The path to zero: Concrete’s role in decarbonizing the built environment
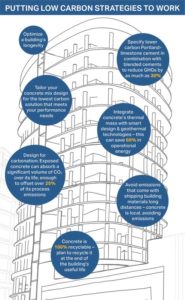
Importantly, PLC is complementary to other carbon-reducing strategies, such as using supplementary cementitious materials (SCMs) like fly ash and slag. Together, PLC and SCMs can achieve carbon-intensity reductions of 30 to 40 per cent.
All cement producers in Canada are now able to manufacture PLC and it has been fully recognized in the Canadian Standards Association (CSA) cement standards and building code. While there are no technical barriers to the adoption of PLC, its market penetration has been hindered by resistance to change, a function of the inherent conservatism in the construction community.
Carbon capture, utilization, and storage
One of the most exciting developments in the cement and concrete industry in recent years has been the explosion of carbon-capture technologies.
Carbon capture offers a complete solution to cement GHG emissions, with the potential to capture virtually 100 per cent of the emissions from both the cement industrial and combustion processes. Captured emissions can then be stored underground or used to make other products like CO2-neutral synthetic fuels and aggregates. The latter can replace virgin aggregates used in concrete.
For many years carbon capture has been viewed as a kind of ‘Hail Mary’ pass for the coal-fired utility sector. In fact, SaskPower’s Boundary Dam coal-fired power plant in Saskatchewan is among the most well-known full-scale carbon capture systems in the world. However, the long-term success of carbon capture hinges, to a great degree, on its commercial application in the cement sector. This is, in part, because cement kilns produce a high concentration stream of CO2 making it efficient to capture. Additionally, the captured carbon dioxide can be used as a material input in the concrete manufacturing process.
Several cement facilities in Canada are well advanced in the implementation of carbon capture systems. For example, a cement manufacturer has undertaken a $3 million advanced feasibility study for full-scale carbon capture system at their Edmonton, Alta., cement facility. Another manufacturer recently completed the installation of a flu gas pre-treatment system at their Richmond, B.C., cement facility, paving the way for a full carbon capture system.
Examples of carbon capture, utilization, and storage (CCUS) technologies include:
- Solidia, which uses captured carbon to make a new type of concrete that cures with CO2 instead of water, reducing the carbon intensity of the concrete by up to 70 per cent and potentially making concrete water-neutral (it also makes concrete stronger and faster to set);
- CarbonCure, which injects liquid CO2 into curing concrete to make it stronger with less cement;
- Pondtech, which is an algae-based carbon capture and scrubber—the algae purify the flue gas and suck out carbon as they grow (the harvested algae can then be used to make biofuels, agricultural products, and even rare pigments); and
- Blueplanet, which uses captured CO2 to carbonate the waste products of other industrial sectors to make engineered aggregates that can replace virgin aggregates in concrete while permanently sequestering significant volumes of carbon in concrete products (CO2 is released when harvested algae is used to make biofuels, agricultural products, and rare pigments. However, one can achieve a net CO2 benefit by displacing fossil CO2 with CO2 that has in effect been ‘recycled,’ making the process carbon neutral. In other cases, the captured CO2 would be permanently sequestered).
Most promising, if the industry is successful in its goal of manufacturing carbon-neutral cement, and if carbon-capture technologies are combined with other low-carbon materials, such as biomass fuels or carbonated aggregates, concrete could transform into a carbon-negative building material.
Conclusion
For anyone concerned about climate change, it is self-evident building practices need to change—material manufacturers, specifiers, architects, developers, and engineers need to work together at each stage of the construction process to lower embodied carbon while producing ultra-efficient, durable, and climate-resilient buildings and infrastructures.
Adam Auer is vice-president, environment and sustainability, at the Cement Association of Canada (CAC). Auer has almost 20 years of experience as a sustainability professional. In his role at CAC, he works with government, industry, environmental, and other civil society groups to promote and enhance concrete’s contribution to sustainability, with an emphasis on life-cycle approaches to climate change mitigation and adaptation. Auer holds a master’s degree in environmental studies from York University and a bachelor’s degree in ecology from the University of British Columbia. Auer can be reached at aauer@cement.ca.