired performance texture and appearance. The American Concrete Institute (ACI) 301-20: Specifications for Concrete Construction is a solid starting point for information on finishing to make attractive, durable concrete surfaces capable of resisting abrasion, weathering, and other physical stresses. Finishing helps with setting, prevents chipping, and is climacteric to both decorative and industrial polished concrete surfaces.
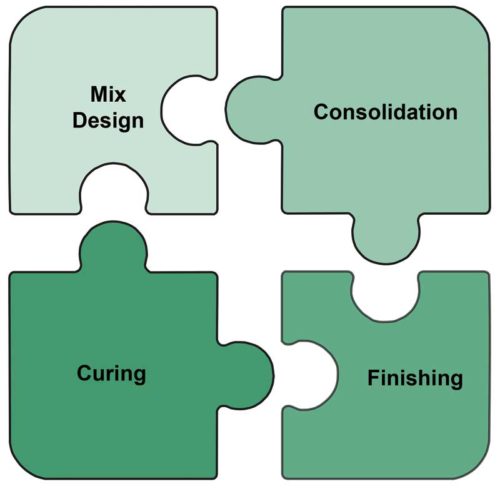
Types of finishes
- Broom finish: Brushing a broom over the concrete’s wet surface will create a noticeable textured groove. This is a long-accepted finish for exterior concrete.
- Bull float finish: A bull float is a tool used by a finisher to spread and smooth concrete before initial set is achieved. A bull full float finish is the texture left behind by the smooth paddle facing of the bull float without additional screening or trowel work.
- Sand finish: A sand finish involves removing the cream off the surface of the concrete so the sand just below is exposed to become the new surface. This can be beneficial for exterior locations in climates that deal with significant freeze-thaw swings.
- Salt finish: Rock salt can be rolled across/into the surface of fresh concrete and then washed off after final set to create a subtle texture with enhanced skid resistance.
- Stamped finish: Stamped concrete has been imprinted to resemble brick, slate, flagstone, and other material types through texturing and pattern moulds that are stamped into the concrete.
- Trowelled finish: By using either a hand or power trowel, a trowel finish is executed by the smoothing and compacting of the unformed surface of fresh concrete.
- Polished finish: A polished finish is a higher degree of trowelling in which the concrete is further refined for esthetics and abrasion resistance. It is worth noting that polished concrete on existing slabs requires the concrete’s surface to return to a semi-plastic state through the creation of slurry to achieve maximum refinement and maintain surface integrity.
A polished concrete finish is most successfully achieved through the specification of surface micro texture (SMT) performance benchmarks in Part 3 of concrete specifications section. As an example, a hard trowel finish may be specified to meet an average 2 to 1 micrometer (µm) (80 to 40 microinches [µin]), as measured by ASME B46.1-2019, Surface Texture (Surface Roughness, Waviness, and Lay), ahead of the polished concrete contractor’s final benchmark (i.e. 0.7 to 0.2 µm [30 to 10 µin]).
For readers unfamiliar with surface micro texture performance, the average roughness (Ra) is a measure of the surface roughness (micro texture) of a material, such as concrete. A higher Ra value indicates a rougher surface, and a lower Ra value means a smoother surface. This can affect appearance, durability, and other performance aspects of the concrete. Ra can also be useful in evaluating other concrete surface qualities to ensure proper surface preparation, treatments, and performance of applied systems.
Owner of Premier Concrete Contractors, Eric Traffic, says, “It is eye-opening to measure Ra after final trowelling on a floor. There are differences between finishers, equipment, and blades. A concrete slab can be finished with more precise Ra tolerances using proper finishing aids and logical mix designs, and paying attention to blade and tool selection. This leads to denser slabs with higher abrasion resistance and lower porosity.”
Finishing requires skilled and experienced professionals to oversee and execute the work. A well-finished concrete surface will reduce the need for maintenance and repairs over time, increase the structure’s lifespan, and produce a strong, good-looking surface. Contractors must be required to attend necessary training to ensure their skill set aligns with performance demands. Failure to do so may result in defaulting to old routines, which can compromise the harmony of finishing tasks with other important steps.
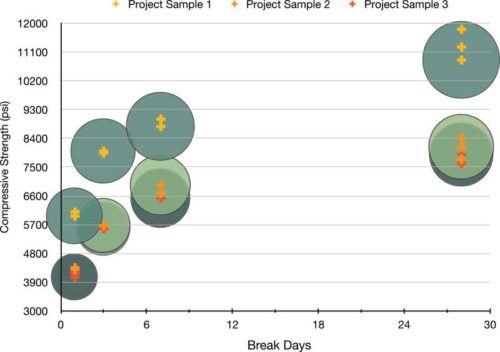
Curing
Curing, the final and culminating phase, is the process of allowing the concrete to harden and reach its full strength by controlling temperature and preventing the loss of moisture. Proper curing is essential, as it affects the final strength, durability, and quality of the concrete. Curing should be reviewed and updated with each project, not simply doing whatever has been done before.
The approach to curing will be informed by the needs of the individual components of the mix
(i.e. slag, limestone cement, calcined clay, reclaimed versus standard fly ash types, etc.) to ensure water demands, alkalinity, milling quality, and other factors are accounted for. All too often, this last step is under considered and creates most of the problems with volume change (i.e. cracking, curling, etc.). As Tyler Ley, PhD, a civil engineering professor at Oklahoma State University, says, “The most common curing of all is not curing.”1
The curing process starts right after placing and finishing (including consolidation) and helps maintain the right moisture and temperature levels to ensure the desired strength of the concrete. If executed properly, curing will aid in developing the concrete’s full strength and durability. If done incorrectly (e.g. allowing the concrete to dry too quickly as is common in North America), it can weaken the structure and lead to cracking and other malformations. In addition, insufficient curing can lower abrasion resistance and lead to early deterioration of the concrete surface. How long the concrete will need to cure depends on several critical factors. They include the following:
- Mix design (mixture proportions)
- Specified strength
- Weather conditions
- Current and future exposure conditions
- Size and shape of the concrete system produced
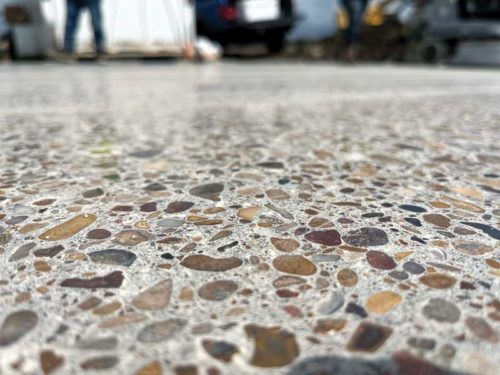
Recommendations for minimum periods of curing from the ACI are generally around the time concrete reaches 70 per cent of the specified compressive strength. This minimum level can take shorter or longer periods of time depending on the aforementioned factors as well as what manner of curing the team uses. There are many different approaches to curing. They vary in cost of application as well as effectiveness. Wet curing has long been the gold standard for concrete among many contractors, but its cost and schedule demands often lead project teams to choose lesser performing methods. In recent years, internally cured concrete (ICC) used in various projects, has developed beyond lightweight clay and shale aggregates to include cellulose fibres (CF), nano modified cements (NMC), certain nano silicas, and other technologies that are proving more cost effective while delivering wet cure-like results in more time effective manners.
Higher curing temperatures can assist in achieving early strength gains, but certain temperatures can also decrease strength. Curing in extreme hot or cold weather requires additional care and preparation. ACI 306.1, Standard Specification for Cold Weather Concreting and ACI 306R, Guide to Cold Weather Concreting are reliable sources for this issue.
Low carbon concrete curing
While ASTM C31/C31M, Standard Test Practice for Making and Curing Concrete Test Specimens in the Field, provides a starting point for traditional concrete placement, it has not, as of yet, been sufficiently updated for low-carbon concrete, respecting the impact to massive cement reductions and the changing qualities of supplementary cementitious materials.
Low carbon concrete is a new material. Treating it like old concrete (i.e. using older curing, consolidating, and finishing methods) will manifest a variety of problems including delayed day of strength requirements, more change orders for repairs, and increased potential for ironically shorter life cycles, therefore defeating sustainability objectives.
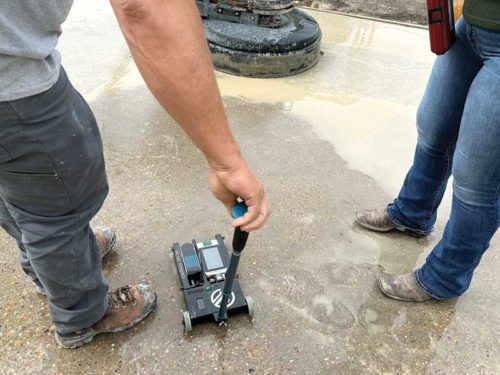
Chris Forney, principal at Brightworks Sustainability says “There are three simple indicators a plan’s low carbon plan might be deficient, 1) longer than normal curing schedules, 2) delayed day of strength, and 3) significant budget increases, all of which may push owners away from opting for low-carbon concrete solutions. Resolving these deficiencies within increasingly aggressive project schedules requires a more careful, organized, and disciplined approach, which a concrete commissioning process offers. Structure and discipline are established with specified clear, measurable performance objectives, followed with field verification, and setting up a “team structure” that is prepared to recognize and resolve deficiencies along the way including missing any steps. This more careful approach will not only win the day but unlock more project-on-project improvement portfolio-wide.”
Approaches, such as ICC, are proving promising in meeting the challenges of low carbon concrete, including earlier strength gains, but also it creates the need for substantial updates to documentation and planning. Construction professionals should also update themselves, setting aside earlier experiences and habits to approach low carbon concrete as a new subject and allow them to learn and become students again.
Architect Kristina Abrams, notes, “If we, as architects, treat low carbon concrete the same way we approach traditional concrete, we will not truly benefit from innovation and cost savings.” Teams should research which approaches are most beneficial for their circumstances and keep in mind the low carbon concrete field is still relatively new. Supplier teams must take responsibility for providing products and materials that can meet the requirements of each of the four steps of concrete production. This is crucial to prevent extended cure times and ensure the production of high-performing concrete.
Protection and usage
Finally, the often overlooked and essential component is protection of concrete once it is cured. Cured does not mean concrete is “good to go,” strength gain can be greatly impaired by leaving concrete left to the elements, being wetted by inclement weather, freezing conditions, or high heat. The Concrete Plan must account for and provide equipment and materials necessary to protect concrete during delivery, placing and finishing, and curing from heat/cold, wind, precipitation—anticipating these conditions could change throughout a scheduled placement.
In addition, the Concrete Plan has to account for the proposed usage of the concrete—based on the needs of floor covering trades, or special finishes applied to the concrete (polished, stained, ground, high performance coatings); or the way the floors will be used, which could require a level of performance for ultimate floor flatness/floor levelness (FF/FL) that exceeds normal work practices.
Conclusion
It is worth nothing, these recommendations are just a starting point and will vary depending on project-specific requirements. It is proper to consult with a qualified commissioning agent or concrete specialty group to determine the appropriate standards and specifications for each project, and be aware of local building codes and regulations which may impact the course of action. At the same time, materials must adhere to established standards, meet the desired results outlined in building codes, and fulfill owner requirements, all supported by scientific data verification.
An informed concrete crew is a treasure to be protected and coddled, a band of disparate workers poking away at the concrete can lead to expensive rework. There is nothing more expensive to a project than pulling out the concrete (i.e. demolition and start over). It is better to make mistakes on paper than in the final work result.
At the same time, designers need to understand the many recipes and ideas marketed to them may look good on paper, but they also just might be creating hardships on the job site. Each step (mix design, consolidation, finishing, and curing) must be carried out with care and precision, and all teams on the project must understand the four steps are related and that success (or lack thereof) in one step can affect the others. Brandon Godbey of Tao Group believes individuals throughout the architecture, engineering, and design process are increasingly recognizing that concrete, despite being produced on-site, can adhere to scientific standards and contribute to the meticulous crafting of high-quality concrete in all aspects.
A well-designed mix with proper consolidation, finishing, and curing can create an attractive and robust concrete structure that can withstand various forms of stress and damage and offset potential budget increases. Data is the only way to protect design intent and collaboration between all team members is paramount to success and increases the likelihood of all four steps concrete working together.
Notes
1 Watch the video on curing, www.youtube.com/watch?v=1siLxrpm_PE.
2 To learn more, visit Prez.is/concrete.
References
- Waco ISD concrete innovation, www.kwtx.com/2023/10/11/waco-isd-holds-demonstration-introducing-new-construction-method.
- An Unusual Approach to Low-Carbon Concrete, www.greenbuildingadvisor.com/article/an-unusual-approach-to-low-carbon-concrete.
- Renovated Waco ISD elementary schools, wacotrib.com/news/local/education/kendrick-south-waco-new-school-designs/article_bb6d0618-2d8c-11ee-8db8-071220f8948f.html.
- Internally Cured Concrete at 415 Natoma www.constructionspecifier.com/concretes-cobra-effect-unintended-results-of-embodied-carbon-reduction
- Healthy Concrete Systems: www.construction specifier.com/healthy-concrete-systems-defending-design-intent.
Authors
Chris Bennett is the founder and CEO of Bennett Build, an industry-recognized leader in concrete consulting and project concrete commissioning. His firm represents owners and assists their project teams in decreasing overall concrete costs and risk, reducing the most embodied carbon possible, and providing the highest quality concrete available. Bennett will be sharing findings from Kendrick Elementary with the Kendrick team this Fall at the 85th annual TxA Conference and Design Expo.
Keith Robinson, RSW, FCSC, FCSI, LEED AP, is an architectural technologist and specifier based in Edmonton, Alta. Robinson instructs courses for the University of Alberta, acts as an advisor to several construction groups, and sits on many standards review committees for ASTM and the National Fire Protection Association (NFPA). Robinson was a key driver in the hands-on research at University of Alberta’s Concrete North with the Donadeo Innovation Centre for Entering Excellence (ICE), as well as early field testing of commercial internally cured concrete in North America.
Together, Bennett and Robinson have developed specification improvements within the concrete scope, written numerous articles on concrete as well as presented at CSI Construct, World of Concrete, Concrete North with University of Alberta, Praxis Events Live!, and the National Concrete and Corrosion Symposium with Kent State University and University of Akron NCERCAMP.