The path to zero: Concrete’s role in decarbonizing the built environment
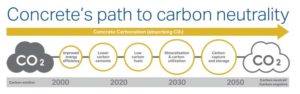
Images courtesy Cement Association of Canada
On this note, there are now several important initiatives to help provide greater transparency, consistency, and robustness in accounting for embodied carbon. In Canada, one of the most promising and significant will be the National Research Council’s (NRC’s) Low Carbon Assets through Lifecycle Assessment (LCA2) initiative. LCA2 aims to establish a definitive regionalized life-cycle data inventory for the country, including filling gaps in how LCA accounts for biogenic carbon from wood products as well as the carbon dioxide (CO2) that is naturally absorbed by concrete over its life (recent research suggests concrete can absorb over 25 per cent of the CO2 process emissions associated with its cement over its full life cycle).
The timing makes this all the more important, with Architecture 2030 estimating that between now and 2050, embodied carbon could represent as much as 50 per cent of the total life-cycle GHG emissions from new, energy-efficient structures. Importantly, and in contrast to operational emissions, these upfront emissions are released entirely at the beginning of a building’s life.
As the spotlight has begun to focus on upfront carbon, building material manufacturing sectors are taking note, and none are underestimating what a low-carbon transition entails for their respective sectors. For steel producers, it could mean a wholesale conversion to electrification and recycled content. For wood, it likely means a full retreat from logging the intact boreal and coastal rainforests and more rigorous, transparent accounting to support carbon-optimized forestry practices.
For cement and concrete, the challenges are significant, but the pathway is clear.
Decarbonizing concrete starts with cement
Cement is the active ingredient in concrete and while it makes up only 10 to 15 per cent of concrete’s recipe, it is responsible for 80 per cent or more of concrete’s GHG emissions. Decarbonizing concrete is largely a matter of decarbonizing the cement manufacturing process.
Canada’s fleet of cement facilities are relatively modern, taking advantage of the latest energy-efficient technologies (e.g. preheaters and pre-calciners, waste heat recovery systems, etc.) and pollution abatement equipment. However, when it comes to reducing GHG emissions, a number of opportunities are being actively pursued.
Cement is made by superheating limestone in a long rotary kiln to make an intermediary product called clinker. Clinker is mixed with ground limestone and gypsum to create Portland cement, and then added to sand, gravel, water, and sometimes other additives to make concrete.
The most obvious sources of GHGs are the combustion emissions coming from fossil fuels (a mixture of coal, petcoke, and natural gas) used to heat the kiln. The combustion accounts for about a third of cement GHG emissions. These can be reduced through fuel substitution and carbon-capture technologies.
Less commonly known sources of GHGs from cement are the carbon emissions coming from the chemical reaction taking place in the kiln. When limestone is super-heated to 1450 C (2642 F), it releases its carbon as CO2, making available the chemical bonds required to make clinker. These account for two-thirds of cement GHG emissions. They can only be reduced at the facility with carbon-capture technologies or at the product level (i.e. in concrete) by minimizing the amount of clinker used in the cement and/or replacing cement with supplementary cementitious materials in concrete to make low-carbon cement formulations.
Low-carbon fuels
The easiest and most economical way to reduce cement manufacturing emissions is by substituting a portion of fossil fuels used in the kiln with lower carbon alternatives (some facilities have achieved 100 per cent substitution. However, a mix of fossil and non-fossil fuels is more typical). Among the best alternatives are waste-derived fuels, such as construction and demolition waste (which is mostly wood), rail ties, biosolids, as well as unrecyclable tires, tire fluff, and non-recyclable plastics. In fact, because cement kilns have high temperatures and fuels linger in them for a long time, they are ideal end-uses for hard-to-manage wastes. Importantly, these fuels reduce GHG emissions (from ~15 per cent for tires to 100 per cent for biogenic fuels like waste wood) and have no impact on other air emissions (some alternative fuels also reduce nitrogen oxides [NOx] emissions).
Canada’s fuel substitution rate has historically been quite low (between seven and 10 per cent) compared to Europe, where the average is over 40 per cent and often much higher. A major impediment to leveraging the benefits of fuel substitution in Canada has been the difficulty in obtaining provincial permits to use non-traditional fuels; provincial permitting systems for industrial fuel are simply out of sync with waste management policies that dictate how potential waste-derived fuels must be handled. However, as addressing climate change becomes a priority along with an increased emphasis on ‘circular economy’ solutions to waste management, the cement sector is confident it can reach substitution levels meeting or exceeding best practices—with the potential to reduce the carbon intensity of Canadian cement by over 20 per cent. In fact, Canadian cement facilities have invested over $100 million in low-carbon fuels in the past several years.
Low-carbon cements
The second significant near-term opportunity to reduce the carbon intensity of cement is the transition to Portland limestone cement (PLC). It substitutes some of the carbon-intense clinker in regular cement with finely ground unprocessed limestone, offering a type that is a functional and cost-equivalent substitute for regular cement, but with up to 10 per cent fewer GHG emissions. It is the industry’s ambition to make PLC the default cement across Canada, reducing emissions by almost 1 million tonnes annually.
MIND THE CARBON GAP |
Carbon is complex, and discussions about the embodied carbon and carbon emission implications of building materials are too important to get wrong.
All materials have a role to play in creating more sustainable communities and we need to rely on science to ensure our plans to cut carbon deliver those results. The “Emission Omissions: Carbon accounting gaps in the built environment,” a new study by the International Institute for Sustainable Development (IISD) found gaps in how carbon is being measured in building products such as steel, concrete, and wood.* They concluded that because life-cycle assessment (LCA) models do not account for biogenic carbon losses, they effectively omit up to 72 per cent of a wood product’s carbon footprint, enough to erode wood’s perceived carbon advantage.** According to this study, these gaps could be serious enough to misdirect efforts to reduce carbon in the built environment and change the outcome of carbon comparisons from “advantage wood” to “advantage concrete”. The IISD study concluded LCAs are still the best approach to measure carbon emissions in buildings but that more data, transparency, and robust standards are needed, especially with respect to unaccounted biogenic carbon. * Visit www.iisd.org/library/emission-omissions. ** Biogenic carbon dioxide emissions are defined as emissions from a stationary source directly resulting from the combustion or decomposition of biologically based materials other than fossil fuels. |